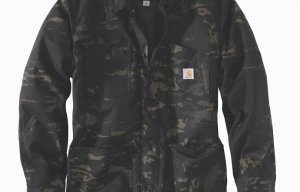
Cordura and Carhartt celebrate collaboration
World’s first bio-based 3D-printed neighborhood now planned for Maine.
30th November 2023
Innovation in Textiles
|
Maine, USA
BioHome3D, the first 100% bio-based 3D-printed home, is proving to be a viable solution to the growing housing crisis after a year of outdoor testing.
Printed at the University of Maine’s Advanced Structures and Composites Center (ASCC), the prototype is poised to set new standards for structural integrity, carbon footprint reduction and next-generation manufacturing.
BioHome3D is a 600-square-foot home that was designed to meet Maine’s affordable housing requirements. It was created entirely with wood residuals, bio-resins and wood fibre insulation. Due to its renewable materials, the home, which includes one bedroom and one bathroom, is fully recyclable and acts as a carbon sink.
The construction industry accounts for 39% of global carbon emissions. Sequestering 46 tons of carbon-dioxide for each 600-square-foot unit, BioHome3D stands as a pivotal solution for the construction industry. This technology addresses both operational and embodied carbon, and sets precedents for both sustainable construction material production and manufacturing.
During its inaugural year, BioHome3D endured one of Maine’s most volatile weather perods, with sensors reporting temperatures from 1°F to 105°F, extreme wind storms that caused blackouts throughout the state and a number of snowstorms. It performed very well under rain, snow, temperature cycling and hail. It was designed in accordance with ASCE 7 loadings, and meets the design requirements of the International Code Council (ICC) code.
Scaling up
The ASCC will break ground on the Green Engineering and Materials (GEM) Factory of the Future in August 2024. This research centre is the next step in scaling up BioHome3D production technology.
It is expected to be completed in 2026 and will feature Industry 4.0, AI-enabled, large-scale additive, subtractive and digital hybrid manufacturing technologies developed by UMaine and its federal, national laboratory and industry partners over the past 10 years. It will rely on new collaborative robotics and closed-loop advanced manufacturing equipment and processes, as well as use the new generations of bio-based material systems. It will also provide discovery-driven learning opportunities for the future workforce
“The data collected over a year of outdoor exposure in Maine has proved that the technology is sound,” says ASCC executive director Habib Dagher. “Now, our focus is to scale up the production process. With the Factory of the Future, our goal is to be able to produce one of these 600-square-foot homes every 48 hours. We’ve created a house. Now it’s time to create neighborhoods.”
At the start of construction for BioHome3D, the material was printing at a deposition rate of 20 pounds-per-hour. Over time, production speeds have increased to nearly 500 pounds-per-hour with improvements to the printer. The focus on scaling up production looks to continue to drive costs of materials and manufacturing down to be competitive or less expensive than traditional stick-built homes.
With the new manufacturing facility and advancements in production speed, ASCC is finalising plans to print the world’s first bio-based 3D-printed neighborhood. It will feature nine homes with the BioHome3D technology located in the Greater Bangor area, providing housing for individuals experiencing or at risk of homelessness. A new study reports that nearly 80,000 homes are needed in Maine to fix the deficit and meet demand for affordable housing by 2030, which BioHome3D can help address.
The proposed neighborhood will feature BioHome 2.0, the next generation of houses that take the data and lessons learned and create livable and sustainable homes with research focusing on material advancements, enhanced fire and toxicity resistance and building code approvals.
Wood residuals
By using locally-produced wood residuals, Biohome3D can also support Maine’s forest products industry. Maine’s sawmills produce nearly a million tons of wood residuals every year, which used to go to many pulp and paper mills that have since shuttered. Each 600-square-foot unit requires approximately 10 tons of wood residuals, meaning 100,000 units could theoretically be produced every year using the sawmill residuals. Not all residuals will be used for this purpose, but this provides a sense of the available feedstock resource.
The technology was also designed to address labuor shortages and supply chain issues that are inhibiting the construction of affordable housing, by printing with abundant, renewable and locally-sourced wood fibre feedstock whicg reduces material costs, while making the construction process and final product more sustainable. These locally-produced materials also are more resilient to global supply chain disruptions and labor shortages.
In Maine, around 41% of the construction workforce is nearing retirement, and projected growth won’t bridge the ensuing gaps. Utilizing ASCC’s expertise in next-generation manufacturing technologies has notably reduced reliance on labour and significantly accelerated production, while minimizing waste through precision manufacturing.
BioHome3D has been recognised globally and was awarded the Aubin AM Case Study Award by the Society of Manufacturing Engineers and the Combined Strength Award at the 2023 CAMX Conference.
Business intelligence for the fibre, textiles and apparel industries: technologies, innovations, markets, investments, trade policy, sourcing, strategy...
Find out more