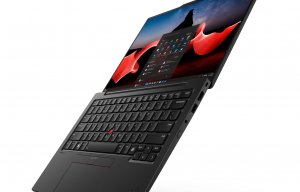
Second life for Boeing’s carbon waste
Lightweight solutions have twin functionality – flame retardence and electromagnetic shielding (EMI).
17th June 2022
Innovation in Textiles
|
Valencia, Spain
Range anxiety is a common worry for electric vehicle (EV) drivers and thermoplastic composites can make a valid contribution to alleviating it.
Aimplas, the plastics technology centre based in Valencia, Spain, is working with the SMART5G Project on a safe, new, efficient and sustainable system which will enable drivers to replace discharged battery packs with charged ones in order to avoid waiting for batteries to charge.
The driving force of this project is the design and development of a battery charging and replacement station for lightweight mobility. The project is specifically focused on developing a system that allows dead batteries to be quickly swapped for batteries charged with solar energy.
The system uses artificial intelligence (AI) algorithms to predict a car’s energy consumption and battery usage and also involves creating an intelligent, energy management platform to improve security and safety and eliminate the risk of electromagnetic interference.
“A strategic priority is to promote new technological solutions that guarantee safe, connected and smart mobility for personal and delivery vehicles, and reduce CO2 emissions,” said Begoña Galindo, a sustainable mobility researcher at Aimplas. “Lightweight, electromagnetically shielded composite materials are being developed within SMART5G to optimise these new models and ensure that the battery is protected against potential electromagnetic interference”.
The initiative is also developing sustainable, structural battery casings for lightweight vehicles based on reusable, recyclable, long-fibre thermoplastic composites with twin functionality – flame retardance and electromagnetic shielding (EMI).
By replacing the old metal casings with the new lightweight thermoplastic casings, vehicle range can be increased by reducing weight, which, in turn, reduces energy costs and consumption.
“Thermoplastic matrix composites could play a key role in industry in the 21st century due to their many advantages, including weight reduction, high rigidity and specific strength comparable to metal materials,” said Galindo. “The new generation of EV manufacturers is starting to use these materials, which enable free design and make cars around 40% lighter.”
Business intelligence for the fibre, textiles and apparel industries: technologies, innovations, markets, investments, trade policy, sourcing, strategy...
Find out more