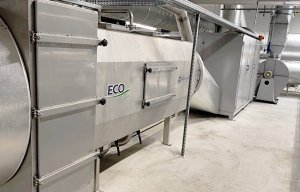
Feinjersey minimises energy consumption with Brückner
The exhaust air treatment on the new stenters of Getzner is carried out by a multi-stage Brückner Eco-Heat and Eco-Air system.
31st January 2019
Innovation in Textiles
|
Leonberg
Getzner AG in Bludenz, Austria. Image source/photographer: Jens Ellensohn, Koblach/A
Vorarlberg is the westernmost province of Austria, bordering Switzerland and Germany. With the impressive alpine scenery, it is not surprising that many tourists come here who like hiking or skiing. Although Vorarlberg is a famous tourist destination, only about 6% of the gross social product is generated by tourism – a sign of a strong industry with a high export share.
The textiles industry, probably the strongest branch of industry in the last two centuries, has lost its supremacy there in the meantime. However, it is still prominently represented: one of the 20 largest industrial companies in Vorarlberg belongs to the textiles industry – Getzner, in Bludenz.
Founded 200 years ago, Getzner is a leading company for the production of African damask fabrics and one of the leading manufacturers of shirt fashion fabrics. In the new production halls at Getzner’s main plant in Bludenz, fabrics are woven and finished for ready-made garments in special processes, mainly on new Brückner stenters. As substances evaporate from the fabric during the textile finishing processes, the stenters have to be vacuumed off and this exhaust air has to be cleaned before being emitted into the environment.
Eco-Heat air/air heat-recovery system. © Brückner
The exhaust air treatment on the new stenters of Getzner is carried out by a multi-stage Brückner Eco-Heat and Eco-Air system. In the first Eco-Heat heat-recovery system, heated fresh air is generated for the drying process, which noticeably reduces energy consumption. In the second Eco-Heat heat-recovery system, water is heated for the company’s internal heating system and thus, depending on the heating requirement, up to 85% of the invested heat energy is recovered. The pollutants from the exhaust air are condensed and separated in the subsequent Eco-Air exhaust air scrubber. A silencer behind the exhaust air fan reduces the exhaust noise to a minimum.
The Eco-Heat components are designed to guarantee high heat transfer efficiency and a particularly robust and maintenance-friendly design. Since the heat exchangers have to be cleaned at regular intervals from unavoidable deposits in order to maintain full performance, they are easy to remove, according to the manufacturer. The heat exchangers are boiled regularly in the cleaning bath supplied. As Getzner has replacement heat exchanger modules in stock, the heat exchangers are cleaned without any time pressure.
With this modern multi-stage exhaust air system Getzner says it achieves a high energy efficiency, because most of the exhaust air heat is recovered in Brückner Eco-Heat systems. “In addition, the environment is not polluted by smoke, noise and odours from the production process, thanks to the Brückner Eco-Air exhaust air cleaning system.”
Business intelligence for the fibre, textiles and apparel industries: technologies, innovations, markets, investments, trade policy, sourcing, strategy...
Find out more