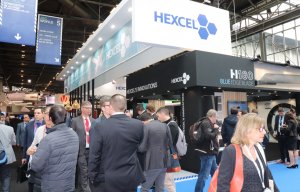
3D printing comes of age
Machines work together to produce high-performance composites in large volumes.
27th April 2022
Innovation in Textiles
|
Zürich, Switzerland
9T Labs, of Zurich, Switzerland, will demonstrate how lightweight carbon parts are pushing cross-sector boundaries at JEC World in Paris, from May 3-5 2022.
The exhibition is timely for the company, following its Series A funding that raised $17 million to help commercialise the Red Series additive fusion solution platform, with key investments made by 3D printing company Stratasys and thermoplastic composites supplier Solvay.
9T’s Build and Fusion modules are operated through Fibrify software that was co-developed with partner and simulation provider, Ansys. The machines work together to produce high-performance composites in large volumes by taking advantage of fast production cycles and the favourable processability of thermoplastic composites. This manufacturing method offers manufacturers the opportunity to directly replace metal parts and conventional manufactured composite parts.
9T Labs will be in Hall 5 at stand Q88 in Paris, running two Build modules and one Fusion module. The team will be available to discuss how additive manufacturing of fibre-reinforced parts is much more accessible than using conventional methods – driving the definition of new standards and certifications to increase industry adoption for end-use parts in marketing including aerospace, medical, sport and luxury.
In addition, the company will display items highlighting its unique ability to employ the most advanced structures, materials, and technologies at scale.
These include:
-An aerospace bracket developed in partnership with Purdue University and Boeing designed to overcome the challenge faced when printing complex load-carrying sub-parts whilst also producing the final part through overmoulding with carbon fibre chips.
-Aerospace struts developed using PEKK with continuous carbon fibre.
-An exoskeleton winglet developed in partnership with the Centre de dévelopement des composites du Québec (CDCQ) and Mawashi, showcasing the ability to print preforms and reshape them into a curved shape during the post-consolidation process.
-A helicopter door hinge developed in partnership with the University of Applied Science and Arts Northwestern Switzerland, designed to allow for printing of sub-parts before welding during the post-consolidation, fusion process.
-An automotive hinge developed in partnership with Setforge – a lightweight additive alternative to metal suspension brackets which can be used on small commercial vehicles.
Business intelligence for the fibre, textiles and apparel industries: technologies, innovations, markets, investments, trade policy, sourcing, strategy...
Find out more