ATEX expands meltblown capacity
Nonwovens/Converting
The ICE won’t melt overnight...
Nonwovens have a significant role to play in the fast-accelerating transition to electric vehicles.
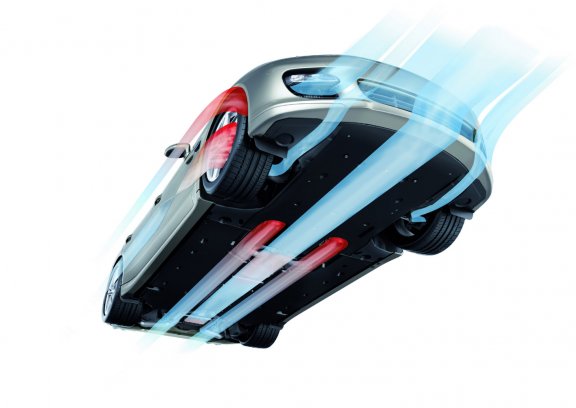
26th September 2022
Innovation in Textiles
|
Geneva, Switzerland
In the build-up to the INDEX 2023 exhibition which takes place from April 18-23 next year, show organisers EDANA and Geneva Palexpo are emphasing how nonwovens have expanded rapidly in the automotive industry over the past two decades, as automakers and their component suppliers have looked to decrease costs by reducing the weight of vehicles.
The aim, it is explained in the show’s latest newsletter, has been to lower fuel consumption and carbon CO2 emissions and comply with new legislation.
The use of nonwoven fabrics in the European automotive industry alone grew by 11.3% per year between 2010 and 2015, despite the fact that the production of cars and light vehicles grew by only an average 1.3% annually in the same years.
This underlines just how much nonwovens have already been included in the lightweighting designs of vehicle manufacturers and reveals that a good deal of material substitution has already taken place in conventional internal combustion engine (ICE) vehicles.
Nonwovens do, however, have an equally significant role to play in the fast-accelerating transition to electric vehicles (EVs) and alternative methods of propulsion.
Insulation
A big application for nonwovens in ICE vehicles is still in insulating materials for absorbing the noise of the engine and dampening the vibrations caused by it. Many of these are superfluous in EVs, but at the same time, other noises are helpfully masked by an engine.
As a result, sound reduction becomes even more critical for EVs because external as well as internal sources such as fans, pumps and electronic drive components are more audible. There are additional thermal challenges too – without waste heat from the engine, the passenger cabin of an electric vehicle can be significantly chillier than that of a conventional vehicle, which calls for different insulating solutions.
Undercovers
Over the past twenty years, the replacement of hard plastic or metal components has already made a significant contribution to the overall nonwoven content of vehicles. While for many years, densely-needled nonwoven layers were used as acoustic insulation components for the interior of vehicles, they have increasingly been employed for the exterior – as undershields and outer wheel arch liners. Nonwoven undershields as replacements for the heavy PVC layers that were previously applied to the rear of the floor panel have provided a considerable reduction in weight at a comparable price.
In a logical extension of such components, nonwoven battery undercovers that optimally meet the specific requirements for the acoustic and thermal management of electric vehicle battery housings are another growing application. The nonwoven solutions for this application are 50% lighter than components made of plastic, with a high degree of shock resistance and protection against stone chips. In addition, they are water and heat resistant and reduce vehicle noise by up to two decibels, while reducing drag. This reduces fuel consumption to generate less COâ‚‚ emissions.
These components also act as insulators, helping to lower sound that enters the passenger cabin caused by tyres and pass-by noise.
Clean and efficient
According to a recent report by Greenpeace, there are two main reasons why electric cars are so much better for the environment than petrol or diesel.
The first is that electricity is getting cleaner all the time and while conventional cars will always need fossil fuels, electric vehicles can – and increasingly do – run on renewable energy. The carbon footprint of electricity is falling fast and every year this trend continues, EVs increase their advantage – as the electricity grid gets cleaner, the carbon impact of manufacturing falls for all new cars, but once they’re actually on the road, powering a petrol car is as polluting as ever.
Secondly, electric motors are much more efficient than conventional engines. Despite more than 100 years of refinements, the ICE in a car just isn’t that good at converting fuel into movement. Even in the most efficient ICE, only around 12-30% of the energy in the fuel ever makes it to the wheels or other useful functions. The rest is wasted as noise and heat.
Electric motors, by contrast, are around 77% efficient, and get many more miles out of the same amount of energy.
Fine dust
There are however, still problems with electric cars and their contribution to air pollution in cities is a major one, with emissions generated as much by tyres and brakes as comes from exhaust pipes.
As a result, fine dust particle filter media for electric vehicles are already promising to become a major new market application for nonwovens.
Braking in city traffic creates significantly more dust than exhaust emissions – every braking action creates dust through friction on the disc and pads. This mainly comprises particulates, more than 90% of which are ultra-fine, and therefore harmful to both health and the environment.
Filters can reduce a vehicle’s particulate emissions by more than 50% and their efficiency increases further when there is a higher level of particle pollution. This means that in urban areas with poorer air quality, far greater quantities of fine particles can be filtered out.
Batteries
There are also problems with some of the materials that make up today’s batteries.
A number of nonwovens companies are now manufacturing battery separators for EVs in what is already a significant market.
Typical hybrid vehicles contain 50-70 lithium-ion (li-ion) batteries, full EVs carry 150 or more, and plug-in EVs with range-extending motors can contain more than 200.
Within each battery, the separator is a sheet positioned between the two electrodes. It functions as a barrier that prevents the electrodes from touching and shorting while letting li-ions pass back and forth to allow the charge and discharge of the battery.
A new kind of galvanic nonwoven to protect the components of EVs from disruptions caused by electromagnetic waves is a recently-developed solution. So far, aluminium has been the tried-and-tested material for this application, but a high proportion of aluminium in EVs can impair driving dynamics and vehicle range, and costs also rise because the tools used to produce the aluminium housings have limited durability. Galvanic nonwovens offer a cost-effective alternative.
A number of INDEX23 exhibitors also belong to the Soteria Battery Innovation Group, a supply-chain-wide consortium founded to promote light, safe and cost-effective architecture for li-ion batteries. Soteria’s separator and current collector technology helps prevent internal cell short circuits from escalating into thermal runaways and employs nonwoven battery separators which combine microfibres and nanofibres in a porous substrate.
As all of these developments continue to make progress, INDEX23 will reflect a nonwovens industry firmly committed to the future of automotive.

Business intelligence for the fibre, textiles and apparel industries: technologies, innovations, markets, investments, trade policy, sourcing, strategy...
Find out more