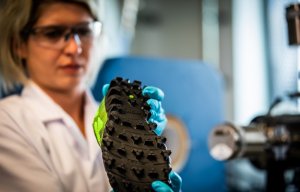
inov-8 unveils graphene sports shoes
Successful electrospinning of flour and formic acid mixture.
28th November 2024
Innovation in Textiles
|
London
Highly porous nanofibre nonwovens made of starch show promise in wound healing as scaffolding for bone regeneration and for drug delivery, but extracting and purifying the starch from plant cells is very energy and water intensive.
A more environmentally friendly method which is being explored by University College London (UCL) researchers is to create the nanofibres directly from a starch-rich ingredient like flour.
In a new paper in Nanoscale Advances, the team describe making nanofibres of just 372 nanometres by electrospinning, in which threads of flour and liquid are extrided and formed by an electric charge.
“To make spaghetti, you push a mixture of water and flour through metal holes and in our study, we did the same except we pulled our flour mixture through with an electrical charge,” said Dr Adam Clancy of UCL Chemistry. “It’s literally spaghetti but much smaller.”
In their paper, the researchers describe the next thinnest known pasta, called su filindeu (“threads of God”), which is made by hand by a pasta maker in the town of Nuoro, Sardinia. This long pasta is estimated at about 400 microns wide – 1,000 times thicker than the new electrospun creation, which at 372 nanometres is narrower than some wavelengths of light.
UCL’s 2cm mat of nanofibres is visible, but each individual strand is too narrow to be clearly captured by any form of visible light camera or microscope, so their widths have been measured with a scanning electron microscope.
“Starch is a promising material to use as it is abundant and renewable – it is the second largest source of biomass on Earth, behind cellulose – and it is also biodegradable, meaning it can be broken down in the body,” said Dr Clancy “But purifying starch requires lots of processing. We’ve shown that a simpler way to make nanofibres using flour is possible. The next step would be to investigate the properties of this product. We would want to know, for instance, how quickly it disintegrates, how it interacts with cells and if you could produce it at scale.”
Electrospinning using a starch-rich ingredient such as white flour is more challenging than using pure starch, as the impurities – the protein and cellulose – make the mixture more viscous and unable to form fibres.
The researchers used flour and formic acid rather than water, as the formic acid breaks up the giant stacks of helices that make up starch. This is because the layers of helices stuck together are too big to be the building blocks of nanofibres.
The formic acid then evaporates as the nanofibre is spun.
The researchers also had to carefully warm up the mixture for several hours before slowly cooling it back down to make sure it was the right consistency.
The work was performed by Beatrice Britton, who carried out the study as part of her master’s degree in chemistry at UCL.
“I really enjoyed the iterative process of adjusting the variables and observing how this changed the mixture,” she said. “It was a lot of trial and error – I didn’t think I would form fibres but I did.”
Business intelligence for the fibre, textiles and apparel industries: technologies, innovations, markets, investments, trade policy, sourcing, strategy...
Find out more