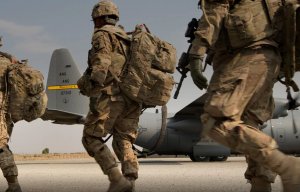
Comprehensive Cordura at Enforce Tac
Continuous wear can potentially have a detrimental impact on the performance of unprotected composites.
13th April 2021
Innovation in Textiles
|
Kendal, United Kingdom
Technical Fibre Products (TFP), based in Kendal, UK, has carried out a study to prove the effectiveness of aramid nonwoven surface veils in protecting the underlying structural elements of composites from the effects of abrasion and wear.
The lightweight aramid veils enable a high-quality surface finish, while simultaneously providing a durable and sacrificial layer in applications such as high-speed composite rollers, automotive friction substrates or sporting goods where the composite experiences a constant friction. This continuous wear can potentially have a detrimental impact on the performance of the composite, as well as significantly reducing it lifespan.
The study carried out examined the effectiveness of using a surfacing veil to increase wear resistance by comparing composite panels fabricated both with and without TFP’s aramid veils.
The panels, based on epoxy resin and woven carbon, were tested using a pin-on-disk tribometer to measure friction and wear as a function of time. The data generated demonstrated that the measured coefficient of friction is significantly lower when an aramid surfacing veil is used, taking at least five times as long to reach the level measured in the control.
Essentially, this indicates that the level of friction experienced by the composite surface is significantly lower and less material is worn away as a result.
This finding is reinforced by microscope imaging of the samples showing just damage (and no breakage) to the surface fibres, and no damage to or exposure of the woven reinforcement in the composite panels containing the aramid surface veil.
This can be compared to evidence of significant fibre breakage and damage to the underlying carbon weave in the control panel. The findings demonstrate the importance of the aramid veil in acting as a sacrificial layer to protect the underlying reinforcement, ultimately increasing durability of the composite structure and extending its lifespan. More information on the study (including data and images) can be found on the TFP website here.
TFP’s nonwovens can be used to confer a wide range of functionalities to a composite, not just abrasion resistance, including conductivity or EMI shielding (using metal coated veils), corrosion resistance (glass or carbon) and even fire protection (with Tecnofire). The veils have been designed to ensure uniform resin uptake, eliminate dry spots, minimise print through and fibre breakout and ultimately deliver a high-quality surface finish.
Business intelligence for the fibre, textiles and apparel industries: technologies, innovations, markets, investments, trade policy, sourcing, strategy...
Find out more