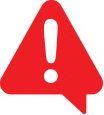
Record printed circuit for UAV
High-precision process removes the need for expensive and time-consuming formwork.
4th December 2023
Innovation in Textiles
|
Zurich, Switzerland
Within the Airlements project, researchers at ETH Zurich in Switzerland have been using 3D printing to produce sustainable insulation elements for buildings – even those with complex shapes.
The high-precision printing process generates less waste and removes the need for expensive and time-consuming formwork and the mineral foam employed was produced by ETH spin-off FenX. It is based on industrial waste and fully recyclable.
“The mineral foam is mostly made from fly ash, a waste product from industrial blast furnaces,” explains Patrick Bedarf, of the ETH Digital Building Technologies group. “The foam has already gone through the first material cycle and can simply be recycled after use and reused. With 3D printing, the formwork needed for pouring material – which is very time-consuming and can only be partially reused afterwards – is no longer required Excessive wastage is a particular challenge when producing more complex geometrical shapes. Without automation, traditional construction methods that save on materials are very time-consuming and expensive, especially due to labour costs.”
A prototype from the project is a monolithic corner column two metres high and made of four 3D-printed segments. The four individual parts are stuck together with mortar and then sprayed with a white cement-free render. The individual parts are easy to lift manually and stack on top of one another.
“The building parts can simply be printed in a factory, transported to the building site and positioned where required,” Bedarf says. “To make the component more robust, the currently hollow core can be cast with high-density mineral foam, making it strong enough to act as a load-bearing structure.”
To date, Airlements can only be used as insulating parts for internal or external walls.
Each individual part is printed in less than an hour and hardened for a week inside the fabrication environment, with a controlled temperature of 20-28°C and relative humidity of 20-70%.
Regulating air humidity and temperature is important to ensure the material hardens correctly and is not prone to fracture and Bedarf has developed a special climatic chamber for this – a large transparent tent-like structure inside which the printing robot moves along the predefined printing path.
“This is an advance on earlier work with cement-free foams, which either had to be hardened with cement or by curing at high temperature in the oven afterwards,” Bedarf explains. “The corrugated texture of the components provides extra stability during the hardening process and in their final state.”
Bedarf will continue to develop Airlements with FenX and a dedicated production line will be built at the company’s factory.
“We will thoroughly analyse the load-bearing capacity and insulation properties to determine how this material acts as a wall element in a closed room,” Bedarf says. “Infrared measurements will help us establish where the thermal insulation could be further improved, and how to eliminate any weaknesses by adjusting the printing path.”
Business intelligence for the fibre, textiles and apparel industries: technologies, innovations, markets, investments, trade policy, sourcing, strategy...
Find out more