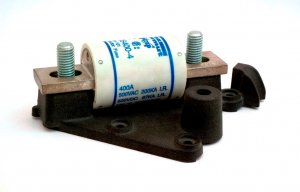
Windform materials pass flammability test
Paving the way for industry to take advantage of the unique qualities composites offer in elements that get very hot.
25th November 2021
Innovation in Textiles
|
Bristol, United Kingdom
The National Composites Centre (NCC), in Bristol, UK, in collaboration with Nexam Chemical, headquartered in Lomma, Sweden, with its manufacturing plant in Cupar, Scotland, has successfully manufactured a composite using a high temperature resin, which provided a solution to the challenge of using advanced materials in components that need to withstand extreme temperatures.
The NCC’s interdisciplinary expertise in the fields of high volume manufacturing, tooling, design, materials science and flow simulation solved the manufacturing challenges existing at elevated temperatures and proved a composite part can be made using Nexam Chemical’s new resin system, Neximid. This development paves the way for industry to take advantage of the unique qualities composites offer in elements that get very hot, such as sections of engines and the housing for electric batteries, which wasn’t previously possible.
Neximid can operate at temperatures up to 400°C – higher than almost all other resin systems. Whilst resin transfer moulding is usually conducted at around 120°C, by developing high temperature specialist equipment – including unique tooling design and high temperature sealings – the NCC was able to keep the resin above 250°C throughout the injection process, allowing the resin’s high temperature capability to be combined with a high processing temperature for a final product that can cope with much higher temperatures than previous composites.
Throughout the process, the NCC has also shown that the resin system is safe, not emitting the high levels of toxic gases that other polyimide resins can.
“Being able manufacture carbon fibre composites using a UK-produced high temperature resin system is a huge step forward in enabling industry to adopt advanced materials in components that were previously unable to take advantage of them,” said Dr David King, advanced research engineer at the NCC. “The excellent thermal capability of the material expands the boundaries of composites into more demanding applications. Based on the emerging details of this expanded capability, we are already working with industry customers on new applications for composite parts, and are excited to further develop our high temperature resin transfer moulding capability by collaborating closely with Nexam and other partners.”
“We are delighted that our five years of collaboration with the NCC has resulted in a major innovation breakthrough for high temperature RTM composites,” added Boyd Cushing, in charge of business development for Nexam Chemical UK & Ireland. “We look forward to welcoming industrial partners who may have interest in our Scottish origin Neximid non-ITAR restricted resin for aerospace and defence applications.”
Following this successful collaboration, Nexam Chemical has joined the NCC as an SME Affiliate Member, paving the way for further projects.
Business intelligence for the fibre, textiles and apparel industries: technologies, innovations, markets, investments, trade policy, sourcing, strategy...
Find out more