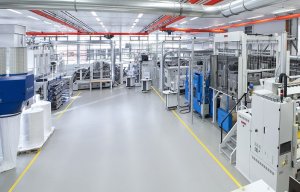
Groz-Beckert at IDEA 2022
Most nonwovens lines of Groz-Beckert customers in the USA work to capacity or beyond, with only little time considered for service.
9th August 2018
Innovation in Textiles
|
Albstadt
“This is where the Groz-Beckert Service Team comes into play,” the company says. “Both the short staple spinning and the nonwovens industries put high requirements on mounting service. Compared to the service provided to the spinning industry, service is even more important in the production of nonwovens.”
“While in spinning there are typically several revolving flat cards installed, large nonwovens lines normally feature only one roller top card. If this fails due to damage, also called crash, the entire line stands still. This is why an immediate response and quick restart of the nonwovens line are critical.”
Only a small share of annual service jobs and maintenance work is scheduled beforehand by carding customers in the US. In these cases, service engineer resources and material can be planned ahead of time. The greater part of service jobs, however, is based on crashes. In such cases advance planning is not possible, and the Service Team gets the relevant information through the 24-hours service hotline.
In a first step it must them be clarified what card section and card clothing was damaged and what jobs must be done by the service engineer. The service could range from the disassembly of the card to the stripping of old wires and mounting of new wires to the assembly and restart of the card.
At the same time, the local Service Team prepares for the service job. To guarantee a quick response to crashes, Groz-Beckert holds available several service engineers, service vehicles and mounting equipment. To guarantee a quick arrival at the customer's, the Groz-Beckert service engineers are located in strategically important parts of the USA.
Wire specification for the customer's card is based on the Groz-Beckert specification sheet, listing the relevant rolls and the required wire. Sufficient stocks allow the service engineer to take the material along or have it sent to the customer immediately.
For a typical service job, whether planned or in case of a crash, the customer will usually request several engineers. This allows the carding customer to minimize downtime and the service technicians to work efficiently.
Service engineers complete a special training program for the first 3 to 5 years so that they are able to take fast and confident action in any situation. The programme starts with training in the service workshop where fundamental knowledge regarding card wires, the mounting of wire and Groz-Beckert safety standards is taught. After the basic training, fitters then assist experienced colleagues during service jobs at customer facilities to deepen their carding knowledge. At the same time their awareness for safety and handling high quality products is raised.
“The majority of our US-American carding customers are in the nonwovens industry; for them, the Groz-Beckert service is essential. Moreover, the Groz-Beckert service is distinguished by constant availability of service engineers and fast response times with immediate availability and delivery of products, as well as fast and efficient mounting of wires and restart of the card,” the company adds.
“This is why the Groz-Beckert mounting service has proved successful in the USA and is firmly established in the carding market.”
Business intelligence for the fibre, textiles and apparel industries: technologies, innovations, markets, investments, trade policy, sourcing, strategy...
Find out more