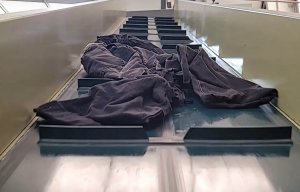
Timely debut for Wastex
Opinion
VDMA webtalk addresses the available options for maximising the value of fibres from post-consumer waste clothing.
2nd April 2024
Adrian Wilson
|
Frankfurt, Germany
The automated sorting of waste clothing has been identified as something of missing link in the European textile recycling industry at present.
This was the subject of the latest webtalk organised by the textile machinery branch of Germany’s VDMA on March 26th, with a focus on activity in France, where an extended producer responsibility (EPR) scheme for textile waste has been in operation since 2008 and further moves are now even afoot to dramatically curb fast fashion via further legislation.
France has been ahead of the curve as the European Union plans to impose an EPR scheme for the mandatory collection of textile waste bloc-wide and the banning of its landfilling or incineration from January 2025, potentially creating a mountain of material that will have to be dealt with.
Refashion
Cécile Martin, innovation and recycling manager of Paris-based Refashion, the non-profit association formed to administer the French EPR scheme, outlined its objectives for the period 2023-2028. These include achieving the collection of 60% of all clothing placed on the French market annually, the 99.5% recovery of sorted post-consumer textiles and the recycling of 90% of this waste by 2028.
Fees imposed by the association on member manufacturers and brands in 2022 were based on 827,000 tons of new product going onto the French market, of which 65% was clothing, 17.5% footwear and 17.5% household linen.
There is still some way to go. Collection in 2022 was 260,000 tons, representing a collection success rate of 31%. The waste that was then subsequently sorted by Refashion’s 67 contracted sorting facilities amounted to 188,000 tons, representing a 23% success rate.
Of this sorted waste, 59.5%, roughly 112,000 tons, was resold or reused, but it’s notable that only 5% was actually reused in France, and 95% was reused elsewhere. A further 31.3%, or 59,000 tons, was given a second life as nonwovens for automotive, construction or wiping applications, or ground down for use in plastics or composites, with only a small percentage unravelled and turned into new yarns for spinners.
Ecomodulation
A notable development of the Refashion scheme has been the introduction of ‘Ecomodulation’ fees which are bonuses for manufacturers who are able to demonstrate either the durability of their products, provide environmental certifications or incorporate recycled materials into their collections. Some €237 million has been allocated to this scheme for the 2023-28 period, which should prove a major incentive for change.
Specifically, products incorporating raw materials from the recycling of post-consumer textile waste collected or funded by an approved organisation will qualify for a bonus of €1,000 per ton, and those made from recycled mill waste a bonus of €500 per ton – significant concessions when considering the huge volumes that can be involved.
Refashion has also undertaken extensive work on the potential recycling routes for waste textiles, with a two-year study run at six sorting facilities and based on mixed materials. Martin emphasised the importance of solid product information on garment labels in speeding up and simplifying sorting procedures.
Technologies
As far as sorting is concerned, Martin explained that NIR (near infrared) spectroscopy is widely employed, using handheld devices or sorting tables in which samples are exposed to electromagnetic waves to establish their chemical signature. With hyperspectral imaging, the detection of non-uniform materials on surfaces is also possible.
Automated sorting lines are meanwhile now manufactured by Pellenc, Picvisa, Tomra and Valvan, with nine such lines currently either fully established or in development in Europe. This includes two in France at CETAI and Synergies, one in Germany at Soex, Texaid in Switzerland, LSJH in Finland, SYSAV in Sweden, Wieland Textiles in Denmark, Coleo Recycling in Spain and the Salvation Army in the UK.
Nouvelles Fibres Textiles
In addition, the fully automated sorting, fibre recycling and preparation and nonwovens production line was inaugurated in November 2023 at Nouvelles Fibres Textiles, in Amplepuis, France, in partnership with Andritz Laroche and Pellenc.
Laroche, which was acquired by Andritz at the end of 2020, has over 2,000 sorting and textile reference projects worldwide, but with an estimated 7.5 millions tons of waste textiles due to be collected across the EU in 2025 (with only 2.2 million tons collected annually at present), the company’s head of sales Charles Junker, observed that the challenge is to be able to automatically classify garments in order to maximise the value of the fibres.
The Nouvelles Fibres Textiles system employs processes for consistently refining the textile waste, starting with a sorting line for full waste garments, a second for cutting and secondary sorting and then on to a cleaning and tearing line.
Junker provided an example of how the system would handle a bale of cotton and polycotton denim waste.
After garment spreading to avoid overlapping, the system can be initially set to separate all cotton items that are more than 90% blue in colour from the rest, removing all non-cotton and other coloured items and producing a second bale.
This is then cut into clips and fed through the second line to remove everything remaining that is not cotton or blue, such as pocket linings, and baled again.
The cleaning and tearing line then removes all other remaining impurities to result in a bale of 98-99% clean fibre.
Junker said the Nouvelles will soon by at the stage of handling three tons of material an hour, and by the end of this year is targeting six tons an hour.
“Mechanical recycling is an immediate response but won’t be the only solution,” he said, adding that Andritz is now working with Rieter on the development of a refined system for the production of recycled yarns and also on chemical recycling treatments. “Nonwovens companies are early movers in looking at the potential of post-consumer waste, realising that there’s going to be a big demand for the cleaner and purer waste from manufacturing operations.”
Spinning
Finally, from the perspective of a yarn spinner, Miklós Nagy project manager at Valerisu Texteis in Portugal, emphasised that the proper sorting of fibres is essential to remove any impurities and contaminants or uneven fibres because only very high-quality fibres can be successfully spun.
“Scalable sorting solutions that can adapt to changing demand levels and accommodate future growth will be highly advantageous,” he said.
The latest VDMA webtalk, along with previous episodes, can be viewed here.
Business intelligence for the fibre, textiles and apparel industries: technologies, innovations, markets, investments, trade policy, sourcing, strategy...
Find out more