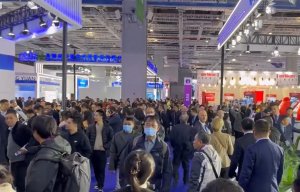
VDMA emphasis on resource savings in Shanghai
In the run-up to ITMA Asia + CITME, Nicolai Strauch spoke to VDMA member companies about their role in developing and realising sustainable solutions.
5th October 2016
Innovation in Textiles
|
Frankfurt/Shanghai
Volatile prices for energy and commodities, requirements from brands, retailers and end consumers, as well as government regulations have made sustainability a major challenge for the textile industry. For these reasons, resource efficiency is one of the premium targets of technical developments. The increased responsibility for work safety and workplace design is also an aspect of sustainability to which textile companies pay more and more attention.
In the run-up to ITMA Asia + CITME 2016, taking place later this month in Shanghai, Mr Nicolai Strauch, Press Officer, VDMA Textile Machinery, spoke to VDMA member companies exhibiting at the show about their role in developing and realising sustainable solutions from fibre to the final textile product.
VDMA represents over 3,100 mostly medium-sized companies in the capital goods industry, making it the largest industry association in Europe. Almost 100 German exhibitors will be present at ITMA Asia + CITME in Shanghai. They cover nearly all different machinery chapters with a focus on spinning, nonwoven, weaving, knitting, warp knitting and finishing.
Taking part in the conversation were Hermann Selker, Head of Marketing, Trützschler; Dr Martin Folini, CEO of Saurer Group and Schlafhorst Zinser Business Unit; Benjamin Mayer, Managing Director, Mayer & Cie.; Hans Gerhard Wroblowski, Area Sales Director South East Asia and Head of Denim Technology, A. Monforts Textilmaschinen; and Karl Hesse, Senior Sales Engineer, Körting Hannover.
Herman Selker: Absolutely. And that’s why fibres should be part of the yarn, not of the waste. Raw material savings are the best opportunity to realise cost savings.
Selker: Our tool called Wastecontrol improves the economic efficiency of the blow room by raw material savings. The idea behind it: the cleaner shall obtain the best possible degree of cleaning without separating many good fibres. This requires that the setting of the cleaning elements is exactly adapted to the raw material.
Selker: Wastecontrol is an optical sensor that determines the composition of the waste. The sensor detects how many fibres and how many trash particles are contained in the waste. The measuring process starts with closed cleaning elements. After that, the deflector blades of these elements are slowly opened. In the process, the separation of trash particles increases. Starting from a certain point, too many good fibres are extracted. Thus, it is obvious that the optimum working point for this raw material and for this cleaning element is just before that point.
Selker: Our experience shows that it is easy to save 0.5% or even more waste in the blowroom when using the system. As a consequence, a spinning mill using e.g. 10,000 t cotton per year can save between US$ 62,000 and US$ 90,000 of raw material per year.
Martin Folini: These are the guiding principles that define the design of every new produced Saurer machine and ensure that it will meet the challenges of the future. Firstly, energy is a huge topic, which will only loom larger in future. Every new machine we bring onto the market is more energy efficient than its predecessor. Secondly, economy represents increased productivity of the manufacturing process, which is the most important consideration in the customer‘s purchasing decisions. And finally, ergonomics: optimising operating conditions of a machine and time needed for settings and adjustments.
Folini: A prominent example is our latest automatic rotor spinning machine. The machine’s individual spinning drive position cuts the energy consumption of rotor spinning mills by nearly 30% compared with its forerunner. In twisting, we are also aiming high: A new drive concept and a new spindle technology with adapted spindle combinations is behind productivity increases of up to 30% and energy savings of up to 40% of our latest twisting machine compared to its predecessor.
Folini: Even employees with less advanced academic qualifications must be able to continue working effectively in the face of the progressing of electronic features in the machines. The great art of ergonomics consists in configuring the human-machine interface such that the equipment can be managed safely and without difficulty by workers on the factory floor. This includes self-explanatory menu structures, largely centralised control and monitoring, so the machine does not have to be adjusted and configured at a large number of different points.
