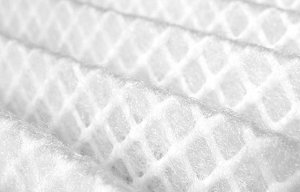
MNW appoints new Technical Sales Manager
When it comes to high performance textiles, filtration media often goes under the radar, says Arville's Andy Smith.
12th December 2017
Innovation in Textiles
|
Wetherby
With technical textiles innovation evolving apace, the sector’s headlines are often dominated with industry firsts, ranging from developments in smart wearables through to the cutting-edge fabrics that end up in space. But when it comes to high performance textiles, filtration media often goes under the radar.
Andy Smith from Arville, a leading technical textiles specialist, shined the spotlight on this commonly-overlooked area of technical textiles. “Rolls goods, sleeves, socks, bags, cloths and sheets, are just some of the various types of media that make up the large family of wet and dry filtration products,” he said. “These bespoke micron-rated fabrics can be designed to a specified particle size and flow-rate, giving customers exacting filtration materials across a wide arena of applications.”
The company is a specialist in providing a fully integrated solution for bespoke technical textiles used across a wide range of industries for wet and dry separation and filtration purposes, providing both roll-stock fabrics and pre-fabricated textile components.
“Each solution is engineered to meet the requirements of both everyday challenges, and sometimes very specific niches, which can often be very demanding in terms of chemical resistance, temperature resistance (hot and cold), high pressure and durability,” said Mr Smith. Versatility, consistent performance, effective particle retention and efficient flow rates, are just some of the capabilities achieved by technical textiles manufacturers who – by design – supply these engineered products for use in increasingly advanced production, separation and filtration processes globally.
“And the market is not standing still. As refinement processes become more complex and demanding, filtration media has to advance in parallel, in terms of everything from the fibres used, to the weave construction, and the consistency of the resulting filtration process itself. Performance criteria will only become more multifaceted over time, and that’s before any thought is given to sector-specific legislative frameworks that the filtration media has to work within,” Mr Smith explained.
“The regulations imposed by the FDA in the food and beverage industry, represents just one example where filtration textiles must meet specific criteria for critical applications where they come into direct food contact.”
“However, the innovative use of filtration textiles does not stop there. Such fabrics are also used in ‘heavy’ industries such as nuclear, mining and construction, as well as wider pharmaceutical scenarios which involve the separation of liquids, gases, powders and suspensions,” he added.
“But because synthetic man-made fibres are predominantly insulators which do not promote the flow of electricity through their structure, some of these processes can create a build-up of inherently hazardous static charge where there are combustible liquids or powders present. As such, anti-static properties must therefore be designed and manufactured within certain filtration media, to mitigate the risk of ignition.”
This typically sees such fabrics woven to include carbonised filaments or stainless steel, which allow the charge to disperse safely. It is also possible to manufacture the fabrics from yarns that are chemically inert to the process, and design weave patterns and constructions that allow for good cake release and efficient flow rates. An example is Arville’s development of a multi-pocket glatt bag, which was certified by the Food & Drug Administration (FDA) and used by GlaxoSmithKline.
Elsewhere, materials which are constructed from high-performance monofilament yarns are used to convey, filter and separate products in industrial, water purifying and waste processing facilities with varying degrees of permeability, giving them excellent drainage properties.
“These technical products represent just a handful of examples where the industry has stepped up to innovate products that fulfil a whole host of varying and conflicting criteria. But with performance demands evolving apace, the journey won’t stop there for filtration solutions. It’s therefore about time that they received a little bit of praise for the challenges they address within this complex ‘technical textiles’ arena,” concluded Mr Smith.
Further reading
Interview with Andy Smith, Group Head of Marketing at Arville
Business intelligence for the fibre, textiles and apparel industries: technologies, innovations, markets, investments, trade policy, sourcing, strategy...
Find out more