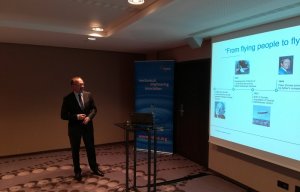
VDMA counts down to ITMA 2019
Six weeks prior to ITMA, Nicolai Strauch, press officer of the VDMA Textile Machinery Association, Germany, spoke to experts of VDMA member companies.
21st May 2019
Innovation in Textiles
|
Frankfurt
Jochen Adler, CTO, Oerlikon Manmade Fibres. © Oerlikon
The future of the textiles industry is more and more determined by Industry 4.0, which has many dimensions and possible fields of application. In three of them (smart services, operations and factory), key solutions are provided by the machinery industry. The other ones from smart textile products, marketing and sales, employees up to strategy and organisation are specific know-how issues for textile mills.
Six weeks prior to ITMA in Barcelona, Nicolai Strauch, press officer of the VDMA Textile Machinery Association, Germany, spoke to experts of VDMA member companies about their products and services with regard to digitisation and Industry 4.0.
In this second series, the interview partners were: Jochen Adler, CTO, Oerlikon Manmade Fibres; Rebekka Dilo, Assistant to the Management, Oskar Dilo Maschinenfabrik; Klaus Heinrichs, Vice President, Monforts Textilmaschinen; Dr Janpeter Horn, CEO, Herzog; Leonhard Kemnitzer, Head of Marketing, Baumüller Nürnberg; Steffen Müller-Probandt, Managing Partner, Dienes Apparatebau; Marcus Ott, CEO, Halo electronic; and Jochen Stillger, Head of Sales, Thies.
Nicolai Strauch: Mr Adler, what can your customers expect digitally from Oerlikon?
Adler: I would say the digital refinement of our machines and production systems for manufacturing yarns, fibres, nonwovens along the textile value chain. We want to further optimise the efficiency of the systems and the quality of the end products with digital solutions.
For this, we are deploying the know-how of our newly-integrated partner AC-Automation – which specialises in large-scale systems automation, transport, packaging and warehouse logistics and end product automated quality control. We combine this with our process competencies and digital data handling using our Plant Operation Center (POC).
Dienes specialises in machine components for the manmade fibre production. © Dienes Apparatebau
This has created Industry 4.0 solutions for our customers – with integrated storage and communication capabilities, wireless sensors, embedded actuators and intelligent software systems. In turn, this allows us to build bridges between data and material flows and between the virtual and real worlds.
NS: And what aspects of all this can visitors already see at the ITMA in Barcelona?
Adler: At our trade fair stand we will be offering our visitors a digital experience that allows them to intensely discover and understand our machines, systems, components and services. Here, we will be deploying playful solutions to present the topic of artificial intelligence. We will be taking our 360-degree and augmented-reality applications as well as our virtual showroom with us, to allow visitors to experience complex systems live in 3D. The digital factory is already in part becoming a reality in conjunction with our machine exhibits.
NS: Mr Müller-Probandt, company Dienes specialises in machine components for the manmade fibre production, as well as textile special applications. One focus are pilot installations for research. How is Industry 4.0 touching this application?
Müller-Probandt: One key product in our portfolio is a modular spinning system, which allows customised solutions, starting from thread run studies to complete pilot installations.
Each unit has its own PLC (Programmable Logic Controller), which allows to run Dienes units in foreign lines or to integrate foreign units in a Dienes line. The units can be operated with an interface directly or over the ethernet from an upper control system.
NS: What are the advantages for customers e.g. research institutes or R&D departments?
Müller-Probandt: Our modular system includes a line overview, which rearranges itself almost automatically for different operation modes in alternative machine sequences. The detailed process representation allows the customer to monitor directly the effect for all changes of parameters.
If a good yarn could be realised it is possible to backtrack the journey of this yarn through the process.
Rebekka Dilo, Assistant to the Management, Oskar Dilo Maschinenfabrik. © Dilo
The parameters can be modified with mobile devices, like a pad or a mobile phone. All these functionalities allow the research institutes and industry to reduce the cost of investments and to operate fast and flexibly in the development of new products, which additionally save costs and time.
NS: Let’s move forward in the textiles chain. Ms Dilo, how can Industry 4.0 help customers in the nonwovens industry to increase efficiency and so to decrease costs?
