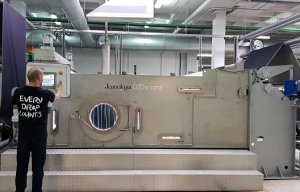
Innovating fabric finishing with G2 Dynamic
High-denier and high-tenacity yarns packed into a very tight pattern to create the roofing industry’s toughest base layer.
20th February 2025
Innovation in Textiles
|
Wooster, OH, USA
FiberTite single-ply roofing membranes manufactured by Seaman Corporation, of Wooster, Ohio, have received an industry-leading 40-year reference service life (RSL) through a cradle-to-grave environmental product declaration (EPD).
This provides commercial property owners and operators further proof of the roofing system’s ability to deliver long-lasting performance.
An EPD is an independently verified document providing transparent, quantifiable data about the environmental impact of a product throughout its life cycle, enabling informed decision making in the built environment to support sustainability goals.
The FiberTite EPD is cradle-to-grave and provides a full life-cycle analysis, from raw materials extraction through to end of life. Comparatively, EPDs for most single-ply roof membranes currently account for only cradle-to-gate environmental impact related only to raw material extraction through the manufacturing stage without accounting for the roofing membrane’s lifetime performance.
“We know that commercial building owners and operators everywhere are looking to make more sustainable choices without compromising their operational security or integrity,” says Peter Kirk, Seaman’s strategic market manager. “This newly-issued EPD is proof that FiberTite can accomplish both goals.”
The 40-year RSL is attributable to high performance in several key areas, including weather, puncture and chemical resistance.
Four-layer structure
FiberTite’s dense four-layer knitted structure contains nearly twice as much fibre as competing products and features an Elvaloy ketone ethylene ester adhesive coat based on a proprietary formula.
High-denier and high-tenacity yarns are packed into a very tight pattern to create the roofing industry’s toughest base fabric layer and the company’s specialised adhesive coating process saturates its individual base fabric fibres, creating a molecular bond between the back and face coats of the membrane. This prevents delamination caused by harsh environments and also keeps moisture from penetrating the cut edges of the membrane and causing seams to fail.
Many manufacturers use a cheap back coat formula that adds thickness and cuts production costs but doesn’t protect well, the company warns. FiberTite uses the same Elvaloy formula in equal weights on the back and face coats for exceptionally secure and lasting welds.
The face coat provides superior UV and chemical resistance, inhibits crazing and cracking, and allows the membrane to remain flexible over the long haul in any rooftop environment. Long-term flexibility makes FiberTite both long lasting and easier to weld for future rooftop modifications.
Business intelligence for the fibre, textiles and apparel industries: technologies, innovations, markets, investments, trade policy, sourcing, strategy...
Find out more