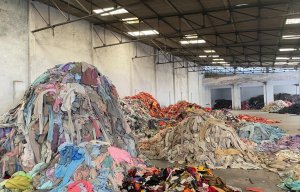
Gathering together the data on textile waste
Over the past decade there has been a marked increase in the development of nonwoven technologies for the successful processing of alternative raw materials, including natural fibres, and for the recycling of waste materials.
7th February 2012
Innovation in Textiles
|
Over the past decade there has been a marked increase in the development of nonwoven technologies for the successful processing of alternative raw materials, including natural fibres, and for the recycling of waste materials.
French machinery builder Laroche, for example, reports that the European market for ‘green’ construction materials is growing rapidly and products made from flax, hemp, jute, wood fibres and kenaf are becoming increasingly popular.
After Canada, France is the largest producer of hemp straw with about 8,000 hectares, producing 50,000 tons of straw which are turned into 10,000 tons of fibres, 35,000 tons of shives and five tons of dust by de-cortication, refining and cleaning processes.
Shives have very good thermal properties and a capacity to absorb and release humidity, so are used in construction materials such as thermal and acoustic ceiling roofing and inside wall insulation in blends with lime clay, as well as in concrete for walls and floors
Hemp fibres are strong and resilient and naturally repel moths and rodents as well as inhibiting the growth of bacteria. They also have good humidity regulation properties and are skin-friendly and easier to handle than mineral or glass wool materials.
As such, they are now employed, amongst other applications, in thermal and acoustic insulation products in roll or panel form for internal walls and roofing
The hemp dust from production can even be used as a heating source, ensuring 100% of the hemp straw is used.
Flax, Laroche points out, is available in much larger quantities than hemp in France and with the company’s decortication and refining technology a significant amount of the plant – primarily the shives, which would otherwise be discarded - can be turned into fibres for nonwoven products for the building industry. They are subsequently airlaid into insulating products with low thermal conductivity and good humidity-regulating properties.
The farming cooperative, Cavac, which has 5,000 members in the Vendée and Deux Sèvres region of western France, now produces various technical thermobonded nonwovens of hemp and flax for the building industry using Laroche equipment.
Cavac farms over 120,000 hectares of land of which an average of 1,000 hectares of oil seed flax is grown, generating about 2,000 tons of flax straw which was previously just waste.
Over in Denmark, Dan-Web has been expanding the range of raw materials which can be processed on its airlaid technology and this now includes:
The company believes there is the potential for airlaid nonwovens to substantially expand into new markets as a result of this wide range of materials
A cluster of Italian machine builders who are regular exhibitors at INDEX shows, including Cormatex, Dell’Orco and Villani, Bombi Meccanica and Bematic, also specialise in such technologies.
The airlay unit of Cormatex, for example, is capable of handling flax, jute, sugarcane, coconut fibre, regenerated cotton, foam polyurethane, glass fibre etc., in a very broad weight range of around 150 grams up to 3,000gsm.
Applications for the products made on this machine include automotive preformed panels, seat wadding, soundproofing and thermal insulation materials, furnishing products such as sofa, mattress and chair waddings, bed quiltings and sleeping bags, roof and wall insulation materials, packaging, interlinings and sanitary articles.
Meanwhile, the world’s largest manufacturer of nonwovens, Freudenberg, reports that it now recycles more than 377 million plastic drink bottles each year – enough to circle the world two-and-a-half times if laid end-to-end.
In North America, recyclable product innovations for everything from mattresses, wallpaper and brooms to building materials, landscaping and automotive interiors have led to new contracts, increased business and job creation for Freudenberg’s Nonwovens, Vitech, Texbond, Filtration and Household Product companies.
Freudenberg Nonwovens, headquartered in Durham, North Carolina, uses millions of pounds of 100% post consumer and post industrial recycled plastic a year to make environmentally sustainable materials for building and construction substrates, landscaping and weedblock materials, residential and commercial wallpaper, carpet backings, filtration devices, and automotive floor mats and carpeting.
The company has recently resumed operation of its recycled polyester fibre line, hired approximately 30 employees over the past year and seen commercial demand increase for its Lutradur and Lutradur ECO recycled plastic products.
Freudenberg Vitech, is an industry leader in the production of nonwoven automotive fabric made from 100% post consumer recycled material at Hopkinsville in Kentucky. Key products include headliners, sun visors, seat backs and packaging trays.
Vitech has landed important new industry contracts and increased its work force by 30% during the past year, as a consequence.
Freudenberg Household Products, headquartered in an environmentally-certified building in Aurora, Illinois, manufactures household and institutional cleaning products, including recycled broom fibers. Earlier this year, the company established a joint venture with SP Berner Plastics to consolidate production of recycled mop and broom components such as handles and bristles. FHP-Berner is hiring more than 50 employees to run the new operations, which were previously conducted in other global production locations.
Freudenberg Texbond, based in Macon, Georgia, recycles more than a million plastic drink bottles a day in production of its nonwoven roofing membrane and building materials. Its products address soundproofing, waterproofing and thermal insulation challenges for the construction industry while helping customers meet green purchasing initiatives. Texbond processes the plastic from bottles into polyester fibres, which are further processed into fabric.
Freudenberg Filtration Technologies uses 100% post consumer recycled plastic to create the material used in its high-quality commercial and industrial Viledon air and liquid filtration systems.
These are just some of the many different ways in which Freudenberg North America is implementing environmental processes for its products to meet the increasingly stringent ‘green’ requirements of its customers, whilst increasing employment.
This article originally appeared in the INDEX14 Newsletter and has been republished with the kind permission of EDANA.
Business intelligence for the fibre, textiles and apparel industries: technologies, innovations, markets, investments, trade policy, sourcing, strategy...
Find out more