Strong German participation at Irantex
Opinion
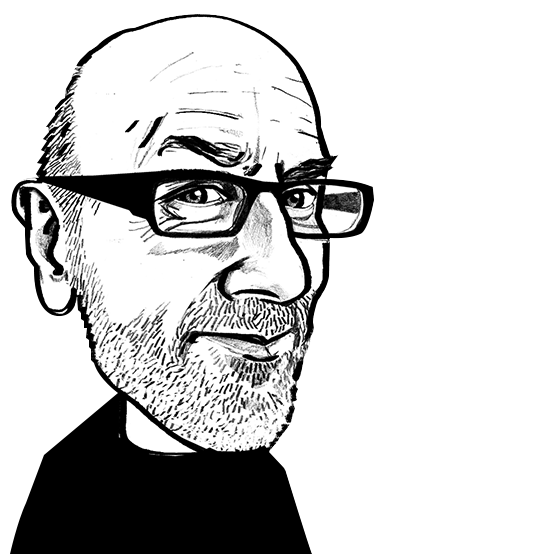
VDMA: Next stop Techtextil
Adrian Wilson
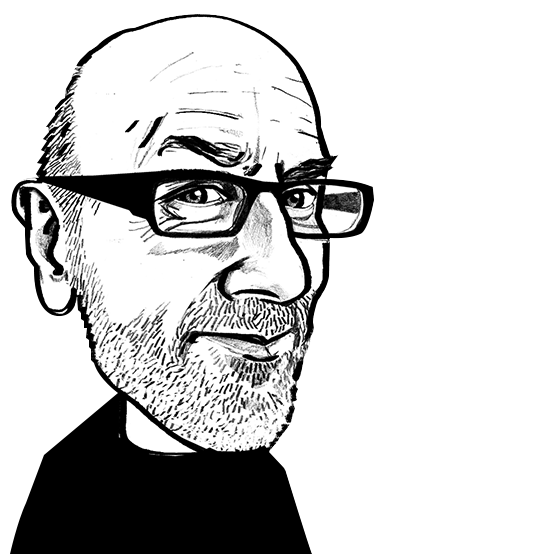
Focus on sustainable technologies for technical textiles from more than 40 member companies.
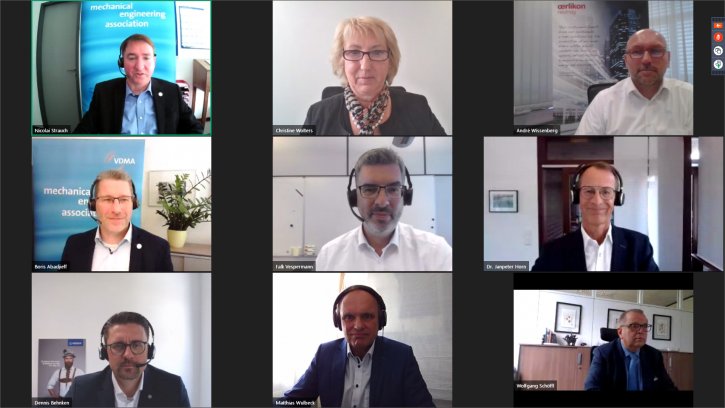
6th May 2022
Adrian Wilson
|
Frankfurt, Germany
In the run-up to Techtextil, taking place from June 21-24 in Frankfurt, nine exhibiting VDMA textile machinery division member companies presented their highlights for the technical textiles market, with an emphasis on sustainable production, in a special webinar held earlier this week (May 2nd).
“This year’s Techtextil is the first important exhibition and get-together for the textile industry in Europe since 2019,” said Dr Janpeter Horn, chairman of the VDMA textile machinery association and managing director of braiding machinery specialist Herzog. “The industry is currently faced with tremendous challenges in terms of the supply chain and logistics and there will be some reshoring as a result. Techtextil is a great place for us to discuss these issues, since we are very much part of the close textile chain that also includes researchers and the textile manufacturers themselves.”
More than 40 VDMA member companies will exhibit in Frankfurt, and the organisation will also have a group stand in Hall 12, underlining the importance of the fair. The companies taking part in the webinar represented the broad spectrum of process steps in technical textile manufacturing, beginning with filament and fibre spinning.
Fibres
André Wissenberg of Oerlikon said his company would introduce a unique 16-end system for the production of high tenacity PET and polyamide yarns.
“Two-end is antique, four-end is old-school and eight-end was yesterday, 16-end is now,” he said. “With the highest efficiency and best quality, production efficiencies such as more than 98% full bobbin rates, as well as up to 72 hours without a single break are achievable.”
The company will also show its latest hycuTec hydro-charging solution for meltblown nonwoven lines which can reduce the pressure loss in typical FFP2 filter media to less than a quarter. Filtration efficiencies of more than 99.99% are easily achievable in typical filter media of 35gsm at 35 Pa.
“Tests at pilot customers manufacturing FFP2 face masks have confirmed quality increases due to the improved filtration with a simultaneous reduction in material usage of 30%,” Wissenberg said. “For end users, the result is reduced breathing resistance for improved comfort.”
