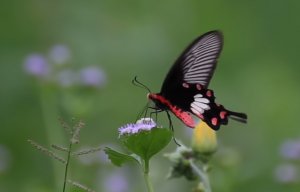
Launch of Design for Decomposition
Opinion
From 1941 when George de Mestral was inspired by nature to design Velcro, engineers have been enthusiastic in their pursuit of what else nature can teach us.
2nd October 2018
Marie O'Mahony
|
Toronto
From the moment in 1941 when the Swiss engineer George de Mestral was inspired by nature to design Velcro, designers and engineers have been enthusiastic in their pursuit of what else nature can teach us. This approach to innovation has become known as biomimicry or biomimetics. There is no shortage of great ideas to look to a nature: Bird feathers used in flight or as thermal insulation; silk made by spiders that is both strong and lightweight or the anti-reflection characteristics of the moth’s eye that has evolved to prevent daylight being reflected by them providing camouflage.
With some notable exceptions, fully commercialised textiles based on biomimicry are relatively few. And those that do exist are not seen to be evolving at the same rate as other innovation paths. How different is the Velcro that you are using today from the one that you use as a young child? This begs the question of whether we need to look at nature in a different way.
I used my own keynote presentation at the recent RISE2018 conference in Raleigh, North Carolina, to explore the subject and to see what new developments we can expect to see from industry and academia.
When a route to innovation results in success, there is a natural tendency to repeat the same approach. There is a strong logic to this, yet some of the most successful biomimicry developments have come about when people challenge accepted views and approaches. Speedo’s sharkskin-inspired Fastskin goes against the accepted idea that a smooth material will always be the most aerodynamic. To the human eye, the skin of the shark does look smooth. However, using advanced visualisation techniques, such as Scanning Electron Micrograph (SEM) imagery, it is possible to see the surface of the skin is in fact comprised of denticles. In this book Ways of Seeing (1972), the British art critic John Berger observes that “the relationship between what we see and what we know is never settled”.
Advanced imaging forms one part of a convergence of technologies that can include such fields as Additive Manufacturing, robotic fabrication and Artificial Intelligence (AI). In a collaboration between Airbus, The Living, Autodesk and APWorks generative design tools are brought together with AI to create an optimized partition for Airbus cabins. Looking to nature to provide a solution for materials that are light in weight yet structurally strong, this combination of technological processes allows for thousands of design options to be explored in a time and cost-effective way before selecting the best solution for each aircraft. The final material can be described as both a nonwoven and composite, with the function of the nonwoven extending beyond that of a prepreg for the composite. This example highlights the importance to innovation of how we look at nature, as well as our perception of manufacturing technologies and their categorisation.
Professor Jeannette Yen is Director of Georgia Institute of Technology’s Centre for Biologically Inspired Design. Applying the principles of biomimicry with industrial collaborators allows her to focus on real world problems investigating material development in topics such as haptic qualities and soft-touch surfaces, attachment devices and anti-friction surfaces. Professor Yen points to the insights that can be taken from nature at different scales. Research on the Euplectella deep sea sponge has inspired some of the mechanical engineering principles used in the building such as the Swiss Re Tower in the city of London. Taken at another scale it can produce in micro nanoscale structure with extremely high resilience and damage tolerance because of its hierarchical optimisation. Hierarchical organisation is something that nature does very well often using layering strategies to achieve different material possibilities to satisfy a variety of functions. Finding sources that include insects, as well as plant cell walls, Yen sees their value is as a starting point but warns against these becoming infinite possibilities.
The environmental impact of materials and product is a key driver in the surge of interest in biomimicry. As Professor Yen puts it, “in order to survive, organisms use strategies honed over an evolutionary time to optimise the use of materials and energy”. Nature’s solutions can often appear beguilingly simple and what does not work quite simply does not survive. Landfill and ocean pollution are testament to the fact that manufactured material design has not followed these principles.
Gurminder Minhas, of BioFilaments, is one of a growing number of companies looking to address the environmental impact of materials utiliыing some of the principles of biomimicry. BioFilaments are developing a nano fibrillated cellulose from certified managed forest feedstock to produce nano fibrils using a nonchemical mechanical refining process. Bringing the material to the next stage, the company is looking to create an NFC-enhanced glass fibre nonwoven using a wetlaid process. This is achieved by entangling the fibrils around the glass fibres at certain points to create a bridging that strengthens the nonwoven structure and also allows for customised pore size in the material. The bridging process creates higher strength as well as improved filtration efficiency.
The pinecone has the ability to open and close in response to changes in external temperature, opening as temperature rises and closing as it drops. It is a good example of how the same principles found in nature can be applied in very different ways by material innovators. The Swiss company Schoeller took the pinecone as inspiration for their c_change membrane technology, where the polymer structure opens to allow excess heat and moisture to escape from the body to the outside air but remaining closed when the wearer is not active and so conserving heat. Waterproof and windproof, it is designed for use in all weather conditions.
MMT Textiles, with inventor Dr Veronica Kaspali, have taken a very different approach in the development of Inotek fibre. Highly engineered fibre structures first emerged from Japan in the late 1990s. Hollow and modified fibre cross sections are used to provide a range of functionality from climate control to wicking. Jeffrey S. Dugan, VP Research Fibre Innovation Technology at MMT Textiles, has been developing a bicomponent cross-section fibre that is self-crimping. The chief technical challenge that he has faced is in the design of the core structure and its outer sheath. The Inotek fibre has a polypropylene core and nylon sheath, exploiting the differences in swelling caused by moisture regain. Looking to optimise the cross-section but avoiding tear points that might be caused by sharp corners a D-liptical shaped core provided the solution. D-liptical being a slightly rounded D shape. The company are testing the fibre in different fabric structures, including nonwovens.
The combination of new technologies, new partnerships and the search for sustainable materials is driving the next phase in biomimicry inspired textiles. Collaboration, often across continents, takes time as does bringing a new fibre or textile development to scaled production. The real challenge may not in fact be our ability to effectively seek inspiration from nature, but in the way that we manage our research, development and stakeholder relationships.
Business intelligence for the fibre, textiles and apparel industries: technologies, innovations, markets, investments, trade policy, sourcing, strategy...
Find out more