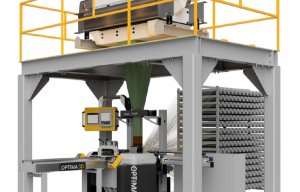
Optima Series 500 3D weaving machines launch at ITMA
Weaving versatility the result of the comprehensive use of digital control systems allowing rapid parameter and sequence changes.
8th August 2023
Innovation in Textiles
|
Maine, USA
Following a highly successful week at ITMA 2023 in Milan in June, the UK’s Optima 3D is delivering the special weaving technology it demonstrated to the USA, for installation at the University of Maine’s Advanced Structures and Composites Center (ASCC).
The 3D weaving system consists of an Optima 3D Series 600 shuttle weaving machine with an integrated 2,688-hook Stäubli SX jacquard and harness. It is also complemented by Optima’s compact warp delivery creel and an associated pirn winder for shuttle bobbins and a spool winder for creel spools.
For safety reasons at ITMA 2023, the carbon fibre yarns that will be processed by ASCC on the Optima 3D Series 600 system had to be replaced with polyester, but it was notably the quietest technology in operation during the ear-shatteringly regular intervals of demonstrations held in the weaving halls by the key players in this field.
Versatility
Optima’s looms offer many advanced features over conventional weaving machines, particularly in terms of versatility, as a result of the comprehensive use of digital control systems allowing rapid parameter and sequence changes, coupled with an innovative shuttle system.
“Our aim from the start was to look at 3D weaving machine technology with a fresh pair of eyes and produce a machine that is simply better by design and delivers real benefits to our customers,” says managing director Steve Cooper. “The key interest in this technology has been in producing new structures from expensive fibres such as carbon into workable structures, as the essential reinforcements for composites.”
“The new Optima 3D weaving system will be a cornerstone of a new textile lab we are developing here,” explained ASCC engineer Professor James Stahl. “We chose the loom to take advantage of the design flexibility the shuttle-based weft/fill insertion will provide for fabrics that will be used in soft and hard composite structures and materials.”
Records
The ASCC is certainly no stranger to advanced technology, or indeed ambitious composite projects – in 2019 it received no less than three Guinness World Records, for the world’s largest prototype polymer 3D printer, the largest solid 3D-printed object, and the largest 3D-printed boat. In its latest project it has further introduced BioHome3D – the first 3D-printed house made entirely with bio-based materials developed in a partnership with Oak Ridge National Laboratory. The 182-square-metre prototype features 3D-printed floors, walls and roof which are fully recyclable and highly insulated with 100% wood insulation and customisable R-values. Construction waste was nearly eliminated due to the precision of the printing process.
“With its 3D system, Optima is really taking weaving back to first principles – it’s technology that embodies true innovation in both design and process possibilities,” said Jason Kent, CEO of the British Textile Machinery Association (BTMA). “It’s great that it will contribute to the development of some very forward-looking projects for tomorrow’s sustainable living at the ASCC, and represents another solid example of innovation from the UK.”
Business intelligence for the fibre, textiles and apparel industries: technologies, innovations, markets, investments, trade policy, sourcing, strategy...
Find out more