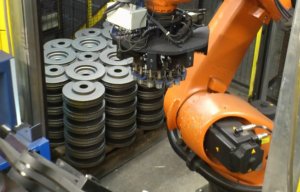
Loop Technology joins NCC as new Associate Member
Flexible and dynamic software-based infrastructure will free gr3n plant from fixed function devices.
8th July 2024
Innovation in Textiles
|
Cologne, Germany
The new PET polyester recycling plant to be constructed by gr3n and Intecsa Industrial in Spain will benefit from the latest Open Automation developments of Schneider Electric.
Speaking at the recent 5th Go Circular conference held in Cologne, Germany, from April 16-17, Fabio Silvestri, head of marketing for gr3n and Delphine Largeteau, Schneider Electric’s consulting director for sustainability, outlined the goals of the ambitious project.
Gr3n, based in Lugano, Switzerland, has developed an economical depolymerisation process it calls MADE, for breaking down PET into its chemical buiding blocks – TPA and MEG – via the application of microwave technology to alkaline hydrolysis. It is intended for textile and plastic feedstocks that are hard to recycle mechanically and the reclaimed TPA and MEG monomers can be used in any standard polycondensation plant. The reclaimed PET pellets can further be used for producing new packaging or fibres, regardless of the feedstocks from which they were obtained. The monomers can theoretically be reclaimed endlessly.
“Our process effectively erases the memory of the monomers,” said Silvestri.
At pilot scale, gr3n has already worked with Italy’s Alcantara to successfully break down and recycle its luxury suede fabrics based on 70% PET and 30% polyurethane (PU) and has also turned its recycled PET into POY and DTY yarns that have subsequently been woven into textiles.
Industrial scale
In July 2023, gr3n announced a joint venture with Madrid-headquartered engineering contractor Intecsa Industrial, to build a MADE plant with an annual capacity of 40,000 tons, to become operational in December 2027.
The full investment of the project is put at €200 million and Delphine Largeteau explained how it will benefit from the Open Automation developments of Schneider Electric, the multinational company specialising in digital automation and energy management, headquartered in Rueil-Malmaison, France.
For the past 50 years, Largeteau explained at Go Circular, automation systems have been locked, proprietary and driven by hardware, making them difficult to integrate with new IT applications.
“This makes them hard to change and demands a lot of labour-intensive coding and engineering,” she said. “We are developing an Open Automation system that is vendor agnostic, decoupling hardware from control application software with a plug and play approach that is easy to scale and modify. It’s about closing the digital loop and our technology is completely applicable to other applications, with a lot of promise in the automated sorting of textile waste, for example. At present there are a lot of machines out there that are not really talking to each other.”
Software-defined plants
In February this year, Schneider Electric announced the release of its new Distributed Control Node (DCN) software framework, developed in collaboration with the technology companies Intel and Red Hat.
An extension of Schneider’s EcoStruxure Automation Expert, the new framework enables industrial companies to move to a software-defined, plug-and-produce solution, allowing them to enhance operations, ensure quality, reduce complexity and optimise costs.
It is aligned with the goals of the Open Process Automation Forum (OPAF), which is dedicated to driving the interoperability and portability that will lead the way to the next generation of industrial control, providing companies with the freedom of shaping technology around their business needs – and not the other way around.
DCNs are low-power, industrial systems using Intel Atom x6400E series processors, dedicated to running controls and designed for workloads of mixed-criticality.
“Open and interconnected commercial solutions will help usher in the transition from fixed function proprietary devices to flexible and dynamic software-based infrastructures,” said Christine Boles, vice president of Intel’s Network and Edge Group.
The 6th Go Circular conference will take place in Rotterdam, Netherlands, from March 4-6 2025.
Business intelligence for the fibre, textiles and apparel industries: technologies, innovations, markets, investments, trade policy, sourcing, strategy...
Find out more