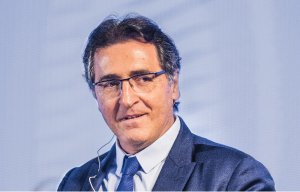
ITMA Live: Forging Ahead Amidst A Pandemic - Alex Zucchi, Managing Director/ Shareholder at Ferraro SpA
Package includes a full range of machinery for the complete treatment of knitted fabrics.
17th May 2023
Innovation in Textiles
|
Germany
Goller, a member of the CHTC Fong’s Group, will promote its KnitExcellence package at ITMA 2023 in Milan from June 8-14, at stand B106 in Hall 18.
The KnitExcellence package includes a full range of machinery for the complete treatment of knitted fabrics – Knit Complexa for bleaching, Knit Mercer for mercerisation, Knit Economica for dyeing and the versatile Sintensa washing concepts for washing after dyeing and printing.
The multi-purpose rollerbed steamers of the Knit Complexa can be used for steaming after bleaching but also washing, when required. The rollerbed in the steamer transports the material while slightly shifting the material from roll to roll to avoid yellowing on the fabric surface. A sump heating equalises the steam condition in the entire compartment and guarantees a homogeneous humidity.
The Knit Mercer unit provides very low tension during caustic treatment and a homogeneous mercerizing effect. Short distances, load cells and drive control provide continuously smooth transport of the material through the machine.
The Knit Economica S Roll padder secures the same pressure over the width of the squeezing rollers and assures an equal dyeing of the fabric The combination of dwelling and drum wash concepts with cyclone rotors realises the best use of washing times and mechanical treatment to minimise water and chemical consumption.
The Goller Sintensa is a continuous washing machine used for washing off knitted textiles after reactive dyeing and printing as well as polyamide after acid printing, wash off disperse print and every kind of spin oil washing. The machine uses a combination of mechanical action, water and detergent to remove any residual dye or chemicals from the fabric. It can handle large volumes of fabric, making it ideal for use in industrial settings instead of discontinuous treatments.
The machine is designed to minimise water and energy consumption, which can help to reduce operating costs.
Overall, the Goller Knit Excellence concept is a reliable and efficient package that is well-suited to all wet finishing treatments of knitted textiles. Its robust and high quality design and advanced features make it a popular choice for textile manufacturers around the world.
Oxidator for wovens
Goller will also introduce the new Oxidator module for woven fabrics at ITMA 2023.
The interchangeable modular design of this new washing compartment enables it to be interchanged to meet the demands of differing fabric qualities and washing requirements, extending the life of the machine. It combines powerful spray washing and up-down roller washing to achieve an excellent cleaning effect, while accommodating 25% more fabric content than a conventional drum washer.
The Oxidator enables multi-power spraying at adjustable angles with high circulation of the water for excellent washing efficiency, automatic cleaning of the squeezer and filter and automatic tension control. It is suitable for all kinds of woven fabric.
Goller continuous dyeing and wet finishing units are manufactured at the plants of Fong’s in Germany and China. The design and development centre in Germany designs tailor-made solutions for customers based on a modular combination of different compartments depending on the process, fabric and production speed.
The company has been producing machines for over a century and can draw on comprehensive knowledge in the field of the continuous treatment of textile materials when designing bespoke customer solutions.
In addition to innovative ideas in the development of machines, design based on experience, experimental field tests and the detailed development of the different modules, Goller’s engineers can help to reduce energy and water during production on continuous wet finishing plants.
Business intelligence for the fibre, textiles and apparel industries: technologies, innovations, markets, investments, trade policy, sourcing, strategy...
Find out more