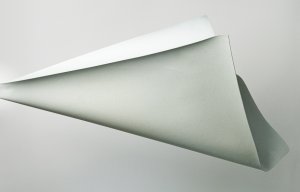
Mirum and Tencel as alternative leather
Technology based on precisely manipulating intermolecular bonding in natural polymers.
16th July 2021
Innovation in Textiles
|
Peoria, Illinois
Natural Fiber Welding (NFW), of Peoria, Illinois, has closed a new $15 million funding round and formed a strategic partnership with BMW Group as it continues to scale up production of its Mirum plant-based alternative leather.
BMW has set ambitious sustainability targets as it aims to reduce CO2 emissions along the entire value chain and to achieve this, is seeking to make use of recyclable materials, or materials that have a lower carbon footprint, while still retaining the same high functionality, aesthetics, and premium quality.
According to a Market Study report, synthetic leather materials are estimated to be the largest segment of the automotive upholstery market.
With its durability, quality, and tunability, NFW’s patented high-performance, plastic-free Mirum is well-suited to displace both animal leather and synthetic leather alternatives. Leveraging the strength and diversity of virgin and recycled plant matter such as coconut husk, rice hulls, and cork, Mirum requires no plastic binders or coating.
“With our new manufacturing capabilities and the support of companies like BMW i Ventures, we are advancing NFW’s mission to eliminate the need for plastics,” said Dr Luke Haverhals, CEO and founder of NFW. “The extensibility of our platform and the tunability of NFW materials means that we can serve many customers spanning multiple large, global markets. We are energized daily by the commitment of major brands and companies to partner with NFW.”
Earlier this year, NFW announced a new 110,000 square feet of manufacturing space dedicated to the production of Mirum. The company currently employs approximately 130 people at its Peoria headquarters and is continuing to grow aggressively as it scales up commercial manufacturing. With the expansion, NFW anticipates adding as many as 240 new jobs to the Peoria area.
“Natural Fiber Welding has developed an innovative process for converting plants into all-natural, 100% recyclable material that mimic all the properties of traditional leather, yarns and foams,” said Kasper Sage, managing partner at BMW i Ventures. “Having a scalable, cost-competitive alternative to leather with premium qualities is the key to further advancing the decarbonization of the automotive industry.”
NFW has also developed Clarus enhanced natural fibres which in yarns and fabrics are strongly held together using natural bonding systems for reduced fraying, pilling, and abrasion damage. By changing the shape and format of natural fibres, the way moisture and sweat is absorbed and transported through Clarus fabrics can also be drastically improved compared to standard cotton.
Both technology platforms have been built on the science of ‘welding’ fibres – the process of precisely manipulating intermolecular bonding in natural polymers. NFW technology creates more of these bonds for stronger yarns and fabrics.
Business intelligence for the fibre, textiles and apparel industries: technologies, innovations, markets, investments, trade policy, sourcing, strategy...
Find out more