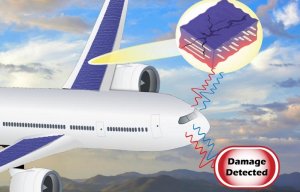
ORNL develops self-sensing composites
Scheduled for completion in September 2015, the 100-ton custom press by the leading hydraulic press manufacturer will feature a 36”x36” work area.
10th July 2015
Innovation in Textiles
|
St. Louis, MO
Oak Ridge National Laboratory (ORNL), a leader in the research and development of advanced materials and economical green energy solutions, has awarded Beckwood Press Company a contract to manufacture a custom hydraulic press for the compression moulding of various composite materials.
The research and development efforts made on the press will ultimately contribute to automotive and aerospace industry light weighting efforts, intended to produce higher performance products with improved fuel efficiency.
Scheduled for completion in September 2015, the 100-ton custom press by the leading hydraulic press manufacturer will feature a 36”x36” work area and integrated multiple zone heated platens for precision temperature control.
In addition to the custom hydraulic press, ORNL will install a Triform Model 16-5BD Fluid Cell sheet hydroforming system (also manufactured by Beckwood), which features 5000 PSI of maximum forming pressure and a 16” diameter forming area.
The Triform 16-5BD is said to allow for the formation of complex geometries with the use of a pressurized diaphragm, which can be programmed to apply a range of forming pressures to accommodate the various materials being formed. The inherent flexibility of the Triform process – which includes the ability to dwell, or maintain pressure on the part for extended periods of time – along with the ability to use inexpensive tooling, will enhance ORNL’s ability to conduct critical material and manufacturing-process research.
“It is our goal to make this lab the intersection of our 3D printing capabilities and composites processing,” said Jesse Smith, Manager of Industrial Partnerships & Economic Development Science & Technology Partnerships at Oak Ridge National Laboratory. “It is going to be a very impressive showplace for industry, and we are excited to have Beckwood on our team.”
The Beckwood machines will be used at ORNL by the Institute for Advanced Composites Manufacturing Innovation (IACMI). Led by the University of Tennessee and headquartered in Knoxville, the IACMI’s main goal is to develop new low-cost, high-speed, and efficient manufacturing and recycling process technologies that will promote widespread use of advanced fibre-reinforced polymer composites.
Through the new IACMI Institute, a world-class team of leading industrial manufacturers, material suppliers, software developers, government and academia will focus on lowering the overall manufacturing costs of advanced composites by 50%, reducing the energy used to make composites by 75%, and increasing the ability to recycle composites by more than 95% within the next decade.
“Beckwood is honoured by every partnership we forge,” said Jeffrey Debus, Beckwood’s President. “Manufacturing organizations rely on our 40 years of experience to provide advanced manufacturing solutions that increase their capability, and competitiveness in the marketplace. But this particular Department of Energy opportunity, and the long-term impact their research & development efforts could have on the automotive and aerospace industries, is special.”
Business intelligence for the fibre, textiles and apparel industries: technologies, innovations, markets, investments, trade policy, sourcing, strategy...
Find out more