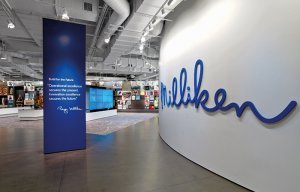
Continuous recognition for Milliken
Opinion
Comprehensive strategies in place for increasing recycling and the use of bio-based feedstocks.
20th December 2024
Adrian Wilson
|
Online
Experts from two giants in the textiles and nonwovens supply chains provide their perspectives on the path to net zero manufacturing in the latest webinar from ITMAconnect that is now available to view online.
In a discussion chaired by Behnam Pourdeyhimi, executive director of the Nonwovens Institute in North Carolina, Claire Mattelet, Indorama’s sustainable programs director for fibres and Jeff Strahan, Milliken’s director of research, compliance and sustainability, discuss in detail the comprehensive strategies their companies are putting in place in moving to a more sustainable future.
PET polyester leader
With sales of $16.6 billion in 2023 and 26,000 employees at more that 140 sites worldwide, Indorama is the world’s largest fully-integrated producer and recycler of PET polyester and also a major supplier of polypropylene (PP) and polyethylene (PE) to nonwovens manufacturers.
Between 2011 and 2023 it has recycled more than 21 billion PET bottles and in looking to reduce its greenhouse gas emissions by a further 30% by 2030, is investing $9 billion in advanced recycling and biobased technologies.
By 2030, the company aims to be recycling 100 billion PET bottles annually and has also set targets to increase its use of biobased feedstocks from 1% to 16% and its use of circular feedstocks from 5% to 30% that will apply to 20% of its annual production, or 4 million tons of product each year.
“Our strategy is focused on optimising our global model and leveraging existing assets and we are investing in key new technologies that are ready to scale,” Mattelet says.
These include the enzymatic PET recycling plant that Carbios is building in France and the first cross-industry supply chain for carbon capture PET that is being established with other major corporations. Indorama is also developing Biotransformation technology with Polymateria – a patented technology that alters the properties of polyolefin feedstocks to make them biodegradable in a natural process.
Mattelet observes that automotive customers are currently leading the field in the adoption of such technologies, pushed by stricter regulations than the general textile and nonwovens industries.
“Circularity will initially come at a premium but the large-scale adoption that will hopefully follow will drive down costs,” she says. “Financial and regulatory support is crucial in making the recycling industry more competitive and we believe there should be a mandatory percentage of recycled content in all new products put on the market going forward, and rising over the years on our way to net zero.”
SBTs and carbon tax
Milliken & Company, headquartered in Spartanburg, South Carolina, is active across a range of sectors including speciality chemicals, floor coverings, performance and protective textile materials and healthcare and has been granted more than 5,500 patents worldwide. Around 8,000 people are employed at its 70 operations worldwide.
In the ITMAconnect webinar, Jeff Strahan emphasises the importance of the UN’s Science-Based Targets (SBTs) relating to Scope 1, 2 and 3 emissions which are already being adhered to by 39% of the world’s corporations – equating to almost $50 trillion of global annual business.
“The SBT’s now call for a commitment to reaching net zero by 2050, which is significant,” he says. “Milliken is currently on target to reduce our Scope 1 and 2 direct emissions by 50%, and our scope 3 indirect emissions by 30% in 2030. We buy some raw materials from Indorama, for example, so its Scope 1 and 2 emissions are part of our scope 3 emissions.”
Strahan emphasises the importance of energy as a lever for positive change, with 24% of greenhouse gas emissions already subject to carbon tax.
“This is a staggering number already accounted for, so carbon is going to cost money and it’s important to explore options for its reduction now, in order to reduce future bills,” he observes.
Measures already implemented at Milliken include a €25 million investment in a co-generation energy plant cutting energy usage by 20% at one of its major integrated US sites.
OEM opportunities
Milliken is also a major supplier to the automotive industry, with more than 50% of North American cars including at least one of its nonwoven components. It has developed a system for recycling the waste material of one Tier 1 automotive customer that has already diverted 1.8 million pounds of waste from landfill or incineration since 2021 and is now exploring routes for also recycling the waste from OEM manufacturers.
Accommodating recycled fibres in Milliken’s own materials is also yielding impressive savings, since 1kg of virgin PET chip equates to around 3.4 kg of CO2 emissions. The substitution with recycled PET can yield a reduction of around 80% of CO2 emissions as well as a 60% reduction in the use of chemicals.
Milliken is also investing in partnerships, including with polypropylene recycler PureCycle, as well as with Circ, which is commercialising a process for recycling blended fabrics.
“PET, PP and PE remain the major plastics in use in the world and if we can develop circular systems for recycling them at scale, we’ll have won,” Strahan concludes. “The world went for plastics for good reason and their usage is not negative. It’s just the waste we have to successfully handle now.”
The ITMAconnect webinar can be viewed here.
Business intelligence for the fibre, textiles and apparel industries: technologies, innovations, markets, investments, trade policy, sourcing, strategy...
Find out more