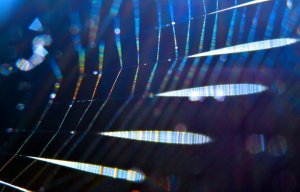
Searching for the battleship steel version of spider silk
Van der Waals forces – the adhesive forces that also enable geckos to stick to walls – make handling nanofibres extremely difficult.
24th March 2021
Innovation in Textiles
|
Geneva, Switzerland
Research and development will be a big component of the forthcoming INDEX™2020 exhibition, which now takes place in Geneva from October 19-22.
In the event’s latest newsletter, details are published of an intriguing project involving the exhibitor Elmarco – a leading supplier of nanofibre manufacturing technology worldwide.
Even comparatively straightforward processing operations such as spooling or winding are complicated when it comes to nanofibres, the company explains.
Their attraction to any surface by van der Waals forces – the adhesive forces that also enable geckos to stick to walls – makes handling them extremely difficult, and this is an issue that may well be hampering the wider adoption of nanofibres, however useful their many properties, especially in combination with nonwoven substrates for fields such as filtration.
The calamistrum comb
The BioCombs4Nanofibers Project takes its inspiration from the humble spider in seeking a solution to this problem.
Coordinated by the University of Linz in Austria, and involving universities in Czech Republic, Germany, Greece and Romania as well as Elmarco, the project aims to recreate the ‘calamistrum’– a comb specific to certain spiders.
Cribellate spiders such as the feather-legged lace weaver, for example, use their calamistrum to handle and process the nanofibres they naturally produce.
They make up to 40,000 sticky nanofibres in thicknesses of 10-30nm from their cribellum – a spinning plate close to the spinnerets. To be able to handle such extremely fine nanofibres, the cribellate spiders use the calamistrum on their hindmost legs. This comb allows cribellate spiders to create a sticky capture spiral from the nanofibres to their nets – which interacts and captures the prey very effectively – without sticking to the spider itself.
Why the calamistrum is non-adhesive towards these fine nanofibres is still elusive and the clarification of these properties – as well as its technical abstraction for technical nanofibre processing – is the aim of the project.
A further goal is to transfer these bionic comb structures to technical surfaces featuring anti-adhesive properties, that will enable improved future tools for nanofibre handling. Similar nanostructures can also hinder the adhesion of nanofibrous protrusions of cells or microorganisms, which may also lead to the creation of cell-repellent or antiseptic areas on medical devices and implants.
Advanced laser-induced nanostructures are currently being employed to mimic the fingerprint-nanostructures of the cribellate spiders.
Nanospider
The commercially-available Nanospider systems manufactured by Elmarco are now characterised by significant improvements to this nozzle-less technology.
The Elmarco machine employs stationary string electrodes supplied with polymer solution by a proprietary moving “painting” head. This results in a dramatic decrease of solvent evaporation during the process, which has to be removed from the exhaust air released from the machine. The polymer solution concentration is also stable, enabling the system to typically run for more than 24 hours.
There are now over 200 Elmarco Nanospider nanofibre nonwoven units in commercial operation worldwide.
Business intelligence for the fibre, textiles and apparel industries: technologies, innovations, markets, investments, trade policy, sourcing, strategy...
Find out more