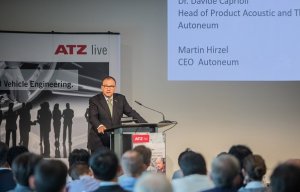
Optimum protection against tire noise with Alpha-Liner
As automotive manufacturers continue to push for improved fuel consumption and lower carbon emissions, they are squeezing every single gram of weight out of every single part that goes into a car. Meanwhile, however, the pressure to save money and create a smoother, quieter driver experience is also increasing.
23rd September 2013
Innovation in Textiles
|
Greensboro, NC
As automotive manufacturers continue to push for improved fuel consumption and lower carbon emissions, they are squeezing every single gram of weight out of every single part that goes into a car. Meanwhile, however, the pressure to save money and create a smoother, quieter driver experience is also increasing.
Greensboro, North Carolina headquartered Precision Fabrics Group, has commercialized a unique nonwoven fabric called Nexus AFR which helps solve the car makers need to improve acoustics and reduce weight without breaking the bank.
The Precision Fabrics solution is based on the ‘physics of acoustics’ and the science focuses on two dominant properties in part design - thickness and resistance to airflow. Because sound moves through air in waves of minute pressure variations, the solution has to work for long wavelengths (low frequency) and for short wavelengths (high frequency).
The thickness of the existing insulation layer is important and determines what low frequency wavelengths can be absorbed. The new Nexus AFR nonwoven material replaces the traditional black scrim on the surface and controls the mid and high frequency wavelength by managing the sound pressure level variations and ‘trapping’ the energy in the insulation layer of the part. This makes the composite more efficient than just the Homogeneous insulation material by itself.
According to Precision Fabrics’ Richard Bliton, this two material approach has many advantages over the traditional homogeneous insulation, one material approach.
“Traditional black scrim - the commodity black scrim used in the auto industry is a descendent of the fabric interlining and lining materials. The typical nonwoven manufacturing technology is a chembond or thermalbond technology,” explains Bliton.
Low cost fibres are carded and oriented primarily in the machine direction and a chemical spray or waterfall coats the web and it is compressed and dried. The web then has a hot melt adhesive powder sprinkled on the face which is to be reactivated during on processing. Properties such as FR or repellency can be added to the waterfall treatment.
“The strength of this type of web is low compared to other nonwoven structures, but the prime advantage is that it is low cost. Most of the purchasing specifications for this type of material only specify- fabric basis weight, colour, width, and amount of adhesive. Acoustic characteristics such as Rayls are not controlled, tested or reported,” Bliton continues.
An example, Bliton says, is an automotive hood liner. A traditional design would have a 30 gsm black nonwoven scrim on the back (B) side, 1600gsm resonated fibreglass about 10mm thick as the insulation layer and a 50 gsm black scrim on the front (A) side.
A recently launched next generation hood liner with Nexus AFR was made up of 30 gsm B side, 600 gsm Fiberglass insulation 10mm thick and 100 gsm Nexus AFR on the face. The weight reduction is 950 grams/m² which is more than 2 lbs/m². In this particular case, the acoustics stayed the same and there was cost reductions generated in the raw material line, and additional improvements in manufacturing related to shorter cycle times required to mould a 600 gsm fibre glass part as compared to a 1600 gsm part.
According to Precision Fabrics Group, the automotive industry is moving quickly to implement this new approach. Parts using the AFR nonwoven are commercial in 10 platforms within 5 OEMs and one major OEM has adopted the low density fibreglass with AFR facing design approach as a worldwide corporate best practice.
The focus on reducing weight and cost is one of the drivers for the adoption of the new material, but in some cases a vehicle may have a sound problem that has to be solved. In these cases, the company says, a properly selected AFR facing can significantly improve that acoustic absorption of the part. The physics based solution offers the acoustic engineer some flexibility to tailor the part to focus the acoustic absorption on mid to high frequency ranges.
“Some of the commercial parts on the road are last minute ‘fixes’ to acoustic problems found during pre-launch road tests. The switch to an AFR facing is an easy change for a part manufacturer and an OEM to make,” Rich Bliton adds.
The new fabric meets or exceeds all of the fabric specifications that are in place, the modified part can be made on the same tooling and the improved part will have the same fit as before.
“The design approach to build a part with low density material for thickness and an acoustically tuned fabric facing for impedance as opposed to the traditional parts where performance was defined by the weight/thickness of the insulation is a new paradigm. The science can be applied all types of insulation materials. Each situation will have to be tuned and validated, but early feedback is generating 30-40% weight reductions without loss of acoustic absorption performance,” Bliton concludes.
Precision Fabrics manufactures, markets and sells value-added products and services to selected, highly specified markets. The company’s high-performance products play a key role in several diverse markets, which demand engineered, finished fabrics, the common thread amongst which is the technical nature of their requirements. Precision Fabrics was the first ISO-qualified textile supplier in the USA. – and ISO continues to provide the discipline and framework for effective and efficient product development, customer service, and manufacturing. Precision Fabrics has been ISO-registered to 9001 since 1993 and upgraded to 9001-2008 in October 2009.
Precision Fabrics was created in 1988 via a leveraged buyout from Burlington Industries and continues as a privately-held company today. The company has evolved from a traditional textile company into an engineered materials business, focused on highly technical, high-quality woven and nonwoven fabrics.
Today, Precision Fabrics employs approximately 600 people and operates plants in North Carolina, Virginia and Tennessee. Corporate headquarters are located in Greensboro, North Carolina and sales offices are maintained in Greensboro and in Bamberg, Germany. Precision’s Vinton, VA, Plant specializes in weaving some of the most technically challenging continuous-filament fabrics in the world. The Greensboro and Madison facilities are world-class in the range of nonwoven products that they produce.
Precision Fabrics Group
301 N. Elm St, Suite 600, Greensboro, NC 27401, USA
Tel. 001 800 284 8071(office)
Business intelligence for the fibre, textiles and apparel industries: technologies, innovations, markets, investments, trade policy, sourcing, strategy...
Find out more