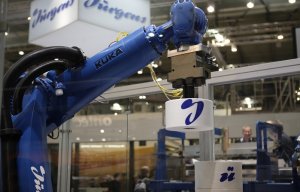
ITMA highlights innovation for its second Barcelona edition
The future of the textiles industry is more and more determined by Industry 4.0, which has many dimensions and possible fields of application.
20th May 2019
Innovation in Textiles
|
Frankfurt
Dr Christof Soest, CTO, Trützschler. © Trützschler
The future of the textiles industry is more and more determined by Industry 4.0, which has many dimensions and possible fields of application. In three of them (smart services, operations and factory), key solutions are provided by the machinery industry. The other ones from smart textile products, marketing and sales, employees up to strategy and organisation are specific know-how issues for textiles mills.
At the ITMA 2019 in Barcelona, next month, visitors will have the chance to see how Industry 4.0 solutions are impacting the textiles process chain. Six weeks prior to the show, Nicolai Strauch, press officer of the VDMA Textile Machinery Association, Germany, spoke to experts of VDMA member companies about their products and services with regard to digitisation and Industry 4.0.
Interview partners were: Andreas Hannes, Marketing Manager, Sedo Treepoint; Maximilian Kürig, Managing Director, KM.ON, a software start-up company of Karl Mayer; Wilhelm Langius, Division Head, Neuenhauser; Andreas Lukas, Managing Director, Andritz Küsters; Rainer Mestermann, Managing Director, Mahlo; Axel Pieper, CEO, Brückner Trockentechnik; Eric Schöller, Managing Director, Groz-Beckert; and Dr Christof Soest, CTO, Trützschler.
Nicolai Strauch: Dr Soest, what is Trützschler’s latest I4.0 innovation?
Dr Soest: We have developed intelligent, self-optimising machines and connect them through digital monitoring systems. The latest examples are cloud-based monitoring solutions which enable customers to literally steer and optimise their spinning mill anytime from anywhere in the world. This combination of complete, intelligent machinery solutions and digital support systems means a big step in automation and ensuring high quality.
NS: And what is the exact benefit for a spinning mill?
Dr Soest: Customer benefits range from improved productivity and quality to fewer downtimes, machine failures and reduced scrap. One of our monitoring systems, for example, warns operators about potential issues or optimisation needs. It also specifies where exactly they occur and advises what needs to be done. There is no need for time-consuming searches for the source of the issue. This saves a lot of time and money! By connecting all machines in a unified data set, we eliminate the information silos that made it difficult to steer production in the past.
NS: Let’s stay in the spinning sector. Mr Langius, company Neuenhauser specialises in the handling of yarn packages within the yarn spinning process. Are transportation systems also influenced by Industry 4.0?
Langius: Indeed, a good example is a new development for the automated handling of sliver cans. Have you ever heard of AGVs?
NS: Should I?
Langius: AGV stands for Automatic Guided Vehicles, a technology that has been around for many years but has been fuelled recently by the introduction of Industry 4.0. Neuenhauser saw with the recent advances in autonomous vehicles and navigation systems that an AGV is also a good solution for spinning mills.
AGV in motion. © Neuenhauser
We thought it is a useful tool to automate the labour-intensive handling of sliver cans in a spinning plant. Within twelve months, our team developed a state-of-the-art transport system using a large fleet of intelligently controlled automated guided vehicles. The AGV will pick-up sliver cans which are filled with cotton sliver material and deliver them to the spinning frame where empty cans will be exchanged with full cans. The empty cans are then returned to the equipment which will refill the sliver cans with cotton sliver to repeat the cycle. Within a typical spinning mill, very large numbers of sliver cans are required to be moved each hour.
NS: And how do you make sure these vehicles find their way in a spinning mill?
Langius: The vehicles are equipped with the latest state-of-the-art safety sensors to ensure the vehicles operate safely alongside plant personnel who need to share the same floor space and aisles within the spinning mill. The plant personnel are also equipped with specialised sensors they wear on their safety vest, to inform the AGV where the operators are working and moving around within the manufacturing floor. With such a system both the AGVs and local plant personnel can work safely together within the same manufacturing area.
NS: Let’s go a step forward in the textiles chain. Industry 4.0. is also an issue in fabric production. Mr Kürig, at ITMA ASIA 2018 Karl Mayer launched its own digital brand, KM.ON. What is new in the associated digital solutions portfolio with regard to production?
Kürig: KM.ON’s range of features has been extended considerably. A good example from Karl Mayer is a new digital tool that combines a PDA system with a ticket system to enable any disruptions in production to be managed efficiently.
KM.ON is a software start-up company of Karl Mayer. © Karl Mayer
The relevant information can be input easily and quickly at the machine and forwarded to the appropriate location in real time. Any problems can be dealt with quickly, and the root cause can be tackled rapidly by displaying the relevant sequence.
NS: What does this tool mean for the machine operator? Is it an operator friendly technology?
Kürig: This system is very easy to operate, which means that this new development can be used immediately.
NS: Integral parts in knitting, warp knitting and sewing are needles. Mr Schöller, will needle handling also move to a digital level?
Schöller: Yes, indeed. Groz-Beckert has developed a quality and life cycle management system for needles. It organises each needle in a clearly structured process and documents them digitally, from arriving at the factory to leaving for recycling.
