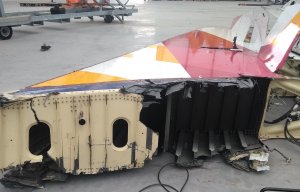
ELG in end-of-life aircraft carbon initiative
Opinion
A new, fast and inexpensive process for the 100% recycling of carbon-fibre composites has been developed at the University of Colorado.
22nd February 2016
Adrian Wilson
|
UK
A new, fast and inexpensive process for the 100% recycling of carbon-fibre composites has been developed at the University of Colorado, along with a method for turning the recycled resins and fabrics into a new material that is just as effective as the original product – but cheaper to produce.
This has major implications for a rapidly-accelerating industry. The use of carbon-fibre composites in Airbus and Boeing passenger planes has increased from 10% to 50% in the past ten years, and now the same is poised to happen in commercial cars. This will potentially create a major issue when it comes to recycling in the future.
Lower-performing nonwovens for various automotive and aerospace applications have so far been the only products to be made from recycled carbon fibres.
Now, Wei Zhang, CU-Boulder associate professor of chemistry and biochemistry and his team have developed a method for reclaiming all of the carbon fibre and the resin simply by soaking the composite in an organic solution at room temperature.
“The resin that holds the composite together can be chemically broken down and separated from the fibres, enabling both to be re-used to make more composite materials of the same strength,” says Philip Taynton, who along with Zhang and CU-Boulder alumnus Chris Kaffer have also founded a start-up company working to bring the process and new composites to market. “Other than mild stirring, no extra energy is used in the recycling process and no waste is created by the recycling process. It is a closed-loop energy efficient cradle-to-cradle recycling solution.”
Currently it’s common for as much as 50% of composite materials to be discarded as scrap during the manufacturing process
“This means that manufacturers could see a financial benefit to recycling on the front end, in addition to the retention of material value at the end of a product’s service life,” says Taynton.
Currently, recycling finished composites requires breaking them down with expensive, energy-intensive processes to separate the resin from the fibres, or the composites can also be crushed into a fine powder. Neither is ideal.
The new composite material based on the recycled components developed at University of Colorado is said to be just as strong and can be more quickly fabricated than most carbon-fibre composites, being formed in 60 seconds.
“The exchangeable nature of the chemical bonds which enables the facile recyclability also leads to additional benefits for manufacturers,” Taynton says. “Single plies or sheets of our malleable composite material can be chemically welded together through simple compression moulding. This leads to 60-second cycle times for the manufacture of parts, which is a target which was set by the automotive industry for rapid manufacturing of composite materials.”
The new start-up, called Mallinda, is now working with a number of branded sporting goods companies to scale up its manufacturing process over the next 12 months.
Business intelligence for the fibre, textiles and apparel industries: technologies, innovations, markets, investments, trade policy, sourcing, strategy...
Find out more