Benjamin Mayer: In general, Mayer & Cie. invests 5 to 6% of its sales revenue in R&D. About 7% of its employees work in development and design. Our company is eager to subject its existing models and technologies to continuous improvements. This refers to reliability and productiveness as much as to resource and energy efficiency.
Mayer: All Mayer machines can be equipped with the oiler system SENSOBlueRS. This means they require significantly less fresh needle oil to run perfectly than knitting machines running on conventional systems that consume about 2.5 to 3 litres of oil a day on the basis of a 20-hour working day.
Mayer: The patented recycling process developed by Mayer & Cie. is based on cleaning and reusing needle oil that has already been used by the knitting machine in question. Used oil is cleansed of dirt particles in a filter unit housed in the machine and then returned to the machine’s oil circuit.
With SENSOBlueRS oil consumption can be reduced by up to 30%, depending on a machine.
Mayer: The Spinit 3.0 E, the first machine type to be equipped with Mayer & Cie. spinning and knitting technology, combines the three formerly separate processes spinning, cleaning and knitting. Rewinding is no longer required. The processes shortening leads to much lower energy consumption than the conventional manufacturing process would require.
Mayer: The 3-in-1 concept makes a new exclusive single jersey knitwear quality possible. We call it Spinit Jersey. It is made possible by the false-twist / zero-twist technology. The fabric has totally new properties: a soft and cosy touch, excellent evenness and luxurious sheen, no splices or knots and extraordinary physiological properties, i.e. heat retention.
Hans Gerhard Wroblowski: Energy is lost via hot exhaust gases, effluent and hot waste air (cylinder dryer) in particular. The handling of thermal energy, as well as raw materials, in an efficient and sustainable way is therefore currently a hot topic in the textile industry.
Wroblowski: We have been concentrating our R&D activities on developing energy-saving machine concepts and systems, focusing on efficient water and chemical apply units – the so-called Eco-application units. One of the latest developments is the Eco Applicator. This system comprises a new application technique and a highly efficient adjustable moistening system that enables - in combination with the latest developed combination system for skewing, stretching and drying - thermal energy and resources to be utilised in a target manner.
Wroblowski: The Eco Line system reduces energy losses and energy use, increases thermal transfer and keeps the drying energy on the textile material longer, i.e. so that it can be used very efficiently. In the shrinkage finishing process for basic and sensitive denim fabrics, for example, energy savings of up to 50 % can be achieved compared to state-of-the-art technology. The main advantages of Eco Line, the Eco Applicator respectively, is its potential to optimise the liquor applied, which is the result of using an individual use of two tangential application units in one.
Karl Hesse: Especially the caustic recovery plants help Körting not only to make production processes in the textile industry more sustainable, but also to decrease the operating costs significantly. The caustic recovery plants complement the existing production machines, the mercerising machines. Their only purpose is to recover the caustic soda used for mercerising at the end of the process. This recovered lye can then be returned to the process and no costly disposal is necessary, which helps to reduce environmental impact significantly. In addition, as these plants use the hot water generated by the process itself, they are extremely energy-efficient.
Hesse: Our system cleans the recovered lye, so that it can be re-used in the process without any loss of quality. When it is used together with another Körting product, the swirl droplet separator, the resulting vapour condensate is of excellent quality. Due to its low pH value, it can be used in other processes, e.g. for washing in the mercerisation machine and for bleaching. This means that we offer a closed circuit for lye and water, with nearly zero drain. Körting is highly diversified in these fields, so the customer can also benefit from our experience in exhaust gas treatment.
Hesse: Since we offer customised solutions, we are able to point out the financial savings at an early stage of the process. The most important factor is to reduce the plant operator’s lye consumption by 85%. As a consequence, hardly any waste water is generated any more, which reduces operating costs substantially. In any case, payback time is less than a year, in most cases only a few months, depending on the capacity. After that, the operating costs for mercerisation remain permanently low. Annual savings of one million euros are realistic. The larger the plant, the greater the saving potential.
Business intelligence for the fibre, textiles and apparel industries: technologies, innovations, markets, investments, trade policy, sourcing, strategy...
Find out more