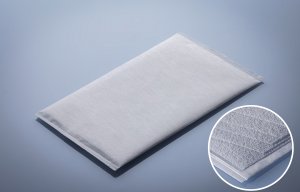
Liquid capture and storage in batteries
Opinion
32,000 visitors and 1201 exhibitors from 100 countries meet face to face in Paris for international composites showcase.
17th May 2022
Marie O'Mahony
|
Paris
Composites are packing greater performance into smaller and more sustainable volumes is the big take-away from the JEC World composites trade show held in Paris on May 3-5, attracting over 32,000 visitors with 1201 exhibitors from over 100 countries making it truly international.
From a fibre and textile point of view there was much to see from recycled carbon fibre and pure cellulose composites to filament winding and hybrid 3D printing of fibres. Aerospace and automotive remain key markets, but with some environmentally - driven surprises in both, while less expected are some novel composite developments in the footwear sector.
Fibre and textile developments for composites
Carbon and glass fibres remain an important focus for composites, however the move towards achieving higher levels of sustainability has seen the development of a recycled carbon fibre (rCarbon Fiber) and the use of hemp, basalt and biobased materials.
The German Institutes of Textile and Fiber Research (DITF) have a strong focus on sustainability from rCarbon Fiber to Biomimicry braiding structures and the use of biomaterials. PurCell is 100% pure cellulose material that is fully recyclable and compostable. The cellulose fibres are dissolved in an ionic liquid which is non-toxic and can be rinsed out and the material dried at the end of the process. To recycle the process is reversed, first chopping the PurCell into small pieces before dissolving in the ionic liquid. It is fully compostable and there is no end-of-life waste. Z-shaped composite materials have been produced with no special technology required. The technology is suited to a number of applications such as interior car parts.
Large scale gets more sustainable
Appealing greatly to the travel-weary visitors the Solvay and Vertical Aerospace Partnership offered a pioneering view of electrical aviation that would allow high speed sustainable travel across short distances. The eVTOL is aimed at urban air mobility with speeds of up to 200mph, zero-emissions and extremely quiet travel when compared with a helicopter at cruise for up to four passengers.
Thermoset and thermoplastic composites are in the main airframe as well as the rotor blades, electric motors, battery components and enclosures. These have been tailored to achieve a balance of stiffness, damage tolerance and notched performance to support the demanding nature of the aircraft with its anticipated frequent take-off and landing cycles.
Composite’s core benefit in sustainability is one of the favourable strength to weight ratio over heavier materials.
A&P Technology are at the forefront of Megabraiders braiding technology taking the technology to another scale – literally. The developments began in 1986 when General Electric Aircraft Engines (GEAE) commissioned a jet engine containment belt well beyond the capability of existing machines, so the company designed and built a 400-carrier braiding machine. This was followed by a 600-carrier braiding machine that was needed for a biaxial sleeving for a side impact airbag for automobiles. This airbag material design resulted in the production of over 48 million feet of airbag braid used by BMW, Land Rover, MINI Cooper and Cadillac Escalade.
Composites in footwear
Footwear is probably the least expected market representation at JEC, and there were a number of developments to be seen. Orbital Composites offered a vision of 3D printing carbon fibre onto shoes for customisation and performance in sports for example. The shoe is itself manipulated robotically as the fibre is printed onto it. Toray demonstrated their capability in composites using Toray CFRT TW-1000 technology composite footplate. A twill weave uses Polymethyl methacrylate (PMMA), carbon and glass fibres as the basis for an ultra-thin, lightweight, resilient plate designed for multidirectional movement and good energy return.
The Toray CFRT SS-S000 (SuperSkin) uses a Thermoplastic polyurethane (TPU) and carbon fibre and used in the heel counter for a thin, lightweight and comfortable fit. Developments such as these pave the way for a more bespoke shoe customised to foot size and shape as well as the performance need. The future of footwear and of composites may never be quite the same.
Business intelligence for the fibre, textiles and apparel industries: technologies, innovations, markets, investments, trade policy, sourcing, strategy...
Find out more