Dilo: Our new operator system assists the operators through intelligent sensors and automatised modes allowing a reduction of workforce at nonwoven lines. At a line restart, the newly formed web may wrap around rollers in the card and crosslapper. The new starting mode automatically prefills the line and forms a stable start nonwoven, minimising the risk of wrappings.
NS: What is the effect of this?
Dilo: As a result, the line starts smoothly with minimal manual intervention. Moreover, an energy-saving technology helps to decrease costs at the fibres transport, one of the main energy consumers in needling lines. Instead of operating the ventilators for the fibre-air transport at maximum frequency, the system controls the ventilator speed according to the actual throughput and also gives warnings before blockages can occur. The technology therefore targets eco-sensitive nonwoven producers, who also want to increase their line availability.
This targets especially producers working with fibre blends and several bale openers respectively.
NS: Dr Horn, Herzog is producing braiding machines. What is your latest I4.0 product and what is your approach?
Dr Horn: An additional module for Herzog machines, an app-box, with which Industry 4.0 scenarios can be realised without employing software teams or starting big Industry 4.0 projects. This technology is an app-based one. Apps can be downloaded and installed easily.
NS: How do customers benefit from this?
Dr Horn: The customer can easily access the data of Herzog machines, e.g. on a PLC (Programmable Logic Controller). The data can be visualised on dashboards created by the customer on terminals or others.
Dr Janpeter Horn, CEO, Herzog. © Herzog
The data can be processed, e.g. by creating key figures, alarms or analysation. Alarms and information could be transferred by e-mail, messengers. Furthermore, the data can be linked to order from pps systems or transferred to the machines – if the customer decides to go this way.
NS: Can you quantify the benefit?
Dr Horn: No formation of software teams outside machines. New applications could be created easily. No additional software.
NS: What is really new at this solution?
Dr Horn: It is the result of a three-year research project. Various innovations have been implemented: The use of cloud technologies on the shop floor; open source technologies for inexpensive apps; no internet connection is necessary. The main advantage however is the “one-click” installation of apps which have been applicable only for smartphones and tablets. The apps are installed in a so-called box outside the machines.
NS: The last steps in the textile chain is finishing. Mr Heinrichs, what will Monforts present at ITMA?
Heinrichs: Thanks to a support app for communication and an app for operating Monforts systems, Monforts machines now feature a digital twin that will be presented to the textile industry for the first time ever at ITMA in Barcelona. With the help of advanced sensor technology, all technical data are mapped in the cloud virtually and in real time. The data in the cloud indicate the current state of the system with its respective specifications and can map the entire production process, enabling targeted analysis and controlled planning and production: Insights harnessed from data analyses can be used to optimise the actual production process.
NS: What is new about your solution / technology?
Heinrichs: The status overview in real-time improves machine availability while minimising downtime considerably. Potential sources of error can be anticipated and eliminated. The digital twin provides information on individual wear parts of a system, such as converters or gears, for example. In the future operators will be able to see how long a wearing part will last and when it has to be maintained or replaced ahead of time. Direct access to the integrated Monforts webshop allows users to order wearing and spare parts at the press of the button when they are needed, virtually preventing machine downtime.
Klaus Heinrichs, Vice President, Monforts Textilmaschinen. © Monforts
On request, Monforts can monitor machine availability and proactively approach customers if action is required. Data is only ever called from the cloud provided customers have agreed, requiring their consent in the interest of data security.
NS: What advantages does this offer for your clients?
Heinrichs: With the support app, the customer can contact Monforts service virtually 24 hours a day or at an arranged time via smartphone or tablet. Support is given right on site via a video connection. The Monforts service specialist can point out individual system parts on the customer’s smartphone using a mouse cursor and assist users in troubleshooting or operating the machine on site. Documents, such as machine documentation, can also be shown in real-time on the smartphone. Data can be used to analyse a system’s energy requirements. For example, machine operation can be optimised for production to go into full operation when electricity costs are at their lowest.
NS: Let’s stay in the finishing process. Mr Stillger, the company Thies specialises in dyeing technology. What is your latest I4.0 product?
Stillger: For the ITMA 2019 we offer a new version of our maintenance system, which, among others, was extended by the condition monitoring module. It is an automated planning, execution and monitoring software for inspection, service and routine maintenance, which not only facilitates the procurement of spare parts, but also provides the corresponding technical documentation digitally. At the same time, we are laying the foundation for future machine-specific and customised machine-based learning from the history data.
In addition, a new controller generation will be offered together with one of our control suppliers, which will be open for I4.0 applications and at the same time can be connected to the corresponding MES (Manufacturing Execution System).
NS: What specific benefit does a customer get from your solution / technology?
Stillger: Optimisation of production processes and production safety through completely transparent planning, implementation and monitoring tools. In the medium term, a significant reduction in process and maintenance time is achieved. There will be a reduction in the failure rate and the time to fix failures.
Halo electronics from Austria develops Enterprise-Resource-Planning (ERP) systems for the textiles industry. © Halo
All in all, a reduction in maintenance costs due to a purposefully controlled spare parts inventory and a prioritised and more efficient maintenance is expected.
NS: Can you prove this with some facts and figures?
Stillger: Customers will achieve higher machine efficiency through intelligent maintenance. Depending on the individual situation in the dye house, optimisation of the processes may reduce the costs by 20 to 50%. Successful energy management (managing energy allocation) can lead to an additional 7% to 10% reduction in costs.
NS: The VDMA supports the mechanical and plant engineering industry in the development of OPC / UA Companion Specifications. OPC / UA is an open interface standard that defines the mechanisms of cooperation in the industrial environment. What advantages does OPC / UA provide with regard to your solution / technology?
Stillger: The OPC / UA interface enables standardised data transfer. A significant improvement in data quality is achieved. The new technology introduces customer-specific and system-specific monitoring of the functioning of the machine. Smarter sensors are used for process monitoring. Forward-looking history data are collected for the configuration of self-optimising AI processes.
NS: Mr Ott, your company Halo electronics from Austria develops Enterprise-Resource-Planning (ERP) systems for the textiles industry. Please, tell us more about your company.
Ott: We provide custom-tailored IT solutions, that offer textile industry customers the perfect level of data transparency - from fibre to finished product. Direct communication between man and machine not only enables this consistently transparent presentation of all relevant data, but also gives employees flexible and, most importantly, mobile access to it. All important information is available on the handheld device while "on the go".
NS: How is the usability of your solution? Can you quantify the benefits of the product?
Ott: The intuitive software relies on language-independent icons instead of text and can therefore be used without training in any work environment. The resulting cost savings are clear.
Baumüller is a manufacturer of intelligent drive and automation systems as well as software for numerous branches, including textile machinery. © Baumüller
The seamless implementation of the software in all relevant production processes up to the point of delivery enables complete consistency and transparency of the data collection, which simplifies optimisation processes and gives management vital decision-making information. For example, the use of our software enables time savings of 45% for the storage and retrieval of products in the warehouse.
NS: Mr Kemnitzer, Baumüller is a well-known manufacturer of intelligent drive and automation systems, as well as software for numerous branches, including textile machinery. One focus is simulation software. What’s actually new?
Kemnitzer: Many simulation tools graphically depict machines and systems as 3D simulations. These standard tools focus on the behavior of the machines under optimal conditions. Our simulation software starts one step ahead. In the first step, the drives and the mechanical parts are selected for the respective application task in order to then verify the motion profiles of the machine.
NS: What advantage does the software offer?
Kemnitzer: Our software is very user-friendly. With classical simulation tools a large number of different parameters has to be entered. The advantage of our tool is the great simplification of the models without losing their accuracy. Application engineers can work with ready-made models that are just as accurate from the calculation cycles as they are in other simulation tools. Due to the complete integration in the operating software, the models are automatically parameterised and changes can be carried out very quickly. The result of the simulation process is a parameter set which can be used in the real application. This saves much time in the engineering process and reduces the time to market.
NS: Thank you very much for this Industry 4.0 journey along the textile chain plus supplier. More than 200 VDMA member companies will exhibit at ITMA end of June. We are eagerly looking forward to a fantastic and successful ITMA in Barcelona.
Further reading
Business intelligence for the fibre, textiles and apparel industries: technologies, innovations, markets, investments, trade policy, sourcing, strategy...
Find out more