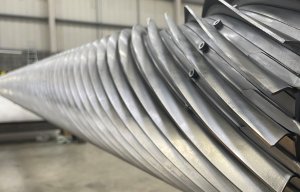
Breakthrough in carpet manufacturing
Opinion
Overcoming the key limitations of current key technologies for constructing carbon fibre composites.
24th March 2025
Adrian Wilson
|
Gloucester, United Kingdom
A patented process developed by Gloucester-based iCOMAT which makes the defect-free steering of composite fibre tapes along curved paths possible for the first time proved critical to the SOCA project led by Jaguar Land Rover (JLR) in the UK.
The SOCA (Sustainably Optimised Composite Automotive) project claimed the Innovation Award in the Automotive Parts category at the recent JEC World composites exhibition in Paris (March 4-6).
The focus of the project, which ran from September 2023 to September 2024, was on developing carbon composite body-in-white vehicle parts to compete with aluminium in terms of CO2 footprint, performance, weight and cost and also involved UK composite builders CCP Grandsen of Belfast and Far-UK in Nottingham.
The project’s members have explained that the current key technologies for constructing carbon fibre composites (CFRPs) such as automated fibre placement (AFP), automated tape laying (ATL) and tailored fibre placement (TFP) are limited in terms of fibre orientation distribution and are only able to handle straight continuous fibre paths, as well as being expensive and comparatively slow.
As a result, they can be labour intensive and involve prolonged manufacturing processes with low-productivity, increased energy consumption, production costs and environmental footprint, hindering their wide adoption in automotive.
While delivering lightweight solutions in comparison to metal components, CFRPs also have a higher embedded CO2e compared to their metallic counterparts, primarily due to the energy intensive processes use in the production of the carbon fibre.
Project Tucana
The SOCA project has aimed to bring to market CO2e-optimised and lightweight composite technologies and body-structures for electric vehicles (EVs) using the award-winning skeleton/flesh concept, which was successfully demonstrated during the previous Project Tucana, the winner of a JEC Innovation Award in 2022.
Project Tucana resulted in the rear body structure of the Jaguar I-PACE being redesigned to increase vehicle stiffness by 30% and cut its weight by 35kg.
The skeleton/flesh concept includes the use of low-cost/low-performance “flesh’“ material strategically reinforced with structural unidirectional (UD) carbon fibre tapes acting as a “skeleton” for the manufacturing of fibre reinforced parts.
This is possible through iCOMAT’s Rapid Tow Shearing (RTS) technology, an automated composite manufacturing process that can place wide composite tapes along curved paths without generating defects. Effective fibre steering is said to allow the alignment of fibres in tapes with the primary load-paths and complex geometries required in automotive applications, leading to ultra-lightweight cost-effective components.
Business intelligence for the fibre, textiles and apparel industries: technologies, innovations, markets, investments, trade policy, sourcing, strategy...
Find out more