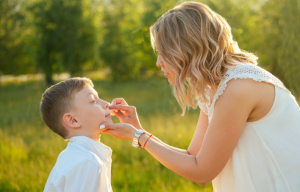
New CAC line for fully biodegradable nonwoven wipes
Carded nonwovens producers can now make their own fibres with a new development which will go on show at INDEX, the leading nonwovens show next month. Staple FORCE S 1000, a new small lot staple fibre production plant from Oerlikon Neumag, is directed at downstream integrators, who want to produce the fibres for their products in-house, enabling nonwovens producers to make and further develop their end products without disclosing know-how and without quality fluctuations.
11th March 2014
Innovation in Textiles
|
Neumünster
Carded nonwovens producers can now make their own fibres with a new development which will go on show at INDEX, the leading nonwovens show next month.
Staple FORCE S 1000, a new small lot staple fibre production plant from Oerlikon Neumag, is directed at downstream integrators, who want to produce the fibres for their products in-house, enabling nonwovens producers to make and further develop their end products without disclosing know-how and without quality fluctuations.
At this year’s INDEX, the leading exhibition for nonwovens, from 8 to 11 April in Geneva, Switzerland, Oerlikon Neumag will be presenting plants and technologies for the production of high-quality nonwovens for hygiene and technical applications. For the first time, the new staple fibre plant Staple FORCE S 1000 will be introduced on stand 2314 in hall 2.
The new, compact plant is specially laid out for the economic production of staple fibres in small lots up to 15 tons per day, as necessary for the production of carded nonwovens. According to the company, the Staple FORCE not only impresses with its low initial investment and compact construction, but also energy costs are significantly reduced by replacing steam and water baths through a dry drawing process.
“The Staple FORCE S 1000 is directed at downstream integrators, who in future want to produce the fibres for their products in-house, enabling the nonwovens producer to produce and further develop his end products without disclosing know-how and without quality fluctuations“, explained Rainer Straub, Vice President Product Management Oerlikon Manmade Fibers.
Oerlikon Neumag has a comprehensive portfolio of nonwoven technologies, from melt-spun spunbond (spunbond and meltblown) up to air-laid nonwovens (airlaid). Application areas include special technical uses such as filtration, roofing, geotextiles and automotive, as well as hygiene applications.
Spunbond technology will also be on the agenda at INDEX. Oerlikon Neumag offers the complete process from polymer chips up to roll goods for the production of substrate for bitumen roofing membranes, sarking membranes and also geotextiles.
The one-step spunbond technology convinces with a combination of effectiveness and productivity, thus lowering production costs by up to 20%. More than 3 million tons of technical nonwovens were produced last year and the demand is still increasing, especially in emerging countries. Thinner, lighter, efficient materials, as produced with the spunbond technology, now specify the trend.
Oerlikon Neumag’s meltblown technology is said to enable the cost-efficient production of high-quality meltblown and SMS (spunbond-meltblown-spunbond) products. Stand-alone mono and bico meltblown plants produce nonwovens for a variety of filtration, insulation and sorbent applications.
The company’s meltblown technology is applied for a multitude of medical and hygiene products as ‘Plug & Produce’ installations in already existing and in new external SXS plants. This solution aims to enable a cost-efficient upgrading of new or existing spunbond plants and offers nonwoven producers access to markets with very high quality demands.
The core of Oerlikon Neumag’s airlaid technology, the forming head, sets standards for the production of extremely thin airlaid nonwovens. A high uniformity and homogeneous web formation, enable the production of high-quality, light airlaid nonwovens with economically attractive production speeds and plant throughputs.
“With the new forming head, we can not only produce very light airlaid materials, but also combination nonwovens with full utilization of the plant capacity, at the same time saving raw material,” the company says.
Business intelligence for the fibre, textiles and apparel industries: technologies, innovations, markets, investments, trade policy, sourcing, strategy...
Find out more