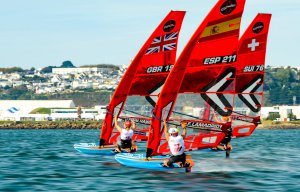
Olympic standards in composites
Wide choice of fibres and filaments, including glass, PAN and PET.
5th February 2024
Innovation in Textiles
|
Baden-Württemberg, Germany
Freudenberg Performance Materials will exhibit a wide range of technical textile solutions for the composites industry at composites show JEC World, the leading international composites show, taking place in Paris from March 5-7.
Experts from the company will be at the Baden-Württemberg International stand in Hall 6 at the show, to explain the benefits of nonwoven surfacing veils for fibre-reinforced plastic (FRP) components and Enka flow media and spacers for composites manufacturing.
To meet the evolving requirements of manufacturers a variety of technologies such as wetlaid, drylaid and spunbond processes are employed to enable a wide range of options in the choice of fibres and filaments, including glass, PAN and PET. These nonwovens are specifically engineered for applications such as anti-corrosive coatings in piping and tank construction, UV-resistant facade panels, and various other end products.
Surface veils are a crucial component of FRP components, ensuring abrasion resistance, corrosion protection, smooth surfaces, and enhanced mechanical strength.
Enka products are designed for efficient resin infusion and foam injection moulding processes. Thanks to their distinctive 3D entangled polymeric filament structures they are exceptionally well-suited as flow media and spacers in composites manufacturing processes.
Flow media for vacuum-assisted resin transfer moulding (VARTM) and resin transfer molding (RTM) processes promote extremely fast and reliable resin distribution ensuring full wet-out of the internal structure, whilst keeping the glass fibre reinforcement nettings and components surface in place. A superior bond, enhanced mechanical properties and even a reduced risk of wrinkling can then be achieved.
The Enka spacer applied in reaction injection moulding using foam pushes the reinforcement matting and composite skin against the mould. This allows polymer foam to flow freely through the mould, filling the cavity completely and resulting in faster production processes that ensure reproducible high-quality finished products.
Business intelligence for the fibre, textiles and apparel industries: technologies, innovations, markets, investments, trade policy, sourcing, strategy...
Find out more