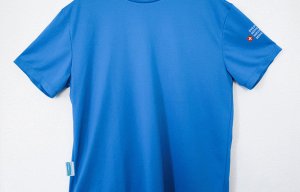
OceanSafe claims Design Prize Switzerland
OceanSafe has an exciting new business model which could have industry-wide implications. Innovation in Textiles talks to the company’s chief marketing officer Matthias Fuchs.
8th February 2023
Innovation in Textiles
|
Frankfurt, Germany
At the first textile show of 2023, Heimtextil held in Frankfurt, Germany, from January 9-12, there was tremendous interest in the Swiss start-up company OceanSafe.
It has developed a new synthetic polymer that is already being turned into fibres, filaments and yarns with all the favourable processing and performance properties of polyester, while at the same time being circular, biodegradable, and toxin-free.
OceanSafe’s naNea materials are also the first and only synthetic textile materials which have achieved the extremely stringent Cradle to Cradle (C2C) Certified Gold standard and certification for the biological cycle to date – for the entire product supply chains of various manufacturing partners.
Innovation in Textiles: OceanSafe was founded in 2019 – can you tell us about the background of the company?
Matthias Fuchs: Our company was founded by Manuel Schweizer, today our CEO, who has been in textiles for over 30 years and has played a fundamental part in recent innovations from the Swiss textile industry. He was the first to establish a Cradle-to-Cradle interior fabrics line worldwide almost ten years ago, so was one of the pioneers, having been involved from very early on in the implementation of the C2C standards for certification into new products.
By 2019 Manuel had become aware that circularity was building a lot of traction and saw a business model for C2C textiles in the marketplace, initially distributing contract home textiles Europe-wide.
The intent was to develop fabrics which are safe for the oceans – hence the name OceanSafe – by working with companies who have the power to bring these materials into the home textiles residential and contract market for interior designers, specifiers and retailers.
IIT: Who was your first customer?
MF: It was JAB Anstoetz – a German market leader in premium and high-end interior fabrics with a global footprint. JAB was our pilot partner and really believed in what we were doing. JAB was the first to work with us on developing these fabrics, delivering its own input and starting to distribute the first collection based on OceanSafe technology in 2021.
IIT: Your references, on the whole so far, seem to be European brands and manufacturers in home textiles. What is the rationale behind this? Why not sports or outdoor wear, where the interest in innovation seem to be more intensive?
MF: For many years Manuel was in charge of the interior fabrics department at Möbel Pfister which is the leading Swiss furniture chain, so he is by definition a home textiles guy and in love with those product ranges – curtain fabrics, sheers and upholstery fabrics were his passion.
I joined at the end of 2020 and also had a home textiles background but more in bed linen, carpets and terry towels, and from a manufacturing perspective. For a number of years I was in charge of the European organisation for the Welspun Group, including Christie towels.
When Manuel explained his vision to me, it became clear we should not restrict ourselves to home textiles but could bring our technology to other markets including fashion, sportswear and technical textiles, where the volumes are. So we started in the niche field of home textiles but aimed at scaling this up globally. As a result, we have now opened naNea up into a technology licensing model – available for all industries looking to replace conventional polyester.
IIT: What is the rationale behind being a material science company and having your own accreditation scheme?
MF: One of the biggest challenges of our model is making it easy to digest because there is a risk of misconception.
Firstly, our vision for 2030 is to develop fully circular finished products with brands.
We believe that the products this industry needs in order to create impact and also comply with the European Green Deal must be circular, fully recyclable, toxin-free and kept in the biological cycle. Today we can already develop certified garments with our components and made by certified value chains. These garments are being Ocean Safe certified.
Outside Europe, we have already partnered with Yunus Textiles Mills, one of the largest bed linen manufacturers in the world based in Pakistan, for bed linen sets, as a good example.
The second part of our business is the material science, and we believe we have a truly revolutionary and proprietary circular synthetic polymer for fibres and yarns, which we are distributing independently from the holistic Ocean Safe Certified model.
The two go hand in hand since we are not a manufacturer ourselves. The polymer chip we have developed is being produced by a partnering chemical company and we now have the opportunity to partner with others.
We are also seeking close partnerships with brands who understand the potential and who can scale production up together with us.
IIT: You are also developing a synthetic alternative to cotton, which is a bit of a hard sell, given consumer perceptions of synthetics compared to natural fibres. How can you explain its benefits in simple terms?
MF: naNea has always been targeted at the polyester market. However, our ambition is to also provide a synthetic and scalable alternative to another impactful material, namely cotton.
This game-changer will come with coNea – a proprietary material that is completely different chemically but that is as soft and hydrophilic as cotton when spun into fibres by extrusion and melt spinning.
This patented technology is not yet on the market and will be launched in the second half of this year. coNea is 100% biobased from fermented agricultural waste. The material is circular, biodegradable, and toxin-free.
IIT: So, what’s immediately next?
MF: Our products are already being used widely in home textiles and we now have some exceptional projects going on with global brands in the sportswear and fashion, luxury automotive and technical textiles fields.
I think the industry has now understood that fibres from recycled PET bottles are not the solution and many companies want to skip the r-PET story and move directly to circular synthetics, which are suitable for the biological cycle.
Our aim is to replace conventional polyester and cotton with fully circular synthetic alternatives and this is not a pipe dream. After our recently completed funding round, we are now expanding our team to react to the increased demand for our technology.
We have already produced more than 200 metric tons of product so we are already at industrial scale, and we can further scale up the volume very quickly. For manufacturing partners, no new technology is required from polymerisation to spinning and on to weaving and knitting. We can provide drop-in solutions for existing infrastructure which is a huge advantage for our partners. These are very exciting times at OceanSafe for sure.
Business intelligence for the fibre, textiles and apparel industries: technologies, innovations, markets, investments, trade policy, sourcing, strategy...
Find out more