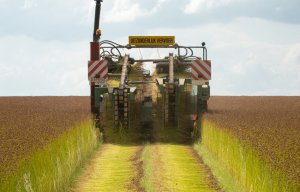
Europe’s flax harvest on track
Opinion
Bio-based resins and automotive industry validation are accelerating adoption.
13th March 2024
Adrian Wilson
|
Paris
A wide range of fabric reinforcement structures based on natural fibre composites (NFCs) was showcased at the JEC World composites show held in Paris from March 5-7.
Many were displayed within the very busy Natural Fibres Village by members of the Alliance of Flax-Linen and Hemp, formerly known as CELC, who continue to build momentum across a number of sectors, most notably in the automotive and transportation field.
‘‘JEC World 2024 saw European flax and hemp fibres taking a global step forward in advancing the bioeconomy of the engineering and composites sector,” said the Paris-based association’s innovation and CSR director Julie Pariset. “These natural fibres combine remarkable physical properties and eco-friendly characteristics, enabling the most innovative manufacturers in the composites industry to create massive reductions in their overall environmental impact.”
Drivers
Since composites generally comprise combinations of reinforcement fabrics and polymer resins, one key growth driver for natural fibre composites (NFCs) has been the development in recent years of resins that are also bio-based, enabling new products that are 100% derived from natural resources to be designed and fully realised.
A second major milestone was achieved during 2023 with the adoption – after many years of testing and validation – of Swiss company Bcomp’s ampliTex flax composites in dashboard and door trims within the first commercial passenger vehicle – the new Volvo EX30. This compact SUV is designed to have the lowest carbon footprint of any model in the history of Volvo.
French lead
Europe is the leading region for the production of flax, with 140,000 tons of long fibres that can be used in technical textiles and composites produced in 2023, across 150,000 cultivated hectares.
France, Belgium and the Netherlands account for three-quarters of total European production, with France the outright leader by far, producing 122,000 tons of long fibres across 131,000 hectares.
While flax fibres account for less than 0.5% of overall global textile fibre production, it is possible to obtain on average 900kg of fibres from a single hectare of land, equating to 3,750 square metres of fabrics, and the sustainable benefits of traceable European supply chains and their proximity to manufacturers is indisputable.
Other benefits of flax in cultivation are that no irrigation is required from sewing through to harvesting. The renewable resource also helps preserve soil quality, as a rotation crop which can increase the yield of other crops grown after it and requires minimal use of pesticides and fertilizers.
There are uses for all parts of the flax plant and fibre extraction via the scutching process is fully mechanical and solvent free.
Europe is meanwhile the second largest hemp producing region behind China.
Sherpa 4x4
NFCs also featured in what was one of the biggest and most attention grabbing exhibits at this year’s JEC World – the Sherpa 4x4 expedition vehicle which took centre stage at the Mobility Planet display area.
The Sherpa has been developed by partners Greenlander and Greenboats, both based in Bremen, Germany, and French flax material specialist Depestele.
Its construction is based on flax fibres and bio-based resins along with sustainable core materials such as cork, wood and recycled PET foam to create durable and lightweight components. In addition to low impact materials, Greenlander also provides a unique business model, offering the composite items as a service and taking them back at the end of their life to be repurposed or recycled.
Supply security
Groupe Depestele’s acquisition of a minority share in Greenboats is another significant development in the forward motion of NFCs.
It strengthens an existing collaboration and positions Greenboats as a forerunner in building the technology and infrastructure needed for NFCs to become a viable option to meet the industry’s growing demand for sustainable, lightweight components.
Managing 13,000 hectares of flax land in Normandy, the family-owned Groupe Depestele has been a key player in the flax industry, sourcing from more than 750 farmers across several regions and operating three scutching plants focused on the initial processing of flax fibres, and combing and manufacturing units.
The origin of the company’s products is ensured by the Alliance for European Flax-Linen and Hemp’s European Flax certification.
Pivotal juncture
Vehicle builders continue to evaluate both flax and hemp materials across their model ranges as they seek to reduce the overall environmental impact of their products. Natural fibres have been used for many years to reduce the carbon footprint in components such as acoustic insulation, headliners and interior mouldings that exploit the vibration damping and noise, vibration and harshness (NVH) benefits of these fibres. However, until recently applications have generally been parts that kept the fibres hidden, but flax is now being used in more visible parts as well as in significantly higher volumes.
“We’re at a pivotal juncture in the evolution of NFCs as a new product category,” says Jan Paul Schirmer, managing director of Greenboats. “Our clients believe in our technology but have demanded a more reliable and scalable supply chain. Our partnership with Groupe Depestele is based on respect and a mutual vision. Its investment is a strong vote of confidence in what we can achieve together and we couldn’t have hoped for a more fitting partner.”
With its background as a supplier to the Marine industry, Greenboats has expanded into many other end-use industries and is behind the Circular Structures B2B business for the off-the-shelf supply of NFC profiles made from flax rovings and plant-based resins. The combination of natural flax fibres and greener resins provides an optimised balance of lightness, stability and sustainability. In many cases, these composites are not just an ecological alternative to conventional materials, but also offer similar or even better mechanical properties than competing products.
Components
Bcomp also displayed a flax fibre seat back at JEC World for a second Swedish car manufacturer, Polestar, consisting of woven flax ampliTex fabrics, structured powerRibs reinforcement grids and nonwoven supporting layers. It will be supplied as standard in the latest Polestar 3 electric SUV.
EcoTechnilin, of Valliquerville, France, meanwhile showcased a range of flax nonwovens for automotive trim parts employed in both passenger and engine compartments, with its FibriPlast range of felts widely used in thermocompression processing and moulding.
Another French company, Saint-Pierre-le-viger-based Terre de Lin, also launched a range of coloured rovings for the automotive industry, suitable for weaving, knitting, braiding, pultrusion, filament winding and automatic fibre placement processes.
“Backed by scientific validation, our work confirms that flax and hemp solutions now meet and exceed the expectations of manufacturers for performance in the automotive sector,” said Julie Pariset in conclusion.
Business intelligence for the fibre, textiles and apparel industries: technologies, innovations, markets, investments, trade policy, sourcing, strategy...
Find out more