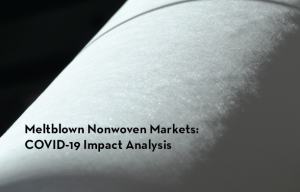
New INDA report provides outlook for medical facemask/respirator meltblown demand
Queensland based company OZ Health Plus is to establish Australia’s first manufacturing plant that will make the critical material used in most protective face masks
7th July 2020
Innovation in Textiles
|
Brisbane, Australia
Queensland based company OZ Health Plus is to establish Australia’s first manufacturing plant that will make the critical material used in most protective face masks. The company has purchased plant from the Switzerland based technology company Oerlikon, to establish a production plant for spunbond and meltblown nonwovens.
The fabrics are essential for Australia’s face mask manufacturers, who currently produce about 500 million medical and industrial masks per year. However, the fabrics have to be imported from overseas and access to these materials has been severely disrupted during the COVID-19 pandemic.
Oerlikon’s German-based business unit Oerlikon Nonwoven has now ‘executed legal and commercial arrangements’ to supply the specialised machinery which can manufacture the nonwoven material locally. The same machinery is used to make almost all face masks material manufactured in Europe and the meltblown plant will commence operations in April next year, with a second stage planned for late 2021.
The Oerlikon Nonwoven plant can produce meltblown fabrics for 500 million masks per year, along with other medical and non-medical grade products, filtration products, sanitary items, antiseptic wipes and more. Rainer Straub, Head of Oerlikon Nonwoven, commented: “We are very proud that we can now for the first time supply our Oerlikon Nonwoven meltblown technology to Australia. Due to the short delivery time, we hope to make our contribution to the Australian population and their safe supply of high-quality protective masks as soon as possible.”
OZ Health Plus director Darren Fooks, said: “Australia has access to raw polypropylene feedstock but lacks the plant to convert that raw material to specialised spunbond and meltblown fabrics. These fabrics are essential for local mask manufacturing. The Australian-based Oerlikon Nonwoven plant will fill the production chain gap for Australia by producing the fabrics we need for mask production and many other products – it will reduce Australia’s protective mask supply chain from thousands of kilometres, to tens of kilometres.”
“Our decision in favour of Oerlikon Nonwoven was a given once we had analysed the material samples. It was a matter of course for us that the Business Unit of the Oerlikon Manmade Fibers segment could supply high-quality machines and systems,” added Darren Fooks.
OZ Health Plus’ new facilities will take up 15,000 square metres of manufacturing space and employ 100 full-time people once the second stage of the project is complete. OZ Health Plus continues to work with both Queensland and Federal Government stakeholders and values their support in bringing this vital capability to Queensland.
“Oerlikon Nonwoven meltblown technology, which can also be used to produce nonwovens for protective masks, is recognized in the market as the technically most efficient method of producing high-separation filter media from plastic fibres. Most of the protective mask capacities available in Europe to date are produced on Oerlikon Nonwoven equipment,” Oerlikon Nonwoven concluded.
Business intelligence for the fibre, textiles and apparel industries: technologies, innovations, markets, investments, trade policy, sourcing, strategy...
Find out more