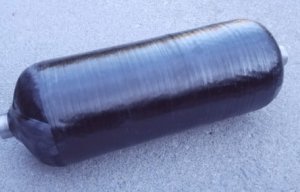
Project to develop smart composite pressure vessels
Multi-functional filament winding technology can handle all combinations of fibre and resin.
23rd January 2024
Innovation in Textiles
|
Bristol, United Kingdom
Cygnet Texkimp has delivered a four-axis filament winding machine to the National Composites Centre (NCC) in Bristol, UK, where it will be part of a new manufacturing and test facility for hydrogen transportation and storage vessels.
The multi-functional filament winding technology provides the NCC and its partners with the capability to wind all types of filament, from towpregs to dry fibre and glass fibre, and all combinations of fibres and resins, including high viscosity and fast cure resins.
“We’re extremely proud to see our filament winding technology forming part of the NCC’s world-leading Hydrogen Programme,” said Cygnet Texkimp CEO Luke Vardy. “The work of the NCC and its partners stands at the forefront of an exciting new era of hydrogen tank design and development and plays an important role in anchoring this area of manufacture in the UK. The technology we’ve delivered offers high levels of flexibility and capability to meet the requirements of many different filament winding applications and support the NCC’s pioneering development work.”
“This technology underpins our state-of-the-art design, test and manufacturing facility for hydrogen and will be used to create pressure vessels for a number of applications, supporting industry in developing business cases and products to enter this growing market,” added Marcus Walls-Bruck, head of hydrogen at the NCC.
The filament winder is designed to wind four tows simultaneously. Each tow has its own tension control unit and dancer arm which regulates feeding and winding tension to enable faster and more accurate winding.
A customised software package developed by Cygnet Texkimp’s in-house team also allows the NCC to record data including winding tension and speed, resin temperature and air pressure within the mandrel.
The filament winder is served by two four-position creels, which are designed to feed different types of fibre into the process. A towpreg creel unwinds and guides towpreg material into the winder and is designed to completely isolate the tension required at the bobbin from the tension desired during the winding phase, in order to ensure the fibre is fed optimally at all times. A second dry fibre creel feeds fibres into the process at low tension and high accuracy and is enclosed to prevent the release of airborne debris into the environment.
The machine also features two types of in-line spreading and coating systems which can be quickly and easily deployed for dry-wind applications – a temperature-controlled wet-out system with adjustable spreader bars to spread individual fibre tows for consistent resin impregnation, and a coating drum and blade to control the volume of resin applied to the fibre. Both of these methodologies will be investigated by the NCC for their suitability in winding applications across a range of applications.
Automation and handling
At the recent Advanced Engineering exhibition held at Birmingham’s NEC, Cygnet Texkimp highlighted how its bespoke automation and handling solutions are being used to improve productivity in the textiles and advanced materials industries.
The company’s technologies are helping manufacturers increase production quality, speed and efficiency, reduce repetitive manual tasks, improve operator wellbeing and safety and enable product traceability in markets including traditional textiles, advanced materials and composites.
“Automation and handling technologies have a vital role to play in maximising efficiency and quality in the materials manufacturing environment,” said Lee Simcock, the company’s director of technology.
These solutions are designed to work alongside Cygnet’s prepreg, coating, slitting, filament winding, creel and materials recycling technologies and include automatic loading and unloading equipment, systems to wrap, pack and palletise bobbins of fibre, radiofrequency identification (RFID), barcoding and vision systems and auto guided vehicle (AGV) systems.
“Just like our fibre converting equipment, each of our automation solutions is designed to enhance the integrity of the fibre or material and the efficiency with which it is processed, either by reducing physical handling or improving traceability and in-process checking,” Simcock said.
Business intelligence for the fibre, textiles and apparel industries: technologies, innovations, markets, investments, trade policy, sourcing, strategy...
Find out more