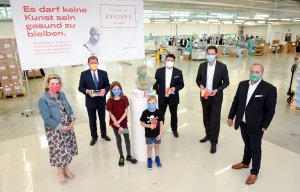
Back to school masks from Hygiene Austria
Live in less than a week with Gerber’s retooling solution and support.
12th June 2020
Innovation in Textiles
|
New York City
With help from Gerber Technology, FPS Apparel was able to quickly transition from producing promotional apparel to producing personal protective equipment (PPE) in just a week. FPS Apparel’s current production allows it to produce and donate 10,000 masks per week to various healthcare facilities and first responders.
As COVID-19 began to spread to New York City in early March, FPS Apparel knew it had to do its part to protect the health and safety of those fighting the pandemic on the frontlines.
“It’s a priority for all of us at Gerber to ensure our customers have everything they need to successfully transition to PPE,” said Pete Doscas, Vice President & General Manager, Americas Sales & Service Delivery of Gerber Technology. “With FPS Apparel being in the middle of an epicentre, we knew we had to help them, not only in regards to cutting equipment but through training and by connecting them with our other customers, which allowed them to get up and running as fast as possible so they could do their part to help stop the spread of COVID-19.”
In order for FPS Apparel to produce a large quantity of effective masks, they needed cutting equipment that would allow for fast, reliable and efficient quality cutting. Gerber was able to deliver and install a Gerber Paragon multi-ply cutter and AccuMark fashion design software in just a matter of days, allowing FPS Apparel to dramatically increase production. The cutter was able to seamlessly integrate with FPS’ microfactory setting, ensuring little disruption to its workflow. Gerber also provided FPS Apparel with production-ready patterns and expertise on PPE production.
“It was truly a team effort with Gerber,” said Dan Feinberg of FPS Apparel. “They delivered and installed the machine in less than a week while providing the support and training we needed to start production right away. They’ve also connected with several of their customers to find capacity for sewing and procurement.”
“By converting their production, FPS has not only saved thousands of lives but they’ve also helped save jobs. Rather than temporarily shutting down their production completely when COVID-19 reached New York City, they chose to keep their employees working by giving them the opportunity to use their skills to help keep those on the frontlines safe and healthy,” Gerber said.
“Located in the foothills of the Hudson Valley, their Chester, NY office is where the magic happens. They like to think of it as a 'microfactory' fit for small runs and sampling, with their bulk production happening in our other locations. The mission of FPS Apparel is to be a leader and trendsetter in customized apparel. With an innovative product line, cutting-edge software, and top-notch service, they strive to bring customers trendy clothing that can be customized in unique ways, at low minimums, with quick turnaround times.”
“Their customers represent some of the largest brands in America and beyond. From Fortune 500 companies to mom & pop retailers, they work solely with wholesalers and distributors, never direct. They proudly carry A+ / 5-star industry ratings through ASI & SAGE.”
Business intelligence for the fibre, textiles and apparel industries: technologies, innovations, markets, investments, trade policy, sourcing, strategy...
Find out more