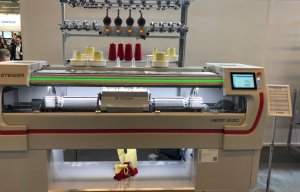
Steiger 3D knitting machine for technical textiles debuts at ITMA
Editor’s Viewpoint
The event that spanned seven days attracted over 105,000 visitors from 137 countries, chalking up new records for the exhibition.
10th July 2019
Billy Hunter
|
Barcelona
The event attracted over 105,000 visitors. © Innovation in Textiles
Themed Innovating the World of Textiles, the 18th edition of ITMA, the world’s largest and most established textile and garment technology exhibition, concluded successfully in Barcelona, Spain, last week, hosting 1,717 exhibitors from 45 countries. The event that spanned seven days attracted over 105,000 visitors from 137 countries, chalking up new records for the exhibition, which has been held every four years since 1951.
The show featured many exciting new product launches and innovative technologies and products, including those that leverage the Internet of Things. “The digital transformation of the textiles and garment manufacturing value chain and sustainability concerns of the industry have driven up visitor interests in ITMA 2019. We had a strong turnout, despite trade tensions and poor business sentiments,” commented Fritz P. Mayer, President of CEMATEX, the European Committee of Textile Machinery Manufacturers, and owner of ITMA and ITMA Asia.
The show featured many exciting new product launches. © Innovation in Textiles
“They were also impressed with presence of new visitor segments, such as bigger numbers of fashion and sports brands. Considering that for this ITMA edition, the exhibition duration has been shortened from 8 to 7 days, we still enjoyed good visitorship.” The top five countries where visitors came from were Spain, Italy, India, Turkey and Germany.
Many new technologies were launched, ranging from 3D weaving and knitting to hi-tech nonwovens processes, sustainable chemicals and state-of-the-art garment-making technologies, and wide range of software-powered automation solutions.
Italian company Santex Rimar Group introduced at ITMA its Sperotto Rimar Compas, a new frontier in compacting woven and knitted fabrics made in natural and blended fibres; Solwa Drywa green sludge dryer for efficient and cost-effective sludge management respecting environment and climate; and Santex Rimar Group Athena – advanced deep learning technologies.
eurolaser. © Innovation in Textiles
German manufacturer of high-end cutters eurolaser premiered the company’s patented Cut’n‘Protect Technology solution for the laser cutting of wool. During laser cutting, fibres “melt”, which provides the characteristic clean cutting edge. At the same time, laser cutting prevents the cut edge from fraying, so that the material can continue to be processed without the processing step of trimming. The unique benefit of the new technology is the elimination of the characteristic odour when laser cutting wool, and there has been a lot of interest from the company’s customers, according to Marcel Berger, Field Representative, Sales Department, eurolaser.
Cobble, a Vandewiele company based in the UK, introduced a number of innovations, including its most versatile tufting machine to date, the Colortec L+. It combines three advanced Cobble technologies in a single machine – ICN (individually controlled needle), IPD (individual pile delivery) and LCL (level cut/loop). This combination is designed to provide full design freedom for the production of multi-colour jacquard-type cut and loop wall-to-wall carpets, area rugs, and more.
In the area of technical textiles, the Flat Knitting team at Groz-Beckert, a German provider of industrial machine needles, presented a new special application needle that can handle a huge range of uses. The stability of the design reduces downtimes and boosts productivity. It also features special technical characteristics, such as a secure yarn insertion mechanism and reliable latch function – even when performing multi-thread knitting of solid loops using continuous filament yarn.
The common theme among the knitting machinery manufacturers at ITMA in Barcelona was the integration of the process stages and digitalisation, automatisation, as well as an ever-expanding range of applications for a variety of knitting technologies.