With its MultiMode system of intelligent modules that can be easily exchanged and rearranged, Dienes plants meanwhile offer maximum process flexibility to manufacturers of fibres, including precursor yarns for carbon fibres, recycled and biobased materials and textile filament yarns.
“We support our customers in their work from the first laboratory tests to the modular construction of their production lines,” said the company’s José Canga Rodriguez. “The development of sustainable technical textiles demands an efficient systematic and, in part, self-optimising working system.”
Braiding
Herzog will introduce a new core-cover braiding technology integrated with a heat-setting device in Frankfurt.
“With a durable design and energy-efficient motors we supply our customers with sustainable braiding machines,” said the company’s sales manager Dennis Behnken. “Even recycled yarns can be processed without compromising machine speed or product quality.”
The company’s braiding technologies are widely employed in the creation of near-net shape carbon fibre composite preforms – 3D textile structures as close to the shape of the final finished component as possible – with key customers in the automotive industry including BMW, Mercedes and Porsche. Suppliers to Airbus and Boeing are likewise Herzog partners for aerospace components.
Centrifugal forces
Braiding is a two-step process exploiting centrifugal forces to create structures with unique characteristics, which can have high flexibility and high torsion stability under load. The fibres are secured by interlocking with equal load division throughout the length of the product in both biaxial and triaxial configurations. There are many markets for these braided products and Herzog has delivered more than 550 types of customised machine to over 60 companies.
In addition to composite preforms, two other key growth areas for braided textiles are ropes and medical products.
The ability to replace steel with high strength fibres such as aramids, Dyneema and Vectran has resulted in ropes that have 75% less weight with all of the advantages that brings in terms of towing, mooring, anchoring and lifting and lowering. In addition, ropes made from these fibres have ten times the working life of steel equivalents.
In medical products such as sutures, artificial ligaments and stents, braided fabrics are increasingly the preferred choice for their flexibility in terms of the customised shapes and patterns that can be achieved and the specialised fibres that can be accommodated.
Data
Companies who already know about machines and processes should use the data they have to better use, was the message of Falk Vespermann of Lenze.
“Our goal is to assist companies in improved web and yarn handling, especially since the exploitation of smart data can result in more sustainable production,” he said. “The data is already there in servo drives, gear sets and belt drives. Using it is more important than ever in the EU, which will soon be demanding digital passports for products.
“The smart way to ensure more sustainability and greater transparency is to look directly into the machine with the drives as sensors. This, coupled with the domain expertise to draw the right conclusions from the data obtained, leads to less waste, higher machine availability and improved processes.”
Knitting
Christine Wolters of Karl Mayer said that at Techtextil 2022 her company will present technological solutions for integrated and optimised processes that reduce resource consumption, energy use and waste within the textile value chain.
“Examples include the application of 3D-printed reinforcement structures on textiles and the incorporation of electronics for the production of wearables directly on warp knitting machines,” she explained. “In addition, sustainable alternatives for conventional textile products will be shown, including 4D-Knit – a clothing solution for less microplastic pollution – and composites made from flax, as a renewable raw material.”
For 25 years, Ontec has been offering sustainable solutions to the textile industry including coating, winding, automated creel feeding and laid scrim production, as well as robotics and automation,
“Our SPSCOMM is an Industry 4.0 universal interface for smart production,” said sales manager Andreas Mondry.
Weaving
Lindauer Dornier weaving machines cover the entire spectrum of fabric production, from very fine to very coarse fabrics.
An emphasis at Techtextil will be on the weaving of filter fabrics.
“No matter whether water, air, blood or gases are to be filtered, the demand for high-quality filter fabrics is growing worldwide,” said the company’s head of weaving machines Wolfgang Schöffl. “Among other things, this is due to stricter environmental and sustainability requirements, which demand ever more comprehensive performance parameters. In order to continuously improve the tightness and quality of filter fabrics, we are further developing our machines, in close cooperation with our customers.”
Finishing
Baldwin Technology is looking to eliminate chemical waste and reduce energy consumption in textile finishing.
“Traditional textile finishing by padding is a wasteful, antiquated process,” said the company’s global leader of engineering and R&D, Wesley Clements. “High pick-ups drive high energy consumption and frequent bath changes generate a lot of avoidable chemical waste. There is a solution, and brands and mills are starting to see the light with the help of Baldwin’s non-contact precision spray systems. These systems increase product quality, improve mill profitability and deliver quantifiable sustainability benefits.”
In addition, he added, they provide traceability via OPC (open platforms connectivity) to a mill’s ERP (enterprise resource planning) system.
Online control
Against the backdrop of current events in Europe and the extreme rise in energy prices, online quality control in production processes in nonwovens and textile production is more important than ever before, said Matthias Wulbeck of Mahlo
His colleague Stephan Kehry added: “Faulty production, be it, for example, due to too large or too small an application quantity during coating, have an even greater impact and cause sensitive losses for the manufacturer. For more than 75 years, Mahlo has been supplying optimum solutions for quality control and energy saving, which is reflected in very short payback times and corresponding profit optimisation.”
A series of new VDMA textile machinery webtalks will be launched in the run-up to the exhibition.
The full programme can be accessed at:

Business intelligence for the fibre, textiles and apparel industries: technologies, innovations, markets, investments, trade policy, sourcing, strategy...
Find out more