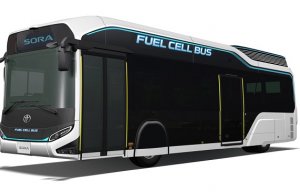
Toho Tenax develops multi-material roof cover for Toyota
Opinion
Around 40,000 tons of warp knitted fabrics are now produced annually for large scale advertising billboards and hoardings. Read more about the findings that were presented by VDMA Textile Machinery Association at the recent ITMA ASIA + CITME exhibition...
5th August 2014
Adrian Wilson
|
Shanghai
Around 400,000 tons of warp-knitted fabric is now produced annually for large-scale advertising billboards and hoardings, according to the VDMA Textile Machinery Association.
This growing technical textiles sector was one of three selected by the organisation for case studies which illustrate the progress that has been made by German machine builders in efficiency and energy savings over the past decade.
The findings were presented at the 2014 ITMA Asia exhibition in Shanghai as part of the VDMA’s ongoing Blue Competence initiative, and some concrete comparisons were made to underline the benefits to Chinese textile manufacturers.
The warp knitted fabric made each year for advertising billboards, for example, equates to around 3,442 square kilometres – sufficient to cover the entire metropolis of Guanghzhou.
One particularly huge example at Dubai airport covers 20,000 square metres alone – large enough to cover three football fields.
Compared to a decade ago, today’s German production machines can achieve energy savings of 26% in the production of these fabrics – the equivalent to 300 billion watt hours (300GWh). This is equal to the daily output of the world’s biggest hydroelectric power station, the Three Gorges Dam on the Yangtze River.
Textile billboards have to be resistant to extremes of weather and also suitable for carrying quality prints, while being either transparent or light-proof, depending on requirements.
Such materials can be cost-effectively produced using warp knitting technology in widths of up to 6.7 metres, without any further making-up required.
Polyester yarn with a count of dtex 550 f 96 PES was used for the VDMA study. As a rule, these yarns are employed as both warp and weft and warped on sectional beams of 21 inches outside diameter.
A warp knitting machine of 213 inches working width and a machine gauge of E18 was taken as the basis. The warp and weft yarn systems are interlaced with a 76 dtex PES yarn to produce fabrics of 120gsm.
The coating and laminating of these materials varies significantly from region to region, the VDMA says, so for the study only the stages up to the warp knitting were taken into account.
The key improvements in terms of energy savings have been achieved in the spinning and warp knitting processes.
The polyester filaments are now produced on a 16-thread system, as opposed to the previous eight-threads, which has led to increased output, while at the same time lowering consumption. Round spinning beams save more than 40% of the previous energy consumed, and high frequency induction technology at the godets saves 20% compared to conventional systems.
A 29% energy reduction has meanwhile been achieved in the warp knitting process for these fabrics over the past ten years. This is down to a combination of improvements, including improved gear technology, reduced friction and the reduction of moved mass. In addition, the machines have an average lower error rate of just three faults per 1,000 metres produced.
Two further VDMA studies examine the savings that can be made when manufacturing standard cotton in the T-shirts and functional performance T-shirts for running.
The energy required to manufacture standard cotton T-shirts has been reduced by 28% and the water consumption by 33% over the past decade.
Based on the production of just one T-shirt per person on the planet, this equates to around 1,000 megawatts – the equivalent, the organisation points out, to the annual output of Beijing’s Gaojing and Guohua coal power plants.
Applied to the production 1,000 T-shirts, around 2,725 kWh can be saved as a result of advances in German yarn production, circular knitting, washing, bleaching, dyeing and finishing.
Functional performance T-shirts for running are generally made from breathable and quick-drying fabrics, designed to provide thermal insulation, skin-friendliness and the optimum perspiration absorption.
Each year around 125 million such T-shirts are produced and if all were manufactured using the latest German textile machinery, the VDMA says, 23.5 billion watt hours (23.5 GWh) of energy would be saved – sufficient to power 200 million notebooks during a working day.
Business intelligence for the fibre, textiles and apparel industries: technologies, innovations, markets, investments, trade policy, sourcing, strategy...
Find out more