Shima Seiki. © Innovation in Textiles
Proposing knitting as an alternative manufacturing solution for non-fashion related industries, Japanese computerised flat knitting machinery manufacturer Shima Seiki demonstrated that what was impossible to knit in the past can now be knitted with its KNITification solutions. “Knitting offers great potential for technical textiles with its inherent characteristics: stretch and compression,” said Masaki Karasuno, Head of Corporate Communications at Shima. “Flat knitting provides further potential with its capability to shape fabric on the machine. New knitting techniques such as inlay made possible with special loop pressers featured on our new N.SVR-SP series machines add further value to knitting and have gained particular attention for its ability to produce hybrid knit-weave fabrics that allow insertion of technical yarns heretofore considered incompatible with knitting, into existing knit fabrics. These include carbon fibre, monofilament and even metallic yarns. Shima has even developed a special Yarn Unwinding Device for unwinding spools of technical yarn to ease yarn feed for such difficult-to-handle material.” Read more here – Shima Seiki sets out to KNITify the World.
Stoll. © Innovation in Textiles
Another global leader in flat knitting machinery Stoll, from Germany, returned to ITMA with a focus on new knitelligence networking solution, designed to play a key role industry wide, as each software tool solidifies the entire knitting process from design to production. The manufacturer also explored the topic of Stoll-knitrobotic – automated robotic functions during a knitting process, which will replace manual interventions without interruptions (like inserting non-textile elements as the item is being knitted). Demonstrations were performed on the ADF 530-32 ki W knitting machine in the gauge E18/16. In the sector of technical textiles, Stoll presented various demanding technical applications on the CMS 530 ki W in the gauge E7.2.
Santoni’s XT Machine. © Innovation in Textiles
Santoni, an Italian leader in the production of sock and pantyhose machines and a part of the Lonati group, celebrated its 100-year anniversary at the show. The company featured a diverse display for manufacturers of underwear, sportswear, beachwear, external, medical wear, denimwear, smart-textiles, socks and footwear, and more. The company presented its brand-new, patented XT Machine with its ingenious intarsia technology for efficient production of the shoe uppers, which is expected to hit the market in 2-3 months, according to Patrick Silva Szatkowski, Marketing Manager, Santoni. Also on show was the updated versatile Mec-Mor technology, known throughout the world as the only alternative range of machines that look circular but perform like a V-bed machine. This technology, displayed on 20 gauge, enables the production of weft double-face knitted garments with high quality designs and record production times. It is also used to produce accessories, such as 3D backpacks, where various yarns can be knitted into ad-hoc positioned areas, in order to obtain a seamless structure for superior product performance.
Mayer & Cie. © Innovation in Textiles
Also with a focus on digitalisation and versatility, German warp knitting machinery builder Mayer & Cie. put its digital offerings together under the name knitlink. The platform includes a web shop, remote maintenance options and recording and evaluation of machine data for the customer and is to be further expanded in the future. The company also premiered the OVJA 1.1 EETT premium jacquard machine, part of the focus on sports, and the Weftnit 3.2 machine study. Unlike common knitting machines, the Weftknit works with spring beard needles and the applications could be found in the automotive, swimwear, sports and leisurewear and outerwear sectors, as well as producing substrates for laminated fabrics.
“In view of the current situation of the textile machinery market the 2019 ITMA was, by and large, satisfactory,” said Benjamin Mayer, one of Mayer & Cie.’s two managing partners and the director in charge of sales. “Very positive trade fair experiences included the response to our digital offerings and the feedback about our Weftnit machine study. We were evidently already able to demonstrate at the development stage the advantages of the knitting method convincingly.”
Picanol, a Belgian high-tech weaving machines producer, exhibited 12 machines at the show, including the company’s brand-new airjet machine OmniPlus-i, which premiered at ITMA. It features a redesigned reed motion, optimised relay nozzle set up and can be combined with SmartShed, the fully electronically controlled shedding motion. “At Picanol, we believe that in this fast-changing world of weaving, the needs of weaving mills in general and the expectations of our customers and their operators are evolving rapidly,” said Frederic Dryhoel, Spokesperson & Corporate Communication Manager, Picanol Group. With the new machine, the company says it wanted to demonstrate that a machine can be performant, versatile, sustainable, digital and user-friendly at the same time.
