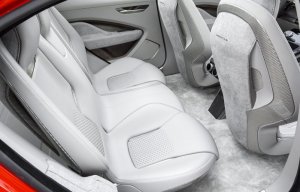
Hypetex adds bespoke carbon to the Jaguar I-PACE
Natural fibres, fibre composites, leather alternatives and algae-based polymers contribute to a 90% CO2 footprint.
7th August 2024
Innovation in Textiles
|
Michigan, USA
At a recent ceremony in Michigan, BMW Group received the Enlighten Award in the Sustainable Process category from Altair, for its development of the BMW M Visionary Materials seat.
BMW Designworks was responsible for the design, colour and material concept of the seat, which was developed in close cooperation with partners Automotive Management Consulting, Bcomp, Gradel Lightweight and Lasso.
The seat takes the use of plant-based materials to a new level, raising the share of secondary raw materials and increasing the potential for recyclability at the end of its lifecycle.
Its minimalist design leaves the lightweight seat structure visible, highlighting its status as a core component. Intensive lifecycle assessments (LCA) complemented the design at each stage of development.
“We are showing today what will be possible tomorrow with existing technologies and materials, in order to take our efforts to reduce emissions and conserve resources to the next level,” said Falco Hollmann, innovation manager at BMW M. “This is about more than just substituting materials, it is above all about designing for circularity.”
The evaluation of available material classes with a high SQR (secondary raw material quota) showed that natural materials are the ideal complement. The seat features natural fibres, fibre composites, leather alternatives and algae-based polymers.
Its CO2 footprint is 90% lower than a BMW M carbon bucket seat made today, thanks to the use of ultra-light, robotically-wound fibre composite seat support structures and materials of natural origin. In addition, lower module complexity and the use of materials grouped by type make it easier to recycle at the end of its lifecycle.
The additive manufacturing processes used are also groundbreaking. A new technology made it possible to completely eliminate support structures, chemical post-treatments and finishing in the production of the seat.
Other priorities included a flat value creation chain and a minimum of finishing steps to save energy and conserve resources.
“One of our biggest lessons was the balancing – how to model our process chain to generate missing primary data,” explained Roberto Rossetti, head of development for total vehicle-lifecycle at the BMW Group. “The data obtained provides new insights, both in terms of today’s negative contributing factors and the design of tomorrow’s processes. This provides a solid foundation for continuously improving sustainability and developing new solutions for forward-thinking mobility.”
Business intelligence for the fibre, textiles and apparel industries: technologies, innovations, markets, investments, trade policy, sourcing, strategy...
Find out more