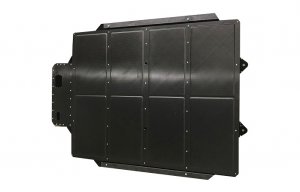
SGL and NIO produce prototypes for battery enclosures
SGL Carbon is making a $4.5 million investment in a new line for carbon fibre-based composites at its plant in Arkadelphia, Arkansas.
26th January 2021
Innovation in Textiles
|
Arkadelphia, AR, USA
SGL is investing in a new line for carbon fibre-based composites, following the award of a substantial contract for composite battery enclosures from a North American car manufacturer at the beginning of 2020.
The new investment at the Arkadelphia plant is expected to be fully operational by the end of 2021. And has received funding from the Arkansas Economic Development Commission (AEDC), the City of Arkadelphia and Clark County.
“Composite battery enclosures meet the specific needs of the chassis for modern e-cars and our facility also produces a variety of carbon and glass fibre-reinforced products for a wide range of industrial applications within the automotive and aerospace industries as well as the energy sector,” said Steve Swanson, vice-president of operations at SGL Composites Inc.
SGL has also started the production of the carbon fibre profiles for BMW windshields after receiving a multi-year order from Koller Kunststofftechnik of Lupberg, Germany.
The profiles are particularly flexible fibre tows, pre-impregnated with thermoplastic resin in various dimensions. They will be compiled by SGL Carbon on the basis of its own 50k carbon fibre at its site in Innkreis, Austria, and subsequently injection moulded at Koller to form a skeletal plastic component. The composite component replaces the previous steel-based windshield.
The windshield is a crucial stabilising element and the profiles add the required stiffness and crash safety. At the same time, they help to significantly reduce the weight of the roof and talso support the driving dynamics. The injection moulding process also enables particularly complex and material-efficient structures. In the BMW model, this component concept will cut weight by 40% compared to conventional steel designs of the component while creating important space for cable ducts and sensors.
The production of the carbon fibre profiles themselves is particularly geared to material and process efficiency in large-scale production. The profiles consist of several smaller fibre strands, the so-called rods, and are manufactured using a modern continuous pultrusion process.
“At SGL Carbon, we have been working on the development of thermoplastic carbon fibre profiles for use in injection molding for some time and this development work is now beginning to pay off,” said Sebastian Grasser, head of automotive at SGL Composites Fibers & Materials. “Due to the many advantages and competitive costs, we see a great potential for the technology to be used in other automotive projects too.”
Business intelligence for the fibre, textiles and apparel industries: technologies, innovations, markets, investments, trade policy, sourcing, strategy...
Find out more