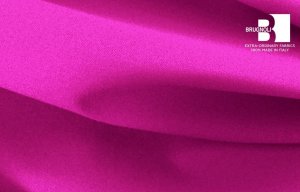
Q-Cycle showcase at Milano Unica
Yarns produced from waste car tyres in BASF’s mass balance process.
16th February 2022
Innovation in Textiles
|
Castel Goffredo (MN), Italy
Following the success of its Q-Nova recycled nylon, bio-based Evo nylon and biodegradable Amni Soul Eco nylon fibres, Italy’s Fulgar is widening its sustainable portfolio with the introduction of Q-Cycle yarn.
The ground-breaking new yarn’s development is the result of a project combining Fulgar’s textile expertise with the world’s largest chemical company, BASF, which has developed a new process called ChemCycling.
ChemCycling turns post-consumer plastic waste into pyrolysis oil, as a secondary raw material to replace the same amount of fossil-based raw materials at the beginning of the chemical production process. The share of chemically recycled material is allocated to the final product by using a third-party audited mass balance approach.
The technology can be applied to plastic waste that cannot be mechanically recycled for technological, economic or ecological reasons, as well as end of life tyres.
Fulgar has opted to use polymer produced from the recycled raw materials from old tyres, since these are usually incinerated, resulting in significant CO2 emissions. In Europe, for example, 1.37 million tons of tyres remain unrecycled every year.
Benefits
The production of Q-Nova offers a two-fold environmental benefit, making it possible to recycle post-consumer waste materials that would otherwise end up in landfill or be incinerated while also being self-sustaining, as the part of the waste that cannot be turned into raw material but is pyrolyzed into gas is used to generate the energy required for the process.
“We want to play a pioneering role in creating an increasingly circular economy for the textile supply chain,” said Fulgar’s head of marketing Daniela Antunes. “Our aim is to provide a measurable environmental contribution. Of course, this also involves cutting the quantity of fossil raw materials used, as well as reducing CO2 emissions and water consumption during production.”
Production is carried out in accordance with the EU methods ISO 14040 and ISO 14044.
Q-Cycle polyamide provides the same functional and aesthetic benefits of lightness, strength and resistance but in a more sustainable form. It can be used to produce high quality fabrics and be processed with ease like a normal polyamide, so it combines with all fibres.
Circular
“Collaborating with companies like Fulgar is the ideal way of constructing a model of a sustainable circular economy that also applies to plastic waste, which until now could not be recycled,” said Dominik Winter, vice president responsible for the European polyamides business of BASF. “The result of this synergy is a polyamide that can be used to manufacture high-quality fabrics, reducing the amount of fossil raw materials and providing individual brands with products with a reduced carbon footprint.”
Founded in Castel Goffredo in Italy’s hosiery region in the late 1970s, Fulgar is a leader in nylon 6.6 and covered elastomers for the textiles and technical fabric sectors and over the past ten years its investment in R&D has grown constantly. A commitment to environmental issues has been expressed through supply chain-wide projects such as Q-Nova regenerated yarn and bio-based Evo yarn, in partnership with Evonik.
Fulgar is also the exclusive distributor in Europe and Turkey of the Lycra, Lycra T400 and Elastan fibre brands and in 2012 forged a partnership with the Solvay group, becoming the distributor and producer of Emana fibre and Amni Soul Eco mainly for Europe, North Africa and the Middle East. The cooperation with BASF for the production of Q-Cycle recycled yarn started in 2021.
Business intelligence for the fibre, textiles and apparel industries: technologies, innovations, markets, investments, trade policy, sourcing, strategy...
Find out more