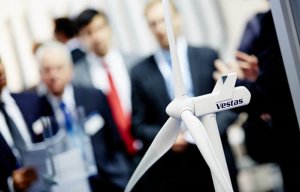
Wind power focus at Composites Europe 2017
Opinion
As I’ve mentioned previously in this column, carbon fibre has some pretty glamorous associations, what with being able to latch onto the Boeing and Airbus superplanes and hundreds of next-generation military and space programmes, in addition to Formula 1 and high profile programmes such as BMW’s latest i-series electric cars.
20th March 2014
Adrian Wilson
|
Paris
As I’ve mentioned previously in this column, carbon fibre has some pretty glamorous associations, what with being able to latch onto the Boeing and Airbus superplanes and hundreds of next-generation military and space programmes, in addition to Formula 1 and high profile programmes such as BMW’s latest i-series electric cars (see Buy Carbon, Sell Glass).
For the manufacturers of glass fibres, yarns and fabrics, meanwhile, it’s simply business as usual.
But it’s all pretty smart business just the same – as was very evident at the 2014 JEC Composites show which took place in Paris from March 11-13.
Take AGY, for example, headquartered in Aiken, South Carolina, which is currently achieving considerable success with its S-2 glass fibre composite reinforcements for the oil and gas industry.
Specifically, its products are making a significant contribution to the success of fracking that’s currently poised to make the USA self-sufficient in energy within a decade.
AGY’s high-performance reinforcement offers the physical and chemical characteristics necessary to drive composite down-hole tooling into more aggressive well environments.
As well depths increase, so do down-hole temperatures and pressures, creating progressively more hostile environments for the materials involved. Composites produced using S-2 Glass can be more than 40% stronger than those made with traditional E-Glass fibre and can provide up to 200°C additional thermal resistance without compromising the performance of the drill. Improved mechanical properties allow the use of composite frac plugs and other tooling in well sites that have previously been restricted to metal tools. In addition, plug and tool use life in all well types can be increased significantly. S-2 Glass also provides salt-water corrosion resistance – a known failure issue with composites made from E-Glass reinforcements.
Any composite is only as good as the linkage that holds its parts together and AGY has developed a portfolio of sizing systems for both thermoset and high-temperature thermoplastic polymers to ensure that S-2 Glass can meet requirements in as wide a range of resin systems as possible.
“Tailoring the linkage between the glass surface and the polymer matrix to achieve optimum chemical bonding can be the difference between the system – and the part – holding or breaking,” explains Drew Walker, AGY’s CEO. “Some fibre manufacturers try to take an easier route by having a one-size system that is okay for several polymer systems. However, what’s okay for many things is rarely excellent for anything. In today’s demanding oil and gas industry, only excellent will do.”
AGY has also just announced a partnership with CTG/Taishan Fiberglass, which will produce S-1 HM glass, developed primarily for the wind energy market in China.
Johns Manville introduced a new range of Evalith hybrid nonwovens for decorative thermoplastic applications consisting of mixed glass and polyester fibres at JEC 2014. The Evalith material has excellent thermo-formability and also enhances mechanical performance, making it well suited as a skin material for reinforced thermoplastics.
The roofing panel of the BMW i3 which is made from the company’s products was on display and a new chopped strand glass fibre was also introduced, for use with high performance polypropylene in composites designed specifically for automotive applications, such as inlet manifolds and front-end carriers, to reduce the weight of structural parts.
JM’s new ThermoFlow 636 provides improved mechanical properties in tensile strength and impact resistance by 10% compared to standard short glass fibre chopped strands. Available in 10 and 13 micron fibre diameter, its maintains the exceptional high flow feeding performance of current ThermoFlow chopped strands with low fuzz and less downtime to the benefit of customers using large extruders –even with high glass load.
JM also announced plans to rebuild and upgrade the EU’s largest and most productive E-glass furnace located at its Trnava site in Slovakia.
As reported elsewhere on Innovation in Technical Textiles, Owens Corning introduced a number of new products for the wind power industry in Paris, while 3B and its partners – DSM, Siemens Wind Power and DTU Wind Energy – received the 2014 JEC Innovation Award in the Sustainability category.
Their achievement is a new composite system for the easy manufacturing of wind turbine blades which are characterised by low weight, high stiffness and excellent resistance to fatigue.
The material system is currently being evaluated by Siemens Wind Power for its next generation wind turbine blades and is based on DSM’s Beyone 201-A-01, a resin that is styrene-free, cobalt-free and 40 % bio based.
The use of this resin brings faster resin infusion and requires only limited post-cure. The system also incorporates 3B’s SE3030 glass rovings.
Through an optimised sizing applied on the glass filaments, an excellent fibre/resin interaction is obtained, resulting in improved composite properties for a long-lasting blade operation.
“For Siemens the new composite system provides many benefits, including a major reduction in blade manufacturing cost and an increased process output,” says Karsten Schibsbye, manager of the Siemens Next Generation Blade Project.
Owens Corning also supplies special triaxial glass fabrics for the manufacture of wind turbine blades under the Ultrablade brand, which are supporting the industry’s push for ever-longer blades.
The latest 7 MW wind turbine which has just been installed at a new site off the coast of Scotland features blades made by SSP Technology of Denmark, each of which is a staggering 83.5 metres long and weighs some 30 tons.
The turbine can produce the equivalent the annual energy consumption of an average family house in just 30 minutes.
With these kind of new applications cropping up – and with glass still accounting for around 80% of all the fibre reinforcements used in composites – the glass fibre makers can happily afford to let their carbon cousins have all the limelight.
Business intelligence for the fibre, textiles and apparel industries: technologies, innovations, markets, investments, trade policy, sourcing, strategy...
Find out more