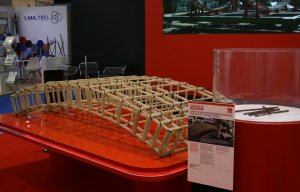
Pultruded tunnel skeleton replaces steel
Process reduces waste, cycle time and material handling costs compared to traditional composite reinforcement methods.
2nd October 2023
Innovation in Textiles
|
Norcross, GA, USA
Braskem, the largest polyolefins producer in the Americas, is working with advanced manufacturing and materials startup WEAV3D, headquartered in Norcross, Georgia, on the development of new polypropylene (PP) structural and automotive composite applications.
WEAV3D feeds commercially available thermoplastic prepreg tapes into its composite forming machine which weaves and consolidates a lattice structure. Automated and continuous, the process reduces waste, cycle times and material handling costs compared to traditional composite reinforcement methods. The machine easily scales to meet automotive part size and production volume requirements.
The WEAV3D lattice technology enables lightweight PP parts to replace materials like steel, increasing their use in automotive applications by balancing improvements in performance, weight and cost. The combination of Braskem PP sheets with WEAV3D’s ‘Rebar for Plastics’ will allow Braskem to compete in new structural material end-markets.
“We’re excited to offer our clients new innovations and partnerships around high-performance polypropylene materials utilising the WEAV3D lattice technology,” said Amanda Zani, technology platform manager at Braskem. “As the automotive industry continues to roll out new electric vehicle designs, car builders need to re-think vehicle design with cutting-edge performance materials. With significant improvements in lightweighting, reduced costs, and higher material efficiency, combining Braskem’s PP portfolio with WEAV3D composite lattices provides a ‘win-win’ in terms of enhanced material performance and a more sustainable environmental impact, that can include the integration of natural fibre options.”
Compared to conventional organosheets, the combination of WEAV3D’s lattices and Braskem PP reduce sheet blank weight and costs by around 50%, while increasing sheet yield from 25% to 45% by weight, resulting in a 63% reduction in trim waste.
“Braskem has been a fantastic partner throughout this project and really demonstrated a strong commitment to sustainable materials innovation,” said Chris Oberste, president of WEAV3D. “Leveraging its diverse portfolio, we worked collaboratively with to identify the right combination of PP and reinforcing lattice material in order to minimise cost and maximise performance, while achieving formability and sustainability goals.”
Braskem will exhibit a prototype beltline stiffener from the collaboration at the Society of Plastics Engineers (SPE) TPO Global Automotive Conference in Troy, Michigan from October 1-4, 2023.
Business intelligence for the fibre, textiles and apparel industries: technologies, innovations, markets, investments, trade policy, sourcing, strategy...
Find out more