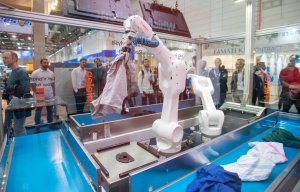
Texcare bounces back after eight years
Exhibition will showcase concepts that optimise the use of resources and reduce carbon emissions.
27th June 2024
Innovation in Textiles
|
Frankfurt, Germany
In the commercial textile-care sector, soaring energy costs are resulting in new solutions for lowering consumption, reducing emissions and in many cases extending textile durability.
At Texcare International 2024 in Frankfurt from November 6-9, a significant number of manufacturers will be presenting technologies to help dry cleaners and laundries increase their resource efficiency.
Currently, energy accounts for around 15% of total costs for commercial laundries, with process heat making up the lion’s share. As a result machine and equipment manufacturers are working on concepts that optimise the use of resources and reduce carbon emissions through modern washing methods, the recycling of water and energy and the use of renewable sources for heat generation.
Water the key
Recycling process water is nothing new in the laundry business, but concepts for recycling pressing water, filtered rinsing and process water and the use of cooling water from the dry-cleaning machine, for transferring articles to the wet cleaning machine, are constantly being improved. In addition, the modern technologies installed in laundry machines such as weighing cells or low-level sensors adjust the resources used to the actual load weight, to contribute to a reduction in costs.
Energy consumption
Manufacturers of laundry and dry-cleaning machines, as well as finishing appliances, focus on technologies with an optimum efficiency classification. Such machines ensure the best possible water extraction and low residual moisture in the laundry so articles can be dried quickly and efficiently. Plant manufacturers use new materials such as ceramics and carbon steel to reduce ironer gas consumption and also exploit heat-pump technology and generate hot water by solar energy. Modern machines are also equipped with special coatings that stop dry, energy-absorbing fluff from adhering to surfaces. New technologies improve evaporation performance thanks to direct heat transfer in a heated trough or improve solvent distillation by preventing boil-over, measuring turbidity or filtration.
Increasingly, the energy contained in vapour is also being harnessed – technologies such as low-pressure vapour recovery systems recycle energy from steam to generate process heat. Special collectors store excess heat and make it available again when needed. In addition, the energy trapped in exhaust air or wastewater is being recovered using special heat exchangers before being fed back into the production process, either as preheated fresh water or fresh air.
System as a whole
Reducing the resources consumed by a textile care business cannot be achieved by implementing isolated measures, but only as part of an overall system in which all processes are intertwined. Waiting times at machines, idle times and poor occupancy rates all result in unnecessary energy losses. In an energy-optimised laundry, however, every item is in the right place at the right time. Additionally, management information systems make it possible to precisely analyse energy consumption in all parts of the laundry and provide a solid basis for modifying processes or making investment decisions.
Detergents and processes
The detergent industry also uses processes and products to promote the optimal utilisation of resources in laundries. Low-temperature disinfection processes, which achieve a listing with the Robert Koch Institute (RKI) and the Association for Applied Hygiene (VAH) at 40°C, can significantly reduce the cost of process heat. A new benchmark has however been established at 50°C for disinfection washing, because although energy consumption increases with this process, the quantities of detergents and washing auxiliaries used are reduced and the lifespan of the items increases.
Customised, highly concentrated detergents or washing substances which are tailored to the material, stains and hygiene requirements of the customer in a modular system, lead to optimum stain removal, reduce the post-wash proportion and lower the energy input per item of laundry.
New options
Events of recent years have underscored the dependence of energy prices on geopolitical factors and political decisions.
As a consequence, supply-side developments in Germany and across Europe are difficult to predict, which is why the choice of the best source of energy will in future be much more dependent on local and structural conditions.
“In some regions, hydrogen will be available, while in other regions wood pellets may play a more important role than in the past,” says Andreas Langer of leading laundry technologies manufacturer Kannegiesser. “Companies will then use these methods to heat steam boilers or generate electricity, for example, to heat thermal oil as a source of energy.”
In Germany, the focus is likely to shift more towards renewable energy sources, such as solar or wind energy.
“Long-term investments in sustainable energy generation can lead to a gradual relaxation in the market, as gas is increasingly replaced by electricity,” says Alexander Seitz CEO at laundry services specialist Seitz. “However, prices are likely to remain high for the time being, following the energy transition and the imposition of an energy levy.”
Dirk Freitag CEO of Multimatic, another manufacturer of laundry machinery, sees the switch to alternative energies as an opportunity for the industry
“They are already by far the cheapest form of energy generation and we firmly believe that, within ten-to-fifteen years, Germany will be able to generate, store and transport sufficient electricity autonomously for stationary energy consumers over long distances,” he says. “Accordingly, we are already prepared for the switch from gas to electricity for all of our products.”
Despite all the speculation about future market developments, Thomas Zeck, sales manager for textile care chemicals manufacturer Chemische Fabrik Kreussler, emphasises that energy costs will remain high.
“As a consequence, the energy consumption of laundry and cleaning processes must continue to fall.”
Business intelligence for the fibre, textiles and apparel industries: technologies, innovations, markets, investments, trade policy, sourcing, strategy...
Find out more