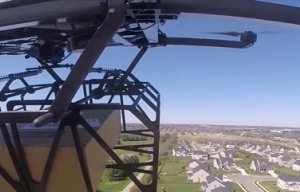
US patent for UAV delivery drone system
Opinion
Carbon fibre-based structures accounted for just 2% of the 13.5 million tons of composite parts produced globally in 2024.
17th March 2025
Adrian Wilson
|
Paris
Anyone visiting an annual JEC World composites exhibition in Paris for the first time would be forgiven for thinking the industry largely consists of carbon fibre creations.
These dominate the exhibition’s landscape in every conceivable form – from aerospace and automotive components to wind blades and sporting goods and on to the hydrogen storage tanks that are seen by many as the next major field for the industry’s growth.
In fact, as Dr Elmar Witten of AVK, the German association for reinforced plastics, pointed out in a conference held during the 2025 JEC World (March 4-6), carbon materials accounted for just 2% of the 13.5 million tons of composites produced globally in 2024, while 95% were glass fibre reinforced plastics (GFRPs).
Globally, composites production in 2024 was up 4% on 2023, but production fell in Europe for the third successive year and it now accounts for 18% of this global market, compared to 30% made in the Americas and 51% in Asia.
GFRPs are very much the workhorse of the industry and get all the dirty jobs – they’re to be found in largely uncelebrated industrial pipes and tanks and as the reinforcement for concrete and plaster and insulation for walls and roofing. And while carbon fibre composites are proudly associated with Formula One racing and advanced aerospace, glass fibre composites generally get to travel in cattle class bus and railway bodies.
Performance and prices
I’m exaggerating of course, but the reasons carbon fibre gets the star treatment are down to both performance properties and price.
Carbon fibres have a significantly higher strength-to-weight ratio than glass, and also provide superior stiffness, enhancing the structural integrity of composites. In addition, they exhibit excellent fatigue resistance and their lower thermal expansion improves dimensional stability, particularly in high-temperature environments. Carbon fibres also have better electrical conductivity, which can be beneficial in aerospace and automotive applications.
Carbon fibre production is meanwhile much more intricate and requires specialised techniques in production, resulting in its much higher cost to start with. This extends down the supply chain.
While exact prices can vary, glass fibre costs around $2-3 per kilogram, while carbon fibre can start at upwards of $50 per kg and much more in applications in the aerospace industry when lightweight and high strength are crucial.
This makes recycling carbon fibres a potentially very profitable activity, even before sustainability is brought into the equation.
At the moment, one of the major trends driving the composites industry is in the replacement of thermoset materials with thermoplastics, in order to enable easier recycling.
This push was notably well represented in the long-list of selected finalists in the 2025 JEC World Innovation Awards, and not just the winners, as explained here and here.
Cement
During a panel discussion during JEC World 2025 entitled From Trash to Treasure: Building a Thriving Recycled Composites Supply Chain, further indignity was unintentionally heaped on glass fibre composites when it was said that one of the most effective routes for them at end-of-life was simply to turn them into cement.
Kim Sjödal, senior vice president of technology and sustainability for Finland’s Exel Composites explained that his company and its partners have developed a co-processing method involving the shredding and crushing of the waste to break glass fibre composites down into more manageable pieces. Subsequently, the prepared composite waste is introduced into a cement kiln, where each constituent element of the glass contributes to the formation of cement clinker – an essential intermediary in cement production. Additionally, co-processing enables energy recovery, because the organic components in the resins generate heat energy during combustion.
Wind turbines
Acciona headquartered in Alcobendas, Spain, however, is meanwhile advancing end-of-life glass fibre options through a wind blade recycling plant in Navarra, Spain, which is set to become operational in 2026.
Anurag Bansal, Acciona’s head of strategic innovations, explained that this is based on a low-temperature thermal recycling process after which the recycled fibres are processed into chopped strand mat nonwoven fabrics for applications in construction, automotive and renewable energy.
In Australia, Acciona has also partnered with professional surfer Josh Kerr and his surfboard brand Draft Surf to create the world’s first surfboards made from retired wind turbine blades.
Zebra project
IRT Jules Verne in France and its partners also claimed the JEC World 2025 Innovation Award in the Renewable Energies category for the Zebra project which has demonstrated the technical, economic and environmental relevance of recycling thermoplastic GFRP wind blades.
Two full scale wind blades with lengths of 62.2 and 77.4 metres respectively were manufactured by Denmark’s LM Wind Power using Elium resin supplied by Arkema and Ultrablade fabrics from Owens Corning Europe. Recycling solutions have been developed to generate recycled Elium monomer and to recover glass fibre at pilot scale and a complete Life Cycle Assessment has shown the environmental benefits of Zebra blades.
The blades of wind turbines currently in operation are made of thermoset composite materials which allow them to combine strength and lightness. Elium liquid thermoplastic resins, however, are now making the production of new thermoplastic blades using established infusion processes.
The key benefits of the Zebra project have been the closed-loop recycling of GFRP waste and the optimisation of the use of resources for raw materials, in addition to the generation of recycled Elium through a thermolysis process.
European production
AVK’s figures for European production in 2024 show that 983,000 tons of GFRP thermosets were produced, a decline from 1,073,000 tons in 2023. The main areas of application for these products remains in the construction/infrastructure and transport sectors.
The production of GFRP thermoplastic composites in Europe was meanwhile 1,368,000 tons, down from 1,423,000 tons in the previous year. As such, the market share for thermoplastic GFRPs in the overall European market is now 58.2% and the transport sector accounts for almost two thirds of their end-use markets, followed by electrical/electronic applications.
Business intelligence for the fibre, textiles and apparel industries: technologies, innovations, markets, investments, trade policy, sourcing, strategy...
Find out more