NS: How do customers benefit from this system?
Schöller: This quality management system makes it possible to efficiently conduct audits and, as part of the digitalisation process, provides a complete overview of KPIs (Key Performance Indicators) with the option of implementing predictive maintenance measures. Customers also benefit from the ability to improve machine utilisation and identify weak points in production. The use of the system reduces needle consumption at factories by up to 10%. Downtime during needle changes also decreases by 50% on average. Moreover, the risk of contractual penalties due to non-compliance with brand owner specifications goes to zero.
Smart INH: Groz-Beckert's answer to the challenges of the digital age. © Groz-Beckert
The use of the system also eliminates the need to store used needles for documentation purposes; the needles can be sent for recycling right away – a decisive benefit in the sense of sustainability.
NS: Mr Lukas, Andritz Küsters specialises in technologies for the nonwovens industry. Which steps have been taken recently to address the topic I4.0?
Lukas: Andritz has pooled its relevant expertise under a new technology brand that covers smart sensors, big data analytics and augmented reality.
NS: Augmented reality is a good topic that has not been mentioned so far. What are the advantages of this technology?
Lukas: Portrayal of important information where operations are taking place and always with respect to the product or object are compelling arguments in favour of using Augmented Reality.
Andreas Lukas, Managing Director, Andritz Küsters. © Andritz Küsters
Other benefits for customers: Conventional operating manuals are converted into digital instructions, virtual tools can be displayed in the real work environment, and users can perform difficult work sequences with a lower error rate.
NS: Gentlemen, in the daily press I get sometimes the impression that I4.0 / digitization is an end in itself. Mr Pieper, in textile finishing, energy consumption plays a crucial role. Can I4.0-solutions help to reduce energy costs?
Pieper: Brückner has developed an intelligent machine assistance system that monitors the settings of the entire system in the background. Deviations from default values are immediately signaled to the machine operator and stored in the production history logbook. A new simulation tool helps the machine operator to get the highest possible productivity and/or energy savings out of the system. Maintenance and spare part suggestions are displayed preventively after a certain interval. Upcoming maintenance tasks are comprehensively visualised for the maintenance department and can even be retrieved from mobile devices.
NS: How can a finishing company realise savings potentials with this solution?
Pieper: During production, a production assistance system helps the operator to decide which parameters need to be adjusted to make the system even more energy-efficient and productive. Optimised recipes can be stored for future processes and are therefore very easy to reproduce. At the customer's request, we can also connect his system to a higher-level control station system.
Axel Pieper, CEO, Brückner Trockentechnik. © Brückner Trockentechnik
This allows recipe data to be researched in a central data base and to be shared with other users. This new intelligent assistance system in combination with the simulation tool allows productivity increases of up to 40%. Energy consumption can be reduced by up to 30% with these systems.
NS: Let’s stay in the finishing process. Mr Mestermann, company Mahlo develops and produces measurement and control equipment for the textiles and nonwoven industry. A basic idea of Industry 4.0 is collecting and processing data for better production results. How is Mahlo addressing this issue?
Mestermann: A new platform from Mahlo realises these ideas of industry 4.0 with digital technologies. In the digitisation concept for all Mahlo products, the functionalities are grouped, optimised and standardised as "services". This results in modular hardware and software function blocks that can also be retrofitted. There are modules, e.g. for the acquisition and processing of measured values, for control tasks or for the long-term archiving, data logging and analysis.
NS: Why should manufacturers and finishers of textile fabrics invest in your solutions?
Mestermann: Our new platform makes it easier for customers to use data in a meaningful manner to optimise their processes. Networking of Mahlo devices with each other and with other systems ensures consistent data exchange and enables the bundling of information as a basis for process improvement. Higher machine availability through remote maintenance via better product quality by adaptive control or flexible data analysis as the basis for better decisions provide immediate monetary benefits.
NS: Can you quantify the benefits, please?
Mestermann: One example is the control module in our weft straighteners. Together with a renowned university, the distortion control was revised and digitised. Optimised hardware and software resulted in a faster and more efficient controller.
Rainer Mestermann, Managing Director, Mahlo. © Mahlo
Evaluations confirmed by customers prove that the control module regulates 20% faster and more precisely than before. Better straightening results reduce the production of second-choice goods and the need to pass the same fabric through the stenter several times.
NS: Mr Hannes, tell us something about the portfolio of Sedo-Treepoint.
Hannes: We are known for smart factory integration and offer integrated textiles management systems along the textiles production chain, such as spinning, weaving, knitting, dyeing, finishing, printing and inspection. For all departments, PPS, routing of orders (track and trace) or energy management is available. Existing ERP systems are integrated as well, so double entry of existing information is avoided.
NS: What can we expect from your company at ITMA in Barcelona?
Hannes: We will introduce a new series of our dyehouse controllers. The new series is specially designed for Industry 4.0. The open connectivity on production and machine level improves the M2M-communication. Important information for the production floor is displayed wherever required.
NS: Gentlemen, thank you very much for this discussion. More than 200 VDMA member companies will exhibit at ITMA end of June. We are eagerly looking forward to a fantastic and successful ITMA in Barcelona.
Business intelligence for the fibre, textiles and apparel industries: technologies, innovations, markets, investments, trade policy, sourcing, strategy...
Find out more