Picanol. © Innovation in Textiles
Another weaving technology specialist Itema, from Italy, presented two new market launches, a never-before-seen weaving insertion concept and a series of weaving novelties. The new Itema airjet A9500-2bedsheeting has been developed to provide the most demanding bed sheeting weavers with an airjet weaving machine capable to reach the highest performances. Key machine components, such as main and tandem nozzles, have been redesigned along with the whole pneumatic platform. The second airjet weaving machine A9500-2 is the second generation of the Itema airjet A9500 and A9500p. Thanks to a new and optimised pneumatic platform, the weft insertion cycle is improved, leading to a quicker system response.
Itema. © Innovation in Textiles
The company also recently launched Itematech – the new division dedicated to technical textiles born as a result of the agreement signed with PTMT, with a product portfolio, which ranges from negative and positive rapier, to air-jet and projectile weaving machines.
German specialist Monforts presented an energy-optimised new version of its industry-leading Montex stenter for the first time at ITMA. With the introduction of the new MonforClean exhaust air treatment system and other unique process innovations, Monforts says it has been able to further reduce the energy consumption of Montex stenters by a further 13%. Exhaust air treatment on stenter frames has posed particular challenges over the years. In addressing this issue, Monforts is now incorporating the MonforClean module into the stenter frame, so there is no additional space requirement. The waste heat from the drying process is used to pre-heat the drying air, resulting in a radical reduction in the conventional heat supply required compared to gas and thermal oil heating. The further integration of an automatic exhaust air filter washing system automatically cleans the module elements.
Monforts Eco Applicator. © Innovation in Textiles
Imogo, a new Swedish company, introduced its new Dye-Max spray dyeing technology. While still at the prototype stage, the Dye-Max promises to slash the use of fresh water, wastewater, energy and chemicals by as much as 90%, compared to conventional jet dyeing systems. Its application unit consists of a closed chamber containing a series of spray cassettes with precision nozzles for accurate and consistent coverage, in combination with the patented imogo pro-speed valve that controls the volume to be applied.
Huntsman Textile Effects launched the high-performance digital ink ranges at the show. Novacron Advance ink is the next generation of reactive inks for cellulosics with outstanding shade depth and colour gamut, developed for the latest industrial digital printing machines. Eriofast Vista ink enables printers to achieve brilliant lasting designs on polyester/cotton blends. Using inks from this range enables printers to adopt a simple urea-free process with significantly reduced energy consumption, washing, machine maintenance and carbon dioxide emissions.
Mimaki. © Innovation in Textiles
Datacolor, a US leader in colour management technology, has collaborated with Adobe to launch a set of innovative tools at ITMA. The collaboration pairs Datacolor’s professional colour lookup tool ColorReaderPRO with Adobe’s newest plugin for Adobe Photoshop: Adobe Textile Designer. The integration of software allows designers to measure colour inspiration in the real world and transfer the data to Photoshop automatically via Bluetooth connection. “Adobe Textile Designer was conceived to help streamline the print design process,” said Mike Scrutton, Director of Print Technology and Strategy for Adobe’s Print & Publishing Business Unit. “We are excited to incorporate the ColorReaderPro into the solution to simplify the process of capturing inspiration colour for designers.”
Mimaki, a Japanese manufacturer of industrial wide-format inkjet printers, showed for the first time its brand-new hybrid digital textile printer, uniquely featuring both direct-to-textile and direct-to-transfer print capabilities. These features enable textile and garment manufacturers to achieve flexibility and enhanced application opportunities. The new printer also allows multiple sets of inks to be loaded simultaneously, supporting increased fabric range versatility and maximum product variety.
This year’s ITMA presented a strong sustainable denim, with a number of companies from different sectors demonstrating their approach to environmentally friendly denim production processes. Headquartered in Switzerland, Archroma, a leader in colour and specialty chemicals, has launched its new Diresul Smartdenim Blue, a liquid sulphur blue dye designed to mimic indigo. The new dye has a greener shade, better fastness to minimise back staining, and allows to create overall wash-downs much closer to actual indigo than any other dyestuff, whilst avoiding greyish cast especially in bleaching with hypochlorite, the company explains.
Among its Cadira modules, part of the company’s Resource Efficiency programme, DyStar, headquartered in Singapore, presented Cadira Denim, a dyeing technique for Indigo to reduce or eliminate the salt freight in wastewater streams, and Cadira Laundry. The company developed a range of auxiliaries for ultra-low liquor ratio machines using air for the processing of denim garments. With this technology, a variety of finishing effects on denim can be achieved saving a lot of water and energy.
Jeanologia. © Innovation in Textiles
The Spanish company Jeanologia exhibited the first complete production line that includes all its technologies and disruptive solutions. The process starts with G2Dynamic, which allows treatment of the fabric without using water and chemicals. It goes on to the Laundry 5.Zero garment finishing plant that guarantees zero pollution and obtains 85% saving in water. Laundry 5.Zero combines the following technologies: laser, G2 ozone, e-flow, Smart Boxes and H2Zero, the company’s first water recycling system; eliminating potassium permanganate, pumice stone, substances of concern and discharge from the textile finishing industry, as well as the manual processes of scraping and grinding.
Karl Mayer. © Innovation in Textiles
Karl Mayer, a German textile machinery manufacturer, remains on a growth path with its Denim Excellence Center at Karl Mayer Rotal. At ITMA 2019, Karl Mayer launched Greendye. The nitrogen technology ensures less environmental impact and more efficiency during indigo dyeing. With its high concentration in the dye bath and under nitrogen atmosphere, the dye diffuses and migrates more intensely into the fibre than in case of conventional procedures. The chemical consumption can be reduced considerably, a minus of 50% is possible when using hydrosulphite and caustic soda, and there is also less yarn waste. Karl Mayer took over the patents for the innovative indigo dyeing technology from Master in 2018.
Loepfe Brothers, a Swiss leader in yarn clearing technology, presented a brand-new yarn clearer – the YarnMaster Prisma. For the first time, it combines new and established sensor technologies in one device. Four sensor technologies interact intelligently to ensure fault visibility and data quality. As an extra benefit, Loepfe’s data management system MillMaster TOP 2.0 is an integral part of the new YarnMaster Prisma and complements every Loepfe yarn clearer installation.
Another Swiss company Uster Technologies launched five Value Modules for Uster Quality Expert quality management platform. The system connects, integrates, analyses and interprets vital quality information from every stage of the fibre-to-yarn process. The new modules are designed to give spinners an objective and accurate view of the entire spinning process, leading to higher yields and consistent quality.
James Heal, a British manufacturer, also launched a new collection of precision testing instruments at this year’s ITMA. AquAbrasion is a class-leading hybrid Martindale, which allows users to perform controlled wet abrasion testing for the first time. TruRain is a water repellency tester, allowing users to test for this in a tightly controlled and repeatable way. ProDry provides insight into evaporation. Finally, WickView is a state-of-the-art instrument that uses an advanced imaging system to track and record the transfer of moisture through a garment.
ITMA 2019 also provided the platform for the announcement of a comprehensive modernisation programme for Egypt’s textiles industry valued at around EUR 1 billion from exhibitors including Benninger, Brückner, EFI Reggiani, Itema, Karl Mayer, Rieter, Savio and Thies.
In addition, a number of ITMA and co-located events drew over 1,000 delegates. Among the events were the ITMA-EDANA Nonwovens Forum, Textile Colourant and Chemical Leaders Forum, Better Cotton Initiative Seminar, European Digital Textile Conference, Tex-Summit Global, Planet Textiles, SAC & ZDHC Manufacturer Forum and Texmeeting by TEXFOR.
ITMA also collaborated with supporting organisations, many of which sent visiting delegations from Central Asia, South Asia, Turkey and the Mediterranean countries. “We are extremely glad that many industry stakeholders see ITMA as an excellent platform for collaboration and sharing of ideas to make the industry more competitive in the face of digital transformation and to explore cutting-edge solutions to future proof their business,” said Charles Beauduin, Chairman of ITMA Services, which organises ITMA 2019.
The next ITMA will be held in Fiera Milano, Milan, from 8-14 June 2023.
Further reading
ITMA 2019 sets new record with biggest number of exhibitors
Thank you for reading Innovation in Textiles,
Jana Bukolovska
Deputy Editor
Billy Hunter is away
Business intelligence for the fibre, textiles and apparel industries: technologies, innovations, markets, investments, trade policy, sourcing, strategy...
Find out more