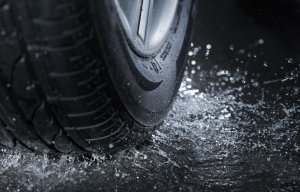
Indorama expands ISCC+ range for Mobility
Certfication will track both sourced caprolactam feedstocks and in-house mechanically recycled fibres.
1st July 2024
Innovation in Textiles
|
Zaragoza, Spain
Integrated producer of synthetic nylon fibres, technical polymers and biopolymers Nurel, headquarters in Zaragoza, Spain, has received ISCC+ certification for its mechanical recycling process and the manufacture of polyamides and a variety of polymer-based products.
In Zaragoza, the company carries out polymerisation, compounding and spinning activities with the latest technologies and has committed to both increasing the use of ISCC+ certified non-conventional materials and to mechanically recycle production waste on-site.
ISCC is a leading international certification system which certifies fully traceable and more sustainable, deforestation-free and climate-friendly supply chains. A system dedicated to the circular economy and bioeconomy, ISCC+ certifies non-conventional feedstock as chain of custody options, as well as mechanical and chemical recycling processes.
“ISCC+ provides companies aiming to be certified with a range of certification options, from a single source,” says ISCC system manager Sina Tischbierek. “We are pleased that Nurel has opted for it and is profiting from our robust and credible system.”
“We decided to apply for ISCC+ certification for the material we source, the chain of custody option we use and our mechanical recycling process,” adds Silvia Catalán, sustainability manager at Nurel. “With ISCC certified materials and procedures, we can reduce the environmental impact of our production and make credible claims to our customers. The certification system covers a wide range of materials and processes and is ideal for us.”
Nurel sources ISCC+ certified caprolactam made from pre and post-consumer residues or biomass. Depending on the application the certified materials are used for, they are mixed with virgin materials to achieve the respective qualities and target volumes.
Once the certified materials are mixed with non-certified materials, it is impossible to physically segregate them. Nurel therefore applies the mass balance methodology that allows manufacturers to track the certified materials as they move along the value chain and attribute certified inputs to outputs by segregated bookkeeping. This verified accounting method certifies that the certified feedstock that has replaced virgin fossil-based raw materials at the beginning of the supply chain can be attributed to the product-to-be-sold while ensuring that input and output are balanced.
“We buy ISCC certified caprolactam and feed it into our production plant,” Catalán explains. “In the end, we attribute 100% of certified caprolactam to our polyamide 6, which serves as a basis for our PA6 yarn or our PA6 based compounds. Finally, our certified products are sold to a customer, who can now make a better-informed purchasing decision.”
Nurel already recycles its production waste on-site through a mechanical recycling process that preserves the material’s molecular structure and sorts waste by material type and colour. The company sorts post-industrial and post-consumer waste into high-purity fractions of polyamide waste. In a first step, contaminants and unwanted materials are removed from the waste stream. Depending on the contamination level and purity requirements, the materials might then pass through a second sorting process. The pure polyamide waste fraction is then shredded into smaller material fractions. Afterwards, the materials are pelletised and turned into recycled polyamide that can be directly sold or used as base polymer for new high-quality compounds.
“In addition to recycling PA waste generated in the production process, we also offer the possibility to collect post-industrial waste from our customers,” Catalán says. “Thanks to our know-how and experience in the textile sector, we are able to recycle textiles containing nylon and elastane. We use a special thermo-mechanical recycling technology that enables us to turn waste into engineering polymers for higher applications.”
Nurel recycles more than 1,000 tons of post-industrial polyamide waste per year, resulting in more than 1,000 tons of recycled materials. With its mechanical recycling process, the company contributes to maximising the materials lifecycle, reducing waste generation, CO₂ emissions and water consumption. In the future, the company will extend its mechanical recycling operation and additionally process waste generated by the plastics industry and community.
“Mechanical recycling provides vast opportunities for the circular economy,” Sina Tischbierek explains. “For us, mechanical recycling should be the first go-to-option when it comes to recycling, so we are delighted that Nurel is among the companies embracing mechanical recycling with the ISCC+ certificate. This enables the company to demonstrate its sustainability commitment and provide greater transparency to the supply chain and customers.”
Business intelligence for the fibre, textiles and apparel industries: technologies, innovations, markets, investments, trade policy, sourcing, strategy...
Find out more