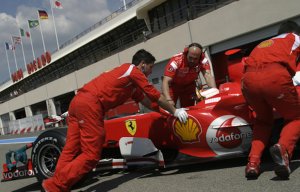
Benwel to market auto racing FR garments treated with Alexium technology
Having secured significant additional finance in the past few weeks, Alexium now has a clear roadmap for accelerating the industry take-up of its potentially groundbreaking new flame retardant and oil and water repellent nylon treatment.
7th March 2012
Innovation in Textiles
|
Greer, SC
Having secured significant additional finance in the past few weeks, Alexium now has a clear roadmap for accelerating the industry take-up of its potentially groundbreaking new flame retardant and oil and water repellent nylon treatment.
Speaking at a special web conference on March 6th, executive director Stefan Susta said the company’s immediate priority was to scale-up and install its equipment – specifically for the treatment of FR nylon – at the plants of its commercial partners.
“The first installation will be in the USA, where the flame retardant coating of nylon is very strong, compared to Europe, where polyester fabrics tend to predominate,” he said. “Our new production unit at Greer in South Carolina is capable of trials in runs of thousands of yards, but the next stage is to install a line capable of production running into millions of yards. After the USA, a second installation will be in Australia.”
During 2011, Alexium announced commercial partnerships with International Textile Group (ITG), part of the multiple-industry empire of entrepreneur Wilbur Ross, and with Bruck Textiles, Australia’s biggest technical textile manufacturer.
Alexium’s RST – Reactive Surface Technology – is based patented microwave driven chemistry which enables nanoscopic coatings to be applied to a wide range of fibres in a continuous reel-to-reel process –a significant advantage in respect of compatibility with existing textile manufacturing equipment.
Certain fibres, such as aramids, polypropylene and nylon are relatively inert and don’t have very reactive surfaces. As a consequence, conventional textile coatings commonly rely on chemical bonding with the surface of the material, which can be challenging without these reactive sites.
RST coatings, however, can covalently bond to the surface of the fibre or when that is not possible, form a nanoscopic intractable coating around the individual fibres. The process is fast and environmentally friendly, enabling single or multi-functional coatings to be applied to most fibres almost regardless of their surface chemistry.
The process is based on organosilanes – silicon-containing chemicals that contain both organic and inorganic functionalities in the same molecule – which are already widely used as coupling agents across a range of industries and commercially manufactured by the likes of Bluestar, Degussa, Dow Corning, Evonik and Wacker.
Specifically, the Alexium flame retardant treatment is based on a mechanism which promotes the formation of a protective nanocomposite char layer – without the dripping or melting which is characteristic of many synthetic FR fabrics. In addition, its performance is provided without using halogenated chemicals, and while heavy back coatings are also currently available for rendering nylon flame retardant, they have limited application due to their high weight and impermeability.
Due to the inherent advantages over other fibres, nylon remains the top choice for many outdoor apparel systems, including the cold weather clothing systems which are issued to each core soldier in the US military. The US military currently has 1.4 million soldiers serving in active service and 800,000 soldiers on reserve duty.
“We can clearly see where our FR treatment can make an impact in the marketplace and we are excited about the potential and very pleased with the progress our technical team has made to date,” said Susta. “It’s a revolutionary approach and very different from any other FR treatment. After transitioning the technology to licensees for nylon, we will be exploring applications on other synthetic fabrics and blends.
“We will also be working to ensure that as a technology company we don’t miss opportunities for our chemistry to translate into other fields, including filter media, composites and functional polyolefins.”
Business intelligence for the fibre, textiles and apparel industries: technologies, innovations, markets, investments, trade policy, sourcing, strategy...
Find out more