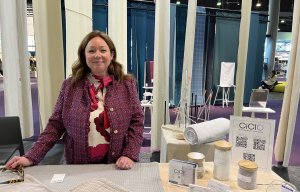
Microban and CiCLO join forces
Andrea Ferris, co-founder and CEO of Intrinsic Advanced Materials, the company behind CiCLO technology, talks to Innovation in Textiles editor Adrian Wilson.
29th January 2025
Innovation in Textiles
|
USA
Adrian Wilson: Maybe we should start by explaining what CiCLO is and what it does, for those who may be unaware of your technology?
Andrea Ferris: Sure. CiCLO enables polyester and nylon fibre-based textiles that would otherwise exist indefinitely to biodegrade at rates similar to natural fibres such as wool. It is patented and proven safe for use through Oeko-Tex Eco Passport certification, as well as rigorous third-party biodegradation studies conducted using internationally recognised ASTM and ISO test methods.
CiCLO is dosed into the fibres as they are being spun, and we offer formulations for both batch and continuous polymerization manufacturing processes for staple fibre and filament yarn.
Essentially it embeds active ingredients throughout the fibre that help enable biodegradation without any impact on the manufacturing process, or the performance of the final fabric. When the material is in the environment and exposed to moisture and microorganisms it can biodegrade just like natural products. CiCLO contains nutrients that microorganisms are attracted to and also creates more amorphous regions within the fibres, enabling the microorganisms to attack the material. CiCLO also makes the fibre more susceptible to attack by water which is important in breaking down bonds and ultimately allowing microorganisms like bacteria in the environment to fully biodegrade the material with no microplastics left over.
AW: Can you say a little about the background of CiCLO?
AF: I’m one of the co-founders of Intrinsic Advanced Materials which is the company that owns, manufactures and distributes CiCLO technology. It’s a joint venture partnership between a company that I helped found called Intrinsic Textiles Group – a textile technology start up – and Parkdale Mills, which is the largest spun yarns manufacturer and supplier in the Western Hemisphere.
We’ve been joint venture partners for six years, but the story predates that – we actually started developing CiCLO back in 2012. This was when I was working on managing a turnkey programme for the supplier of uniforms to McDonald’s, which as you can imagine is a huge programme. The McDonald’s uniform range is mostly polyester for all the practical reasons we use synthetic materials – it’s widely available, it’s affordable and high performing and has easy-care properties.
Even though we were using recycled polyester it was still polluting the environment, because once it winds up in the environment, however unintentionally, it is persistent just like other plastics.
Our initial aim was to make polyester durable but also biodegradable and what we were working on was for our own needs, which was incredibly helpful for our development process because we were already working with the material and knew what sort of boxes we needed to tick to bring a new technology into the textiles industry.
So that was our humble beginnings.
AW: How long was this initial development period?
AF: It took about four years in research and development and once we saw full biodegradation in third party lab studies the two owners of the uniforms company realised the potential of what we’d created. It was then that we decided another company should be set up to bring it to market as a textile technology.
AW: Leading to the formation of Intrinsic Advanced Materials?
AF: Exactly, so we have been in the market with the brand CiCLO since 2017. It takes a long time to bring a textile technology to market, because as you know, it’s a very complex and fragmented supply chain globally that we’re working with, but we are seeing tremendous success. Some of the larger corporations who have adopted our technology include Target, Hanes Brands – which does a lot of polycotton blends – and of course the McDonald’s uniform programme.
CiCLO is now being used in all kinds of apparel, anything that needs to be polyester or nylon – and then there are other non-apparel applications such as soft signage and flags which fray when they are out in the elements and are another source of microplastics, in addition to cleaning supplies products like microfibre floor pads and mops. The applications are really very broad.
AW: Are you dealing primarily with the brands or with fibre producers?
AF: We work throughout the supply chain but as our product is added at the fibre extrusion stage, business is directly between us and the major fibre manufacturers such as Unifi, Reliance and Indorama who are some of the many certified CiCLO manufacturers. We have legal agreements in place with them to participate in our traceability programme and they stand behind the quality of the fibre that they produce. It’s important we don’t just sell to anyone. We have to have a relationship in place.
We have about 50 certified manufacturers worldwide today and in terms of our business development and getting the buy-in for it, our sales team works with the brands and retailers to explain how the technology works and where CiCLO fibres can be purchased, because they have to make the final decision to spec the product. Many of the brands are purchasing from full-package providers so it’s important that our product is globally available, because brands frequently change their suppliers.
AW: How do you protect your technology?
AF: We have patents all around the world, in every major fibre producing country and we also protect our IP, the brand itself and its use through our business model of certified manufacturers. If somebody calls up tomorrow wanting to buy a container load, it’s not going to happen unless we already have a relationship with them. The traceability has been really incredibly important.
AW: It sounds to me like at some point in the future, the use of CiCLO should be made mandatory for polyester manufacturer.
AF: That would be really wonderful but specific material mandates are very difficult to enforce so I wouldn’t expect it to happen. There are, however, two pieces of upcoming legislation I think will be very important to us, as well, of course, to the environment.
The first is the pending intention to oblige companies operating in the EU to measure and report to consumers on the durability of their products. This is incredibly important because CiCLO has no impact on the durability.
Secondly, the extended producer responsibility (EPR) schemes that are being set up both in the EU and in California are likely to have eco-modulated fee structures, although we’re not sure yet how they will be implemented. They may incentivise the use of innovations such as CiCLO for addressing microplastics pollution. Its nominal additional cost may actually drive the eco modulation fees down, which will be a win-win for everybody.
Business intelligence for the fibre, textiles and apparel industries: technologies, innovations, markets, investments, trade policy, sourcing, strategy...
Find out more