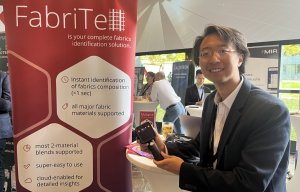
Instant detection with Fabritell
Patch2Patient project has exploited the benefits of FPP.
9th October 2023
Innovation in Textiles
|
Germany
The base technologies for establishing a digital, flexible and automated value chain for the production of personalised composite medical products such as prosthetics and orthotics have been developed in the Patch2Patient project coordinated by Cevotec in Germany.
Cevotec’s fibre patch placement (FPP) technology was employed with adjusted digital tools to integrate patient-specific data into FPP manufacturing.
Fibre reinforced plastic (FRP) is the preferred material for producing the medical device structures due to its weight-related properties and fatigue resistance and while Germany leads in lightweight medical engineering research, the still largely manual production is often outsourced to low-wage countries or results in high costs for the patients. Because many components are customised for each individual patient, automation of production has not been possible with current conventional FRP manufacturing technologies to date.
Cevotec worked with five partners on the project – Carbovation, Mecuris, Guenther Bionics, Otto Bock and the Fraunhofer IPA.
In addition to developing a cloud-based data exchange platform, patient-specific data acquisition and virtual test methods, the partners worked on automated laminate and machine data generation, as well as technologies for multi-material processing with Cevotec’s FPP technology.
“By providing an efficient planning, data processing and manufacturing workflow, the value chain for the production of components such as prosthetics and orthotics can be strengthened in high-wage countries in Europe,” said Dr Florian Lenz, technical director at Cevotec. “In addition, many of the technologies developed can also be used in other industries, such as aerospace, so that further growth of European manufacturers of composite components can be supported.”
Cevotec focused on analysing possible approaches to incorporate patient data into its Artist Studio laminate design software. In addition, it has developed a dedicated material feeding and cutting unit (FCU) as a key enabler for an FPP process suitable for the efficient and economical production of the medical composite products. This FCU is capable of handling different fibre materials and processing patches of variable lengths. In addition to regular carbon and glass fibre slit tapes it is also able to handle cost efficient towpregs, as well as special fibre materials with improved fatigue and impact resistance.
Business intelligence for the fibre, textiles and apparel industries: technologies, innovations, markets, investments, trade policy, sourcing, strategy...